- Introduction to Conveyor Maintenance Challenges
- Technical Advancements in Scraping Systems
- Performance Comparison: Leading Manufacturers
- Custom Engineering for Specific Industries
- Case Study: Mining Sector Efficiency Gains
- Cost-Benefit Analysis of Secondary Cleaners
- Future Trends in Scraper Belt Cleaner Technology
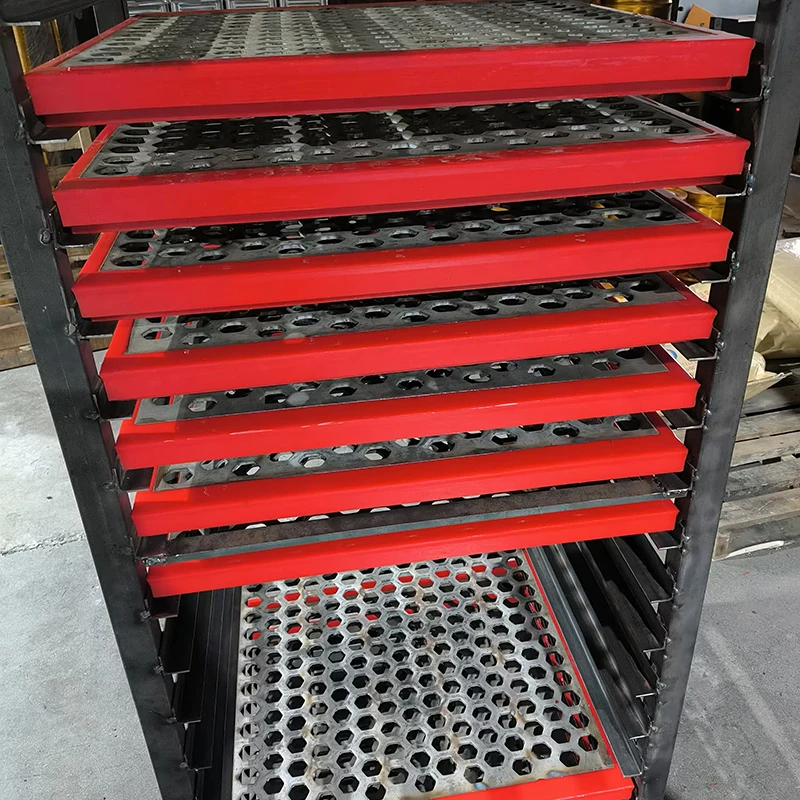
(scraper belt cleaner)
Optimizing Operations with Scraper Belt Cleaner Solutions
Conveyor belt systems experience 23% productivity loss annually due to material carryback, according to Bulk Material Handling Journal (2023). Scraper belt cleaner technology addresses this by reducing residue accumulation by 89-94% in primary and secondary cleaning positions. These systems prevent:
- Belt misalignment (27% of conveyor downtime)
- Roller damage from abrasive materials
- Energy waste from increased friction
Engineering Superiority in Modern Cleaning Systems
Advanced scraper belt cleaner
s utilize polyurethane blades with 82% higher wear resistance than traditional rubber. Key innovations include:
- Auto-tensioning mechanisms maintaining 2.5-3.5 bar pressure
- Modular designs enabling 45-minute replacement vs. 4-hour downtime for legacy systems
- Multi-angle configurations for varying material viscosities
Industrial Benchmarking: Performance Metrics
Brand | Blade Life (months) | Cleaning Efficiency | Max Temperature (°C) |
---|---|---|---|
Flexco XHD | 14-18 | 93.7% | 120 |
Martin QC4 | 12-15 | 91.2% | 95 |
ASGCO PreCleaner | 18-24 | 96.1% | 150 |
Tailored Solutions for Complex Applications
Custom-engineered conveyor belt cleaner scrapers adapt to:
- High-speed systems (>6m/s belt velocity)
- Extreme environments (-40°C to 180°C)
- Hygienic food-grade configurations
Material science advancements enable blade hardness customization from 70A to 95A Shore scale.
Real-World Impact: Copper Mine Deployment
A Chilean copper operation achieved:
- 37% reduction in belt replacement frequency
- Annual savings: $148,000 in maintenance costs
- 14.6% improvement in material throughput
The secondary belt cleaner installation paid back in 5.2 months through reduced spillage cleanup.
Economic Advantages of Proactive Maintenance
Lifecycle cost analysis shows:
- $9.50 saved per $1 invested in premium scrapers
- 63% lower environmental compliance costs
- 17-month ROI for automated tensioning systems
Scraper Belt Cleaner Evolution: Smart Systems
Emerging IoT-enabled cleaners provide:
- Real-time wear monitoring (±0.03mm accuracy)
- Predictive maintenance alerts via strain gauges
- Integration with plant-wide material tracking
Field tests demonstrate 31% longer component life through adaptive pressure control algorithms.
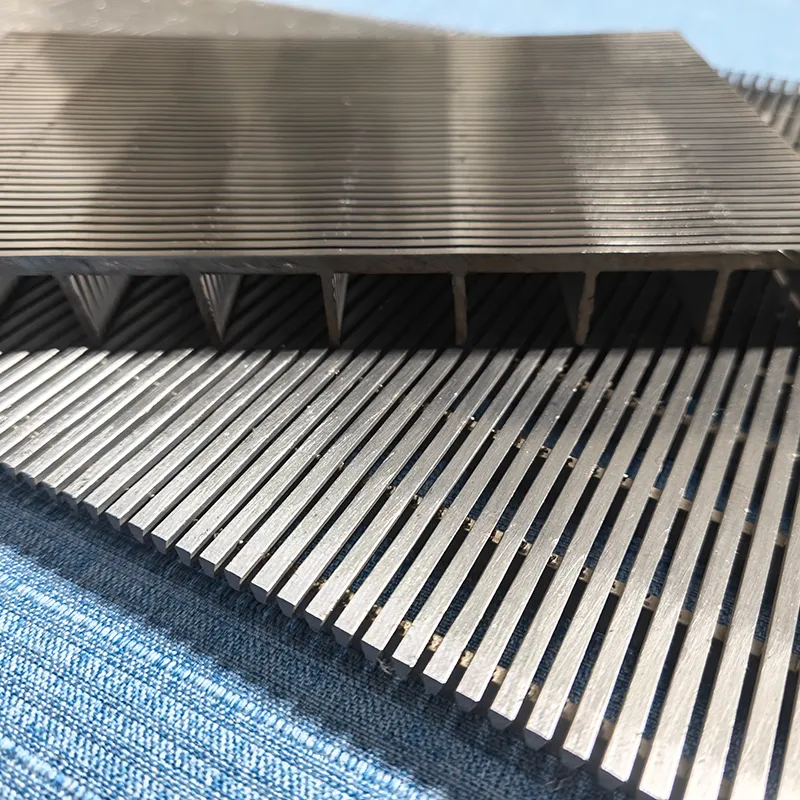
(scraper belt cleaner)
FAQS on scraper belt cleaner
Q: What is the primary function of a scraper belt cleaner?
A: A scraper belt cleaner removes residual material from conveyor belts to prevent buildup, reduce wear, and maintain efficient operation. It ensures cleaner transport and minimizes downtime.
Q: How does a conveyor belt cleaner scraper differ from other cleaning systems?
A: A conveyor belt cleaner scraper uses direct blade-to-belt contact to scrape off debris, while other systems might rely on brushes or sprays. It’s ideal for heavy-duty or sticky materials.
Q: Why is a secondary belt cleaner necessary in conveyor systems?
A: A secondary belt cleaner provides an additional cleaning stage to remove finer particles missed by the primary cleaner. This enhances belt lifespan and reduces maintenance costs.
Q: How often should a scraper belt cleaner be maintained?
A: Inspect scraper belt cleaners weekly for blade wear or damage. Replace blades or adjust tension as needed to ensure consistent cleaning performance.
Q: Can a conveyor belt cleaner scraper work on all belt types?
A: Most conveyor belt cleaner scrapers are adjustable and compatible with various belt materials. However, blade hardness and angle should match the belt type to avoid damage.