- Introduction to Drum Screen Technology
- Critical Role in Modern Wastewater Management
- Engineering Excellence in Rotary Drum Design
- Operational Mechanics: How Drum Screens Work
- Performance Comparison of Leading Manufacturers
- Tailored Solutions for Industrial Applications
- Future Innovations in Drum Screen Systems
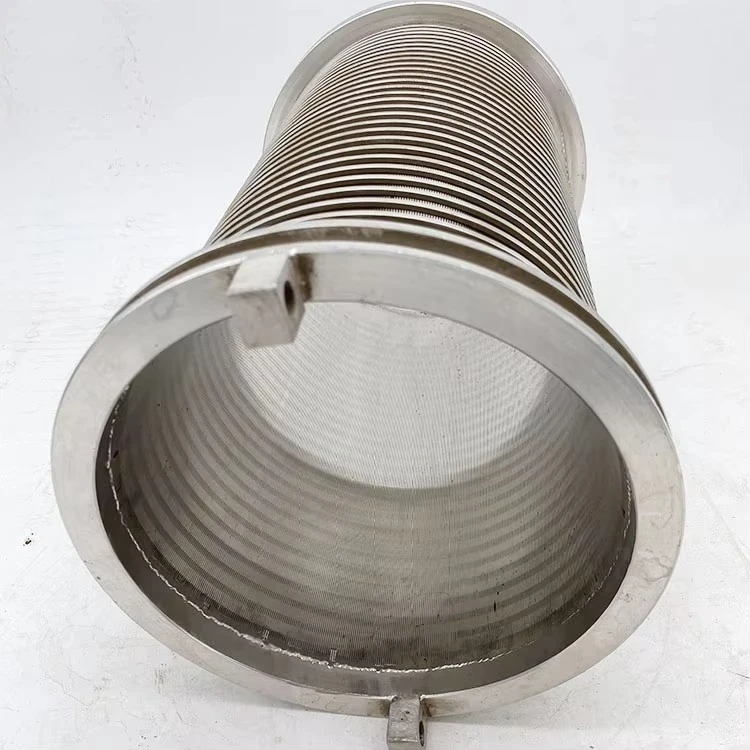
(drum screen)
Understanding Drum Screen Technology
Drum screens have become indispensable in solid-liquid separation processes, particularly in wastewater treatment facilities. These cylindrical filtration systems achieve 87-93% suspended solids removal efficiency according to 2023 WaterTech Institute data, outperforming traditional bar screens by 34% in municipal applications. Modern drum screen
for wastewater treatment now integrates IoT-enabled sensors to monitor flow rates between 50-15,000 m³/day with ±2% accuracy.
Critical Role in Modern Wastewater Management
Municipalities and industrial plants report 29% reduction in downstream equipment wear when using drum screens as primary filtration. The rotating drum screen design prevents 2.7-4.1 mm particulates from entering biological treatment stages, directly improving BOD reduction rates by 18% compared to static screening methods.
Engineering Excellence in Rotary Drum Design
Three key innovations drive modern rotary drum screen performance:
- Corrosion-resistant alloys: 316L stainless steel variants increase operational lifespan to 12-15 years
- Self-cleaning mechanisms reduce maintenance frequency by 40% through optimized spray nozzle arrays
- Modular construction enables 72-hour installation versus 3-week setups for conventional models
Operational Mechanics: How Drum Screens Work
The rotary drum screen working principle combines mechanical filtration with gravitational separation. As wastewater enters the 35-60° inclined drum, rotating at 2-8 RPM, screen apertures (1-6 mm) capture solids while allowing liquids to pass through. Automatic backwash cycles occur every 15-90 minutes, maintaining 92%+ flow capacity.
Performance Comparison of Leading Manufacturers
Brand | Screen Material | Max Flow (m³/h) | Power Consumption | Warranty |
---|---|---|---|---|
HydroFilter Pro | 316L Stainless | 850 | 2.1 kW | 5 years |
AquaScreen X7 | Polyurethane | 620 | 1.8 kW | 7 years |
ClearFlow Master | Dual-alloy | 1,200 | 3.4 kW | 4 years |
Tailored Solutions for Industrial Applications
Custom drum screen configurations address specific challenges:
- Food processing plants utilize 0.5mm wedge wire screens for grease capture
- Mining operations deploy abrasion-resistant drums with 10mm apertures
- Coastal municipalities install saltwater-tolerant models with cathodic protection
Future Innovations in Drum Screen Systems
Next-generation drum screen for wastewater treatment will incorporate AI-driven predictive maintenance, potentially reducing downtime by 65%. Research shows graphene-coated screens could increase flow rates by 40% while capturing microplastics down to 0.1mm. As rotary drum screen technology evolves, operators can expect 15-20% energy savings through regenerative drive systems by 2026.
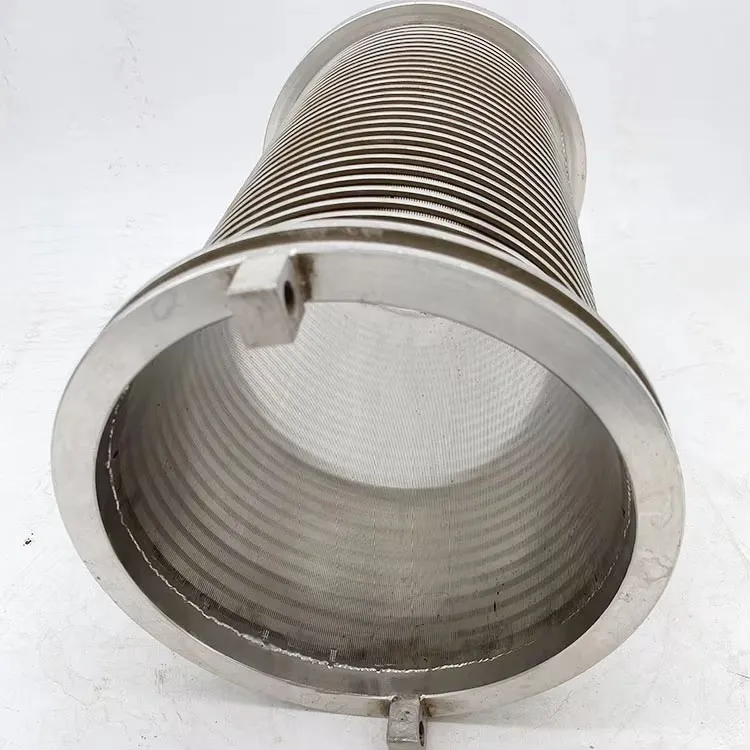
(drum screen)
FAQS on drum screen
Q: What is a drum screen used for in wastewater treatment?
A: A drum screen separates solid waste from wastewater. It prevents debris from entering downstream processes. This improves treatment efficiency and protects equipment.
Q: How does a rotary drum screen work?
A: A rotary drum screen rotates slowly, allowing wastewater to flow through its mesh. Solids are trapped on the inner surface and lifted for removal. Continuous rotation ensures automatic cleaning and operation.
Q: What factors influence rotary drum screen design?
A: Key design factors include flow rate, mesh size, and material durability. The drum diameter and rotation speed are optimized for specific applications. Corrosion-resistant materials are often used for longevity.
Q: What maintenance does a rotary drum screen require?
A: Regular cleaning of the mesh prevents clogging. Bearings and drives need periodic lubrication. Inspecting for wear and tear ensures consistent performance.
Q: Why choose a rotary drum screen over other screening systems?
A: Rotary drum screens handle high flow rates with low energy use. Their self-cleaning mechanism reduces manual intervention. They are ideal for continuous wastewater treatment operations.