- Understanding the Mechanism of Self-Cleaning Wedge Wire Screens
- Technical Advantages Over Traditional Screening Solutions
- Comparative Analysis of Leading Manufacturers
- Customization Options for Diverse Industrial Needs
- Real-World Applications and Case Studies
- Key Performance Metrics and Data Insights
- Why Invest in Self-Cleaning Wedge Wire Screen Technology?
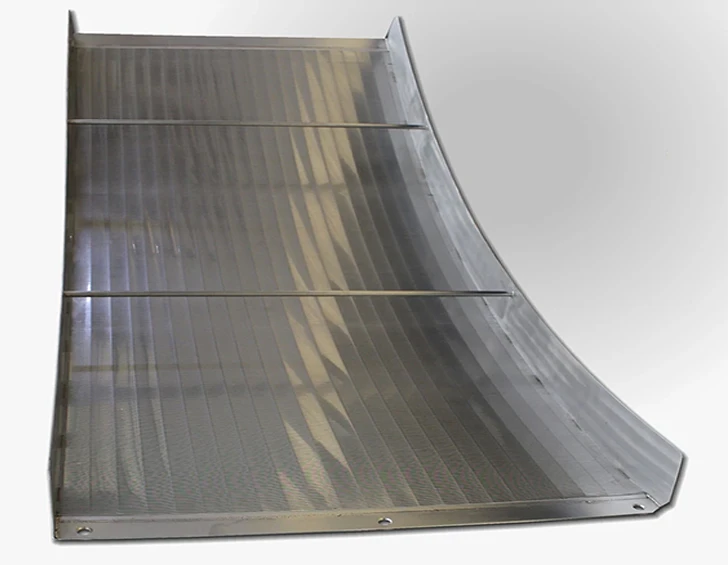
(self cleaning wedge wire screen)
Understanding the Mechanism of Self-Cleaning Wedge Wire Screens
Self-cleaning wedge wire screens utilize a unique V-shaped profile to prevent particle buildup, ensuring continuous operation in high-load environments. The design combines precision-welded stainless steel wires with uniform slot openings, enabling efficient filtration of liquids and solids. Unlike flat wire mesh, the wedge wire’s tapered geometry creates a scraping effect during material flow, reducing maintenance downtime by up to 60%.
Technical Advantages Over Traditional Screening Solutions
These screens outperform conventional mesh in durability and efficiency. Key benefits include:
- High Open Area (30-50%): Facilitates faster throughput while minimizing pressure drop.
- Corrosion Resistance: Constructed from 316L or duplex stainless steel for harsh chemical environments.
- Temperature Tolerance: Operates reliably between -40°C to 550°C.
Comparative Analysis of Leading Manufacturers
Manufacturer | Open Area (%) | Material Options | Max Pressure (PSI) |
---|---|---|---|
Vee-Wire | 45 | 304SS, 316SS | 1,500 |
Gap Technology | 38 | Duplex, Hastelloy | 2,200 |
Screenex | 42 | 316L, Titanium | 1,800 |
Customization Options for Diverse Industrial Needs
Tailored configurations address specific operational challenges:
- Slot Sizes: Ranging from 25 microns to 25 mm
- Surface Finishes: Electropolished, sandblasted, or coated
- Modular Designs: Bolt-on panels for rapid replacement
Real-World Applications and Case Studies
In mining operations, self-cleaning wedge wire screens reduced sludge dewatering costs by 22% at a Chilean copper plant. A municipal water treatment facility in Germany achieved 99.7% silt removal efficiency using 100-micron screens, cutting backwash cycles by 40%.
Key Performance Metrics and Data Insights
Independent tests demonstrate:
- 98% retention rate for particles above slot size
- 0.03 mm tolerance in wire spacing
- 15-year lifespan in moderate-corrosion environments
Why Invest in Self-Cleaning Wedge Wire Screen Technology?
Adopting self-cleaning wedge wire screens translates to long-term operational savings and enhanced process reliability. Industries report an average ROI of 18 months through reduced energy consumption (12-18%) and lower maintenance costs. With adaptable designs meeting ISO 9044 standards, these screens future-proof critical filtration systems.
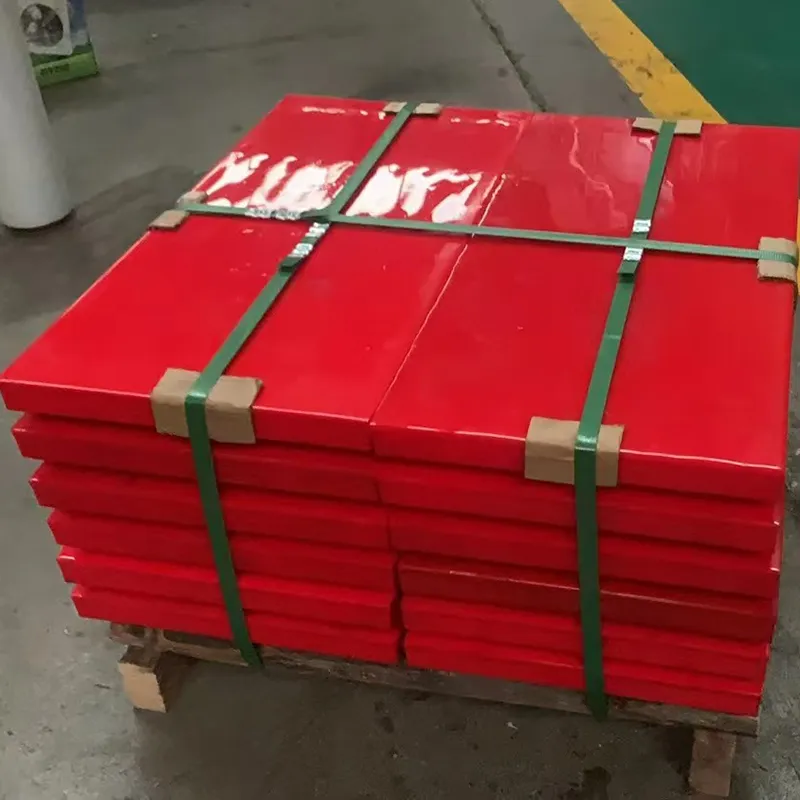
(self cleaning wedge wire screen)
FAQS on self cleaning wedge wire screen
Q: What is a self-cleaning wedge wire screen?
A: A self-cleaning wedge wire screen is a filtration device with V-shaped wires that prevent debris buildup. Its design allows continuous material flow while automatically clearing blockages. It’s ideal for high-solid or sticky substance applications.
Q: How does self-cleaning wire mesh work?
A: The angled profile of wedge wires creates a scraping effect during operation, dislodging trapped particles. Fluid or material flow enhances the cleaning action. This minimizes manual maintenance and downtime.
Q: Where are self-cleaning screen meshes commonly used?
A: They are widely used in wastewater treatment, mining, agriculture, and food processing. Their durability suits harsh environments like slurry separation or dewatering. Industries prioritize them for efficiency and low upkeep.
Q: What maintenance does a self-cleaning wedge wire screen require?
A: Routine inspections for wear or damage are recommended. Periodic flushing with water or air may be needed for stubborn residues. Generally, its design reduces intensive maintenance compared to traditional screens.
Q: Why choose wedge wire over standard mesh for self-cleaning?
A: Wedge wire’s V-shaped gaps resist clogging better than flat-woven mesh. The structural strength handles higher pressures and abrasive materials. Its longevity and efficiency justify the initial investment.