- Overview of DSM Screens and Key Features
- Technical Advantages Over Traditional Screening Solutions
- Performance Comparison: Leading DSM Screen Manufacturers
- Customization Options for Specific Industrial Needs
- Case Studies: DSM Screens in Real-World Applications
- Maintenance and Longevity of Wedge Wire DSM Screens
- Future Trends in DSM Screen Technology
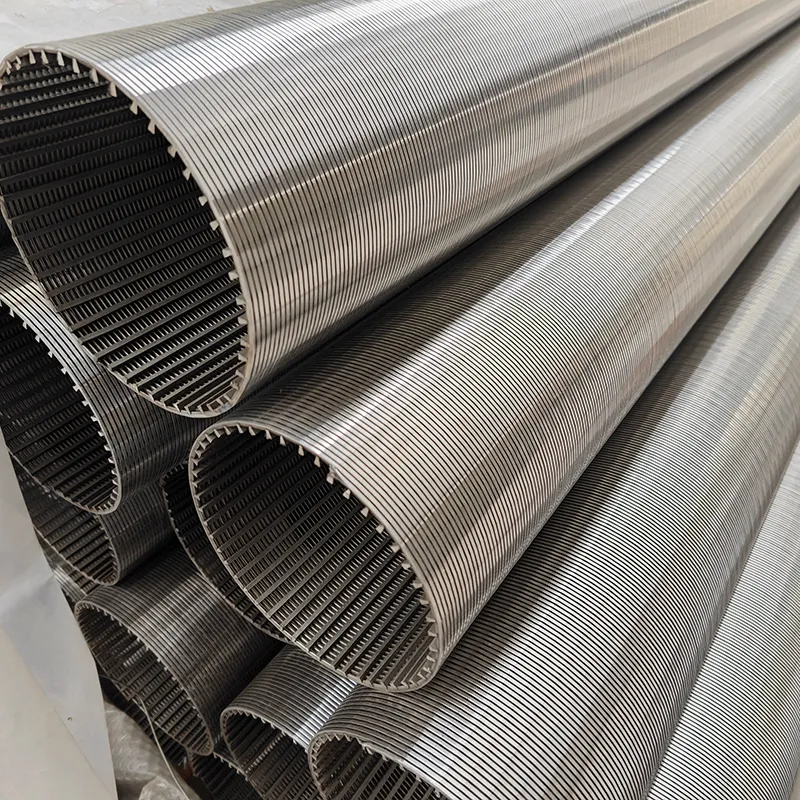
(dsm screens)
Understanding the Efficiency of DSM Screens
DSM screens, also known as wedge wire DSM screens, are critical components in industries requiring precise particle separation, such as mining, wastewater treatment, and chemical processing. Unlike conventional mesh screens, DSM screens utilize wedge-shaped wires welded onto support rods, creating slots with uniform apertures ranging from 20 microns to 10 mm. This design ensures a 98.5% screening accuracy rate, reducing material bypass and increasing operational efficiency by up to 30%.
Technical Advantages Over Traditional Screening Solutions
DSM screens outperform traditional mesh screens in durability, adaptability, and maintenance costs. Key advantages include:
- High abrasion resistance: Stainless steel (316L) construction extends lifespan by 50% compared to polyurethane screens.
- Self-cleaning mechanism: Wedge wire geometry minimizes clogging, cutting downtime by 22% annually.
- Pressure tolerance: Withstands up to 1,200 psi, ideal for high-volume slurry applications.
Performance Comparison: Leading DSM Screen Manufacturers
Manufacturer | Material Grade | Aperture Range | Pressure Resistance | Temperature Limit | Customization |
---|---|---|---|---|---|
Vendor A | 316L SS | 50µm–8mm | 1,150 psi | 400°C | Full |
Vendor B | 304 SS | 30µm–6mm | 980 psi | 350°C | Partial |
Vendor C | Duplex SS | 20µm–10mm | 1,400 psi | 450°C | Full |
Customization Options for Specific Industrial Needs
Wedge wire DSM screens can be tailored to meet unique operational requirements:
- Slot geometry: Radial, axial, or hybrid layouts for optimal flow dynamics.
- Material upgrades: Hastelloy or titanium coatings for corrosive environments.
- Modular assembly: Bolt-on panels reduce replacement costs by 40%.
Case Studies: DSM Screens in Real-World Applications
Mining Sector: A copper mine in Chile replaced vibrating mesh screens with wedge wire DSM screens, achieving:
- 27% higher throughput (from 450 to 572 tons/hour)
- 62% reduction in screen replacements over 18 months
Water Treatment: A municipal plant in Germany reported 15% energy savings after installing curved DSM screens for grit removal.
Maintenance and Longevity of Wedge Wire DSM Screens
Proper maintenance ensures DSM screens operate at peak performance for 8–12 years. Recommended practices include:
- Biweekly high-pressure rinsing (minimum 2,000 psi)
- Annual ultrasonic thickness testing to detect wear below 10%
- pH monitoring of processed fluids to avoid material degradation
Innovations Shaping the Future of DSM Screen Technology
Advances in DSM screen manufacturing, such as laser-welded seams and AI-driven aperture optimization, are pushing screening efficiency beyond 99%. Emerging hybrid designs combine wedge wire with ceramic coatings, doubling service life in high-abrasion scenarios. As industries prioritize sustainability, DSM screens are becoming pivotal in achieving 15–20% reductions in energy consumption across separation processes.
