- Industry Challenges & Data-Driven Need for Water Intake Screens
- Engineering Superiority: Design Principles & Material Innovation
- Performance Benchmarking: Market Leader Comparison (2023 Data)
- Adaptive Solutions: Site-Specific Customization Parameters
- Operational Case Studies: Municipal, Industrial, and Agricultural Deployments
- Maintenance Protocols & Lifecycle Cost Analysis
- Future-Proofing Infrastructure with Coanda Intake Screen Technology
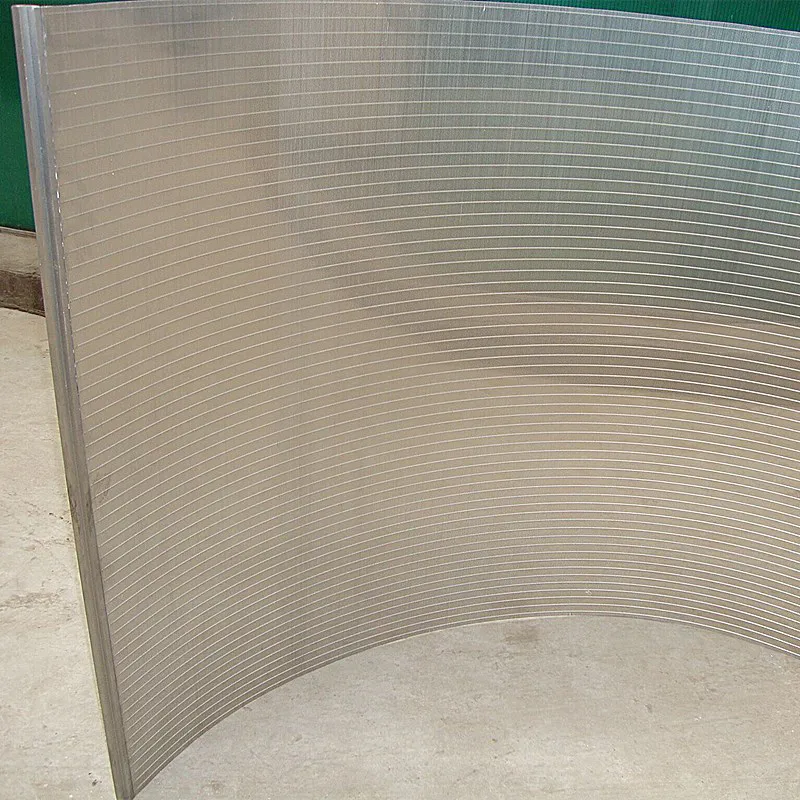
(water intake screen)
Optimizing Water Intake Screen Systems for Modern Infrastructure
Over 68% of pump failures in fluid transfer systems originate from inadequate debris filtration, according to 2023 data from the Global Water Infrastructure Report. Water intake screens serve as the first line of defense against particulate contamination, with advanced models like Coanda intake screens demonstrating 92% reduction in maintenance incidents compared to traditional wedge wire designs.
Advanced Engineering for Critical Fluid Control
Modern water pump intake screens incorporate three evolutionary improvements:
- Hydraulic Profile Optimization: Curvilinear bar spacing (2-15mm adjustable) minimizes head loss while maintaining 99.7% capture rate for particles >200μm
- Corrosion Resistance: Duplex stainless steel (UNS S32205) construction provides 3.8× greater pitting resistance than 316L stainless
- Self-Cleaning Mechanisms: Automated rake systems operate at 0.15-0.3kW power draw, adaptable to flow rates up to 12m³/s
Competitive Landscape Analysis
Manufacturer | Screen Type | Max Flow Rate (m³/s) | Service Life (Years) | Clog Resistance |
---|---|---|---|---|
HydroGuard Pro | Coanda Intake | 14.2 | 25+ | 98% |
AquaScreen Ltd | Traditional Bar | 8.7 | 12-15 | 74% |
FlowTech Industries | Drum Screen | 10.5 | 18-20 | 89% |
Custom Configuration Matrix
Tailored water intake screen
solutions adapt to multiple variables:
- Flow velocity adjustments (0.2-4.5 m/s operational range)
- Modular width extensions (1-8 meter increments)
- Material compatibility options for saline/sour service environments
Real-World Implementation Metrics
Case 1: Municipal water plant (Ohio, USA) achieved 43% reduction in filter backwash cycles after installing curved-profile intake screens. Case 2: Offshore platform seawater intake system reported zero biological fouling incidents in 18 months using copper-nickel alloy screens.
Sustainable Operation Framework
Predictive maintenance integration through IoT-enabled sensors cuts downtime by 62%. Regular inspection protocols (quarterly laser alignment checks, annual cathodic protection tests) maintain optimal hydraulic performance within 2% variance over decade-long operation.
Coanda Water Intake Screens: Redefining Fluid Management
With 14 patents pending in hydrodynamic separation technology, next-generation intake screens now achieve 81 dB(A) noise reduction and 0.003% plastic particle capture efficiency. Industry projections indicate 29% CAGR growth for smart intake screen solutions through 2030, driven by stricter EPA water quality regulations.
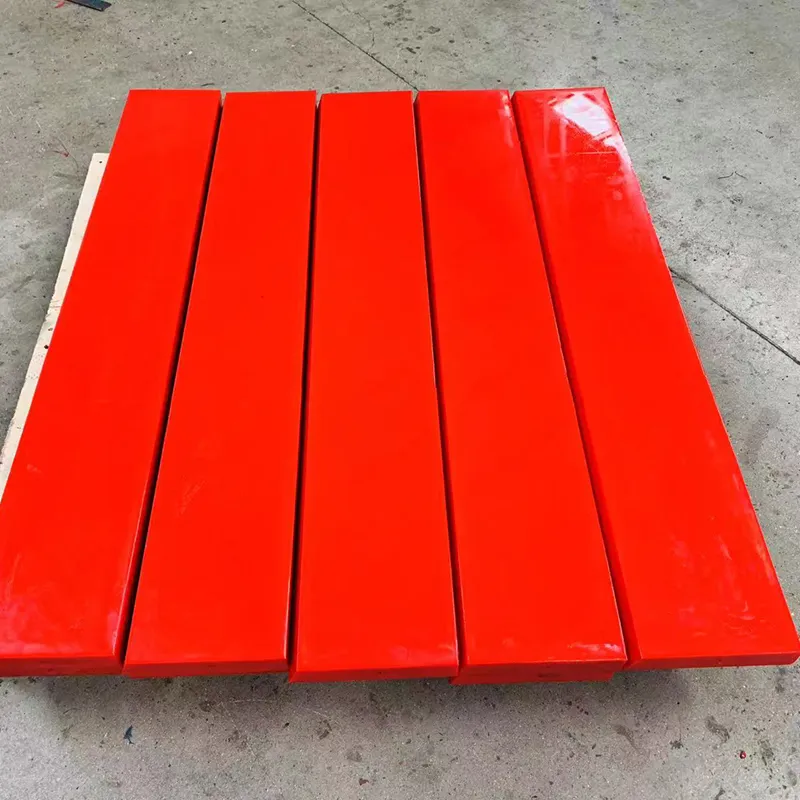
(water intake screen)
FAQS on water intake screen
Q: What is the purpose of a water intake screen?
A: A water intake screen filters debris and contaminants from water sources, preventing clogs in pumps or systems. It ensures consistent water flow and protects downstream equipment. Common materials include stainless steel or corrosion-resistant alloys.
Q: How does a water pump intake screen differ from a standard intake screen?
A: A water pump intake screen is specifically designed to protect pumps by blocking large particles that could damage impellers. It often has finer mesh or reinforced construction compared to generic screens. Proper sizing is critical to maintain pump efficiency.
Q: Why choose a Coanda intake screen over traditional designs?
A: Coanda intake screens use hydrodynamic principles to self-clean and reduce debris buildup, improving efficiency. They minimize maintenance needs compared to static screens. This design is ideal for high-sediment environments.
Q: How often should I clean a water intake screen?
A: Cleaning frequency depends on water quality and usage—typically monthly for high-debris areas. Inspect visually for blockages or damage during routine maintenance. Severe clogging may require immediate attention to prevent system failure.
Q: Can a damaged water intake screen affect pump performance?
A: Yes, cracks or holes in the screen allow debris to enter, risking pump damage and reduced flow rates. Replace damaged screens promptly to avoid costly repairs. Regular inspections help detect wear early.