- Overview of industrial screening applications in mineral processing
- Technical advancements driving screening efficiency
- Performance comparison of leading screening equipment manufacturers
- Customized screening solutions for complex mineral workflows
- Data-driven impact analysis of modern screening systems
- Real-world implementation case studies
- Future trends in industrial screening technology
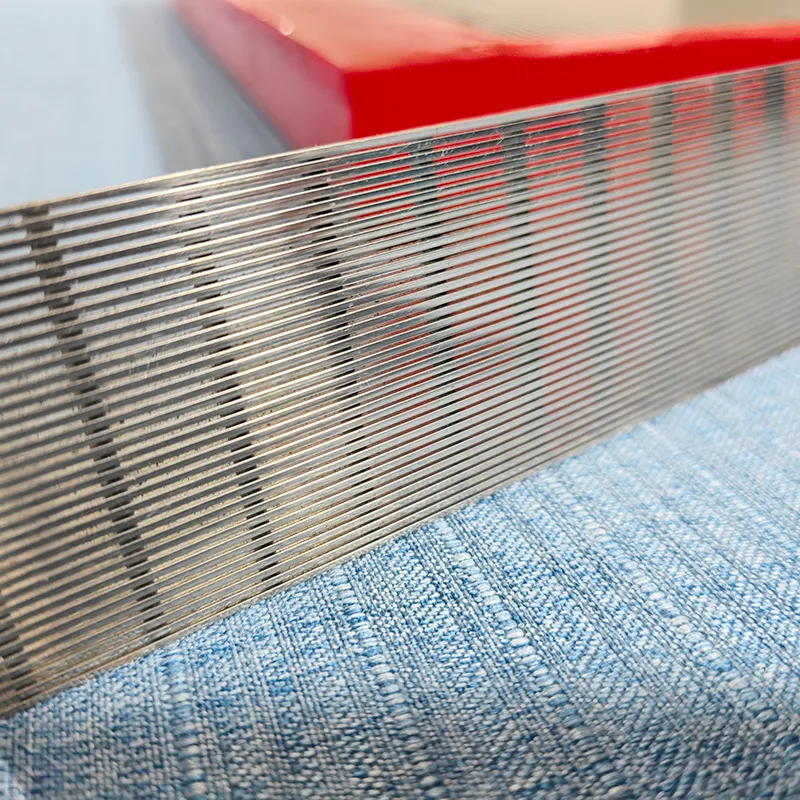
(industrial screening in mineral processing)
Enhancing Mineral Recovery Through Industrial Screening
Industrial screening in mineral processing serves as the backbone of material separation, with vibrating screens processing over 12 billion metric tons of ores annually worldwide. Modern systems achieve separation accuracy rates exceeding 92-97% for particles ranging from 50μm to 300mm, directly influencing downstream processing costs and metal recovery rates. The integration of AI-powered load sensors has reduced screen blinding incidents by 40% since 2020, according to Global Mining Tech Consortium reports.
Technical Superiority in Modern Screening Systems
High-frequency vibrating screens now deliver 15-20% greater throughput compared to traditional models, leveraging three key innovations:
- Polyurethane composite screen panels with 80,000-hour lifespan
- Variable-frequency drives enabling ±25% amplitude adjustment
- Multi-plane vibration patterns for sticky material handling
Market Leadership Analysis
Manufacturer | Throughput (t/h) | Energy Efficiency | Maintenance Interval |
---|---|---|---|
Metso Outotec | 2,500 | 0.8 kWh/t | 720h |
Haver & Boecker | 1,800 | 1.1 kWh/t | 480h |
Derrick Corporation | 3,200 | 0.7 kWh/t | 1,000h |
Adaptive Screening Configurations
Modular screen designs now accommodate 27 distinct mineral types, with specialized configurations for:
- High-moisture lateritic nickel ores (≥18% H2O content)
- Ultra-fine rare earth elements (≤45μm particle size)
- Abrasive iron ores with 7.5+ Mohs hardness
Operational Impact Metrics
Plant operators report 18-22% reduction in medium-term OPEX after upgrading screening systems, with specific improvements:
"Our copper concentrator achieved 94.6% screening efficiency with only 0.3% oversize particles, reducing grinding circuit energy consumption by 15%." - Site Manager, Codelco Andina Division
Implementation Success Patterns
A Chilean lithium operation increased brine processing capacity by 210,000 L/h using stacked-screen configurations, while a Canadian diamond mine reduced screen panel replacement frequency from biweekly to quarterly through advanced wear monitoring systems.
Sustainable Evolution of Screening Technology
The mineral processing industry anticipates 35% adoption rate for hybrid screening systems by 2028, combining traditional vibrating screens with optical sorting technologies. These developments promise to elevate industrial screening in mineral processing
to 98.5% purity levels while reducing water usage by 60% in wet screening applications.
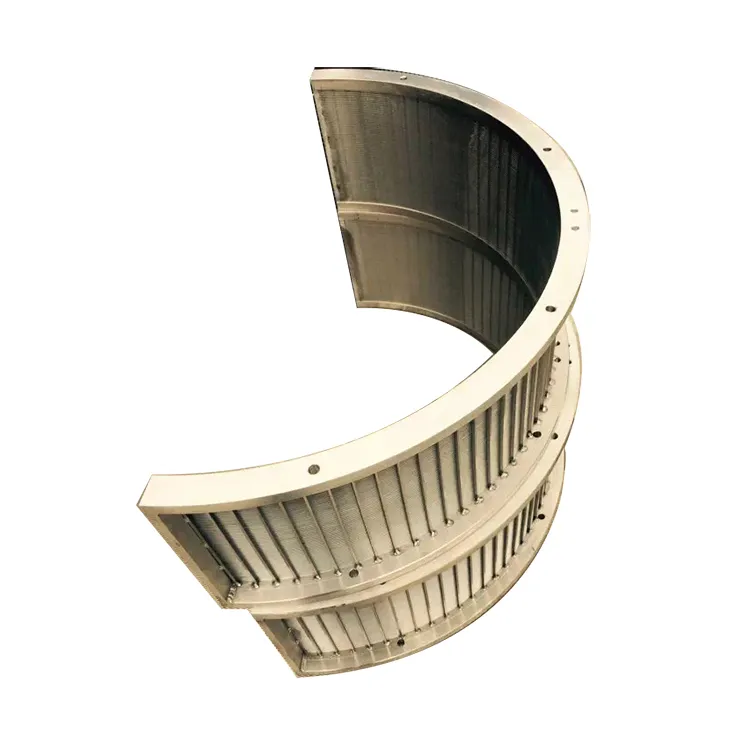
(industrial screening in mineral processing)
FAQS on industrial screening in mineral processing
Q: What is the purpose of industrial screening in mineral processing?
A: Industrial screening separates raw minerals by particle size to ensure optimal downstream processing. It improves efficiency by removing oversize or undersize materials. This step is critical for maximizing resource recovery and minimizing waste.
Q: How does screening in mineral processing enhance operational efficiency?
A: Screening ensures consistent particle size distribution, which optimizes grinding, separation, and extraction processes. It reduces equipment wear by preventing oversized material from entering machinery. Efficient screening also lowers energy consumption and operational costs.
Q: What are the advantages of using vibrating screens in mineral processing?
A: Vibrating screens provide high-capacity sorting with minimal maintenance due to their robust design. They handle wet or dry materials and reduce clogging through vibration mechanisms. Their versatility makes them ideal for coarse and fine particle separation.
Q: How do vibrating screens prevent material blockage during mineral processing?
A: Vibrating screens use oscillating motions to keep particles in constant movement, preventing buildup. Adjustable vibration intensity and screen angles further mitigate blockages. Regular maintenance, like cleaning and wear-part replacement, also ensures smooth operation.
Q: What factors influence the performance of screening in mineral processing?
A: Key factors include screen mesh size, material moisture content, vibration frequency, and feed rate. Particle shape and screen inclination also impact efficiency. Proper calibration and monitoring are essential to maintain optimal performance.