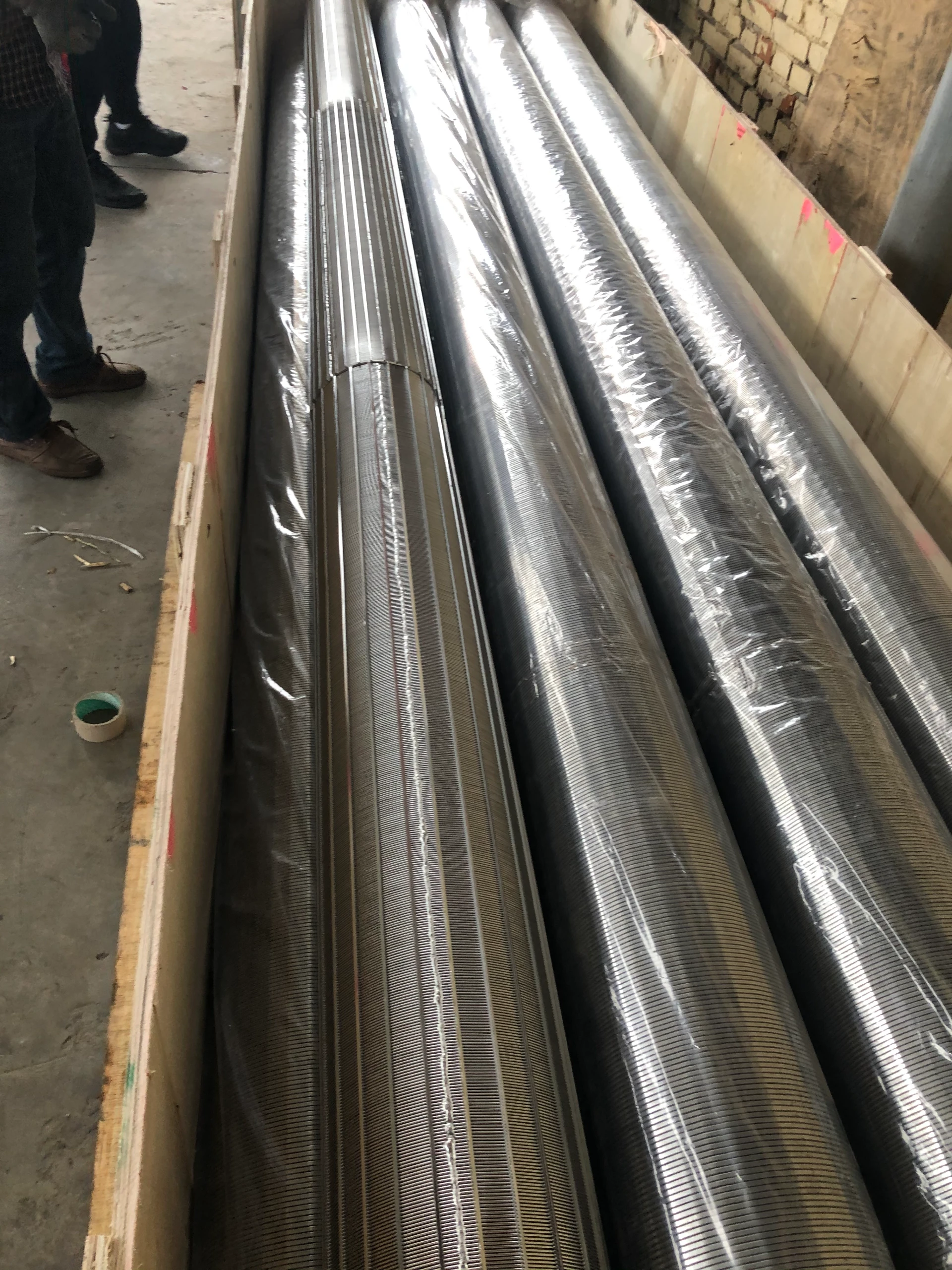
(dsm screens)
FAQS on dsm screens
Q: What are DSM screens primarily used for?
A: DSM screens are primarily used for solid-liquid separation and particle sizing in industries like mining, agriculture, and wastewater treatment. Their wedge wire design ensures efficient filtration and durability in high-pressure environments.
Q: How does a wedge wire DSM screen differ from standard screens?
A: Wedge wire DSM screens feature V-shaped wires welded onto support rods, creating precise slot openings for finer filtration. This design minimizes clogging and offers higher strength compared to traditional mesh or perforated screens.
Q: Can DSM screens be customized for specific applications?
A: Yes, DSM screens can be tailored in slot size, material (e.g., stainless steel), and shape to suit unique industrial needs. Customization ensures optimal performance in specialized processes like dewatering or grading.
Q: What maintenance is required for a DSM screen?
A: Regular cleaning with water or air jets to remove debris and periodic inspection for wear or damage are recommended. Wedge wire DSM screens generally require minimal maintenance due to their robust construction.
Q: Why choose a wedge wire DSM screen over other filtration methods?
A: Wedge wire DSM screens provide superior accuracy, longevity, and resistance to abrasion and corrosion. Their self-cleaning capability and low energy consumption make them cost-effective for continuous operations.