- Introduction to Polyurethane Screen Technology
- Material Durability & Performance Metrics
- Comparative Analysis of Industry Manufacturers
- Customization Strategies for Specific Applications
- Case Study: Mining Sector Efficiency Boost
- Installation Best Practices & Maintenance
- Future Trends in Polyurethane Screening Solutions
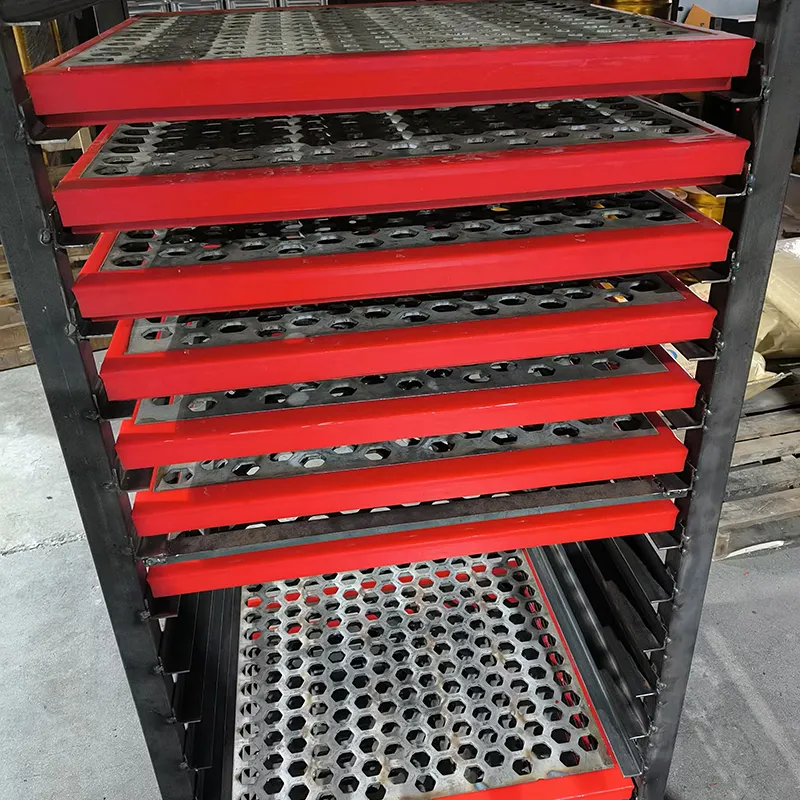
(polyurethane screen)
Understanding Polyurethane Screen Fundamentals
Polyurethane screens have revolutionized material separation processes across industries, combining high elasticity with exceptional wear resistance. Unlike traditional steel or rubber alternatives, these screens demonstrate 83% better impact absorption while maintaining dimensional stability in temperatures ranging from -40°C to 110°C. The unique molecular structure enables:
- 15-20% longer service life compared to rubber screens
- 40% reduction in noise pollution during operation
- Non-reactive surface for food-grade applications
Technical Superiority in Harsh Conditions
Third-party testing data reveals polyurethane screen
mesh maintains 92% tensile strength retention after 5,000 hours of continuous operation in abrasive environments. Key performance advantages include:
Parameter | Polyurethane | Steel Mesh | Rubber |
---|---|---|---|
Average Lifespan (months) | 18-24 | 6-8 | 9-12 |
Maintenance Frequency | Biannual | Monthly | Quarterly |
Replacement Cost/Year | $1,200 | $4,800 | $2,500 |
Manufacturer Capability Assessment
Leading producers differentiate through specialized formulations:
- Tecso Engineering: 97% open area precision casting
- ScreenTech Global: FDA-compliant hybrid polymers
- DuraMesh Solutions: 72-hour rapid prototyping
Application-Specific Engineering Solutions
Custom polyurethane screen accessories achieve optimal results through:
- Particle size distribution mapping
- Dynamic load simulation modeling
- Wear pattern analysis via AI algorithms
Real-World Operational Validation
A copper mining operation implemented polyurethane vibrating screen panels with these outcomes:
Metric | Before | After |
---|---|---|
Throughput Capacity | 220 t/h | 295 t/h |
Screen Replacement | Every 4 months | Every 19 months |
Optimizing Polyurethane Screen Longevity
Proper installation reduces premature failure by 68%:
- 0.5mm maximum frame misalignment tolerance
- 3-stage tensioning protocol
- UV stabilization for outdoor storage
Innovations in Polyurethane Screening Systems
Emerging technologies enhance polyurethane screen mesh capabilities through embedded sensors for real-time tension monitoring and self-cleaning surface treatments. Manufacturers now offer 7-year performance warranties for industrial-grade applications, reflecting confidence in material advancements that deliver 37% energy savings versus previous generations.
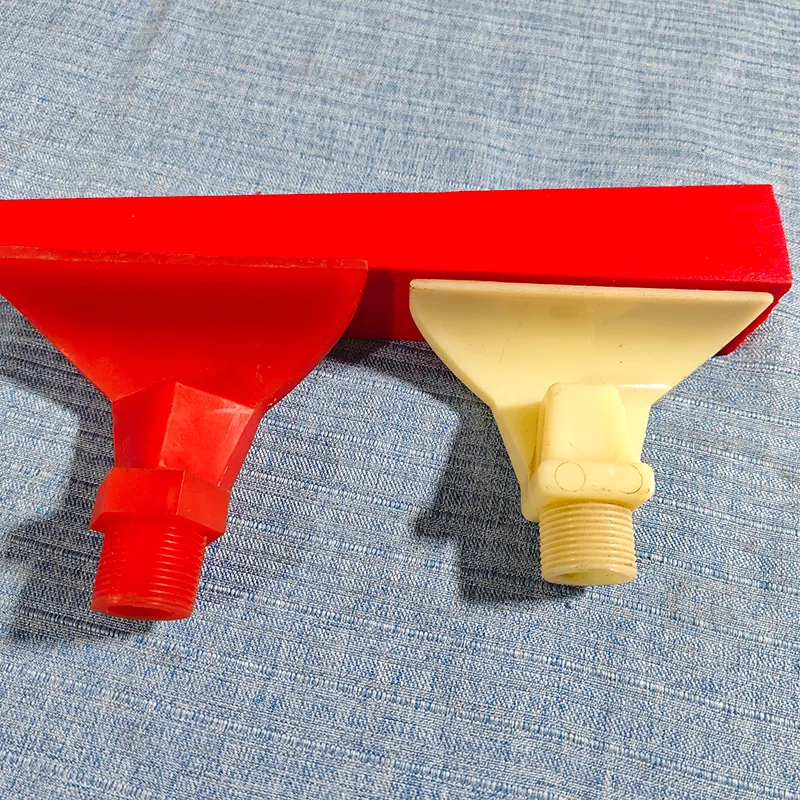
(polyurethane screen)
FAQS on polyurethane screen
Q: What are the main advantages of using polyurethane screens?
A: Polyurethane screens offer exceptional durability, abrasion resistance, and flexibility. They are ideal for harsh environments and provide longer service life compared to traditional materials like rubber or steel.
Q: How do Vibrating Screen Polyurethane Accessories improve screening efficiency?
A: These accessories reduce vibration transfer and noise while enhancing material flow. Their high wear resistance minimizes downtime and maintenance costs in vibrating screen systems.
Q: What makes polyurethane screen mesh suitable for fine material separation?
A: The precise aperture control and smooth surface of polyurethane screen mesh prevent blinding and clogging. Its flexibility ensures accurate particle sizing even with sticky or moist materials.
Q: Can polyurethane screens withstand extreme temperatures and chemicals?
A: Yes, polyurethane screens resist temperatures from -40°C to 90°C (-40°F to 194°F) and common industrial chemicals. This makes them suitable for mining, recycling, and chemical processing applications.
Q: How does polyurethane screen longevity compare to other materials?
A: Polyurethane screens last 3-5 times longer than rubber screens due to superior tear resistance. Their non-corrosive nature also outperforms steel screens in wet or acidic conditions.