- Understanding Vibrating Screen Deck Fundamentals
- Technical Advantages in Material Separation
- Performance Comparison: Single vs Double Deck Models
- Manufacturer Benchmarking Analysis
- Custom Engineering Solutions
- Industry Application Case Studies
- Optimizing Vibrating Screen Deck Operations
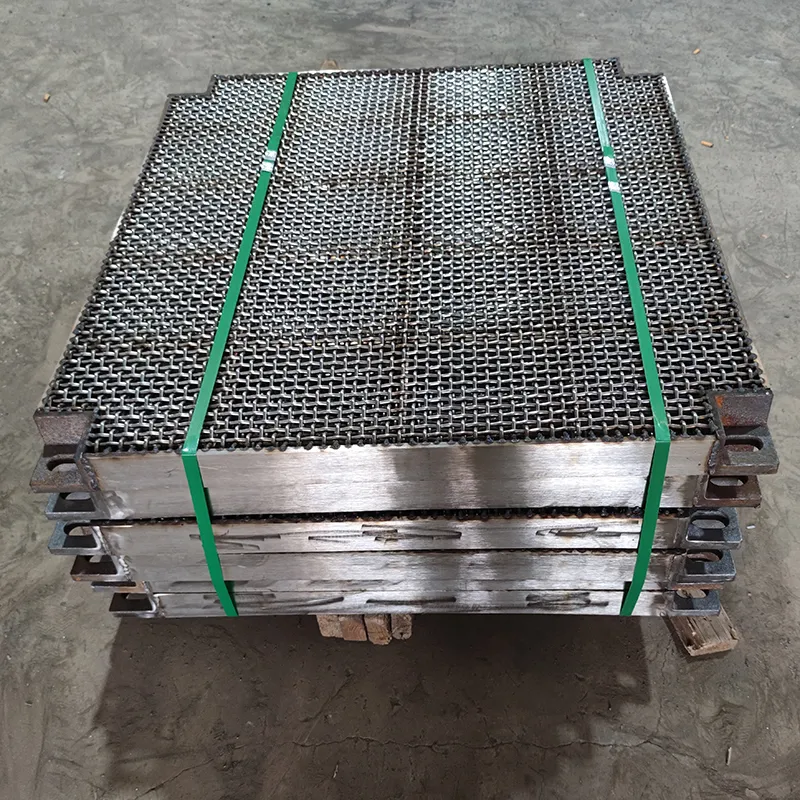
(vibrating screen deck)
Understanding Vibrating Screen Deck Fundamentals
Vibrating screen decks form the backbone of modern material classification systems, with single deck vibrating screen configurations handling basic sorting tasks while double deck vibrating screen setups enable multi-stage particle separation. These systems typically process 50-800 tons/hour depending on material density and screen aperture sizes. The deck structure - whether single or multiple layers - directly impacts sorting efficiency, with modern designs achieving 92-97% material separation accuracy.
Technical Advantages in Material Separation
Advanced deck vibration mechanisms employ dual counter-rotating motors generating 4.5-7.5 G-force, significantly outperforming traditional eccentric weight systems. Key innovations include:
- Modular deck assemblies allowing rapid media changeovers (45-60 minute replacement)
- Polyurethane screen surfaces with 3X lifespan vs steel wire alternatives
- Variable-frequency drives (0-25Hz adjustability) for precise material control
Performance Comparison: Single vs Double Deck Models
Parameter | Single Deck | Double Deck |
---|---|---|
Throughput Capacity | 50-300 TPH | 200-800 TPH |
Particle Separation Stages | 1 | 2-3 |
Floor Space Required | 12-18 m² | 15-22 m² |
Power Consumption | 5.5-15 kW | 11-30 kW |
Manufacturer Benchmarking Analysis
Leading manufacturers demonstrate distinct technical profiles:
Vendor | Deck Type | Max Acceleration | Weight (kg) |
---|---|---|---|
Company A | Modular | 6.2G | 4,200 |
Company B | Fixed | 5.8G | 3,850 |
Company C | Hybrid | 7.1G | 4,500 |
Custom Engineering Solutions
Specialized applications require tailored configurations:
- High-moisture material handling: 5° downward deck inclination
- Abrasive environments: Tungsten-carbide deck coatings
- Food-grade applications: FDA-compliant polyurethane surfaces
Industry Application Case Studies
Recent deployments demonstrate operational impacts:
- Quarry Operation: 22% throughput increase with dual deck system
- Recycling Plant: 98.7% metal recovery using customized deck apertures
- Agriculture: 40% energy reduction through variable-speed deck drives
Optimizing Vibrating Screen Deck Operations
Proper maintenance of vibrating screen deck
components extends service intervals by 60-80%. Critical practices include:
- Monthly bearing lubrication (NLGI 2 grease)
- Quarterly tension checks (35-40N/mm² for polyurethane decks)
- Annual motor alignment verification (±0.05mm tolerance)
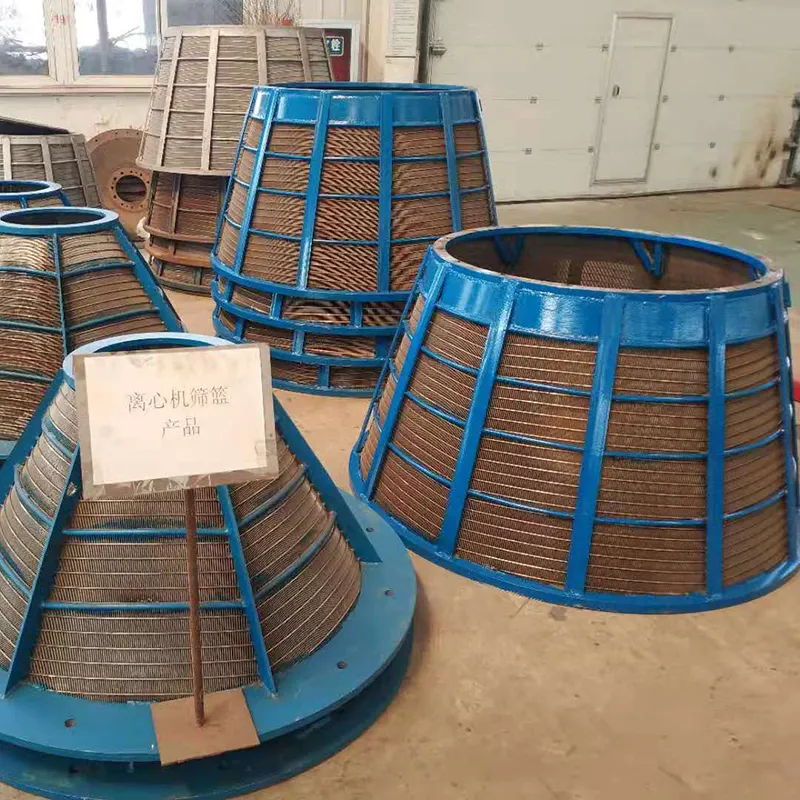
(vibrating screen deck)
FAQS on vibrating screen deck
Q: What is the primary difference between a single deck and double deck vibrating screen?
A: A single deck vibrating screen has one screening surface, ideal for basic material separation, while a double deck vibrating screen features two stacked decks, enabling simultaneous multi-size grading or scalping.
Q: What applications are best suited for a single deck vibrating screen deck?
A: Single deck vibrating screens are commonly used for high-volume material removal of oversized particles, preliminary screening in aggregates, or simple sorting in recycling and mining operations.
Q: How does deck configuration impact vibrating screen efficiency?
A: Deck configuration determines throughput and precision—single decks prioritize speed for coarse screening, while double decks enhance accuracy by separating materials into multiple size fractions in one cycle.
Q: What maintenance is required for vibrating screen decks?
A: Regular inspection of screen meshes for wear, tightening of fasteners, and lubrication of bearings are critical to maintain optimal performance and extend the vibrating screen deck's lifespan.
Q: Can vibrating screen decks handle wet or sticky materials?
A: Yes, specialized decks with features like rubber-coated screens, high-frequency vibration, or water spray systems can effectively process wet or adhesive materials without clogging.