- Introduction to Perforated Screen Plates
- Technical Advantages and Performance Metrics
- Comparative Analysis of Leading Manufacturers
- Customization Options for Diverse Applications
- Industry-Specific Use Cases and Success Stories
- Maintenance and Longevity Best Practices
- Final Considerations for Optimal Selection
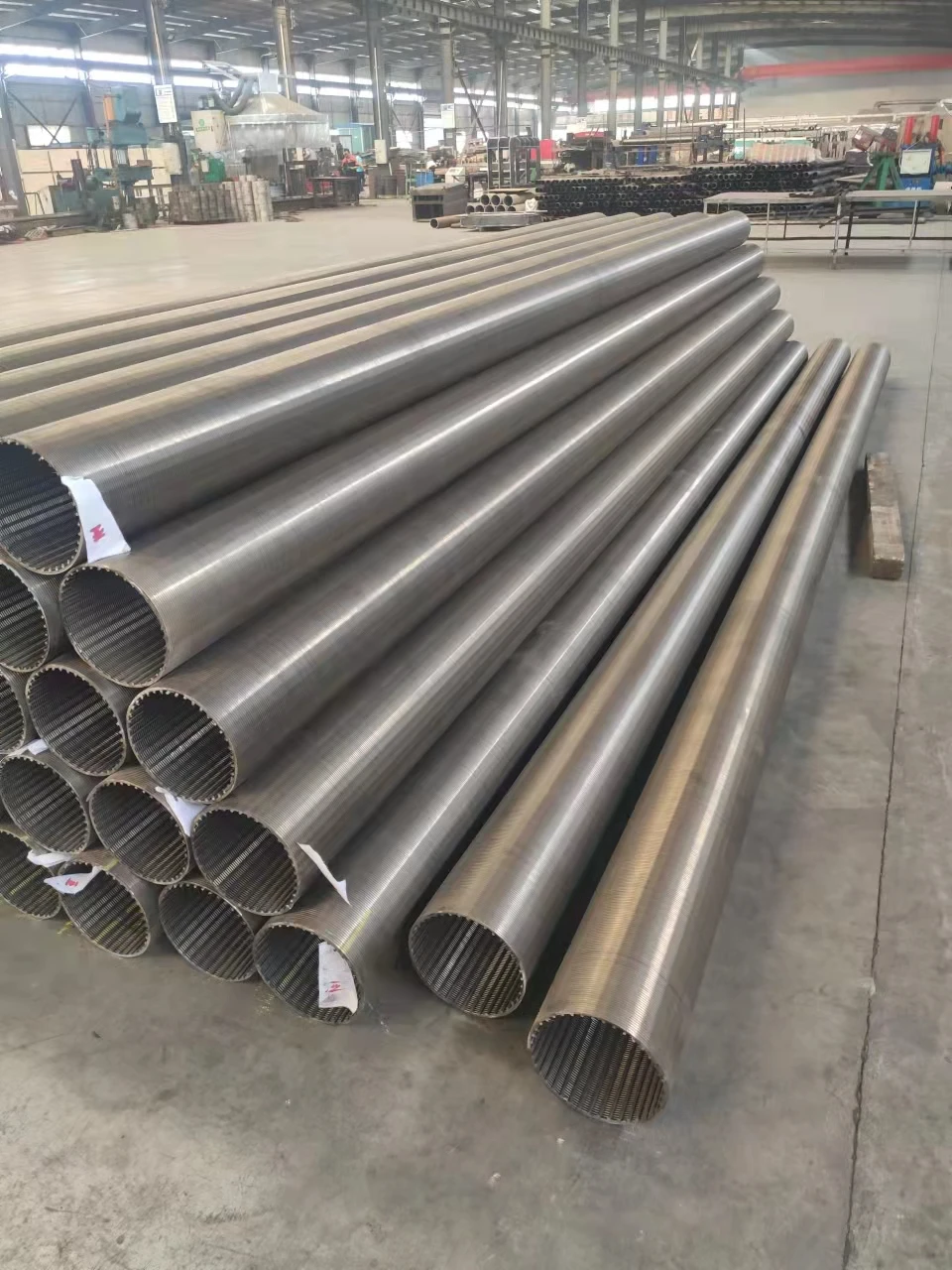
(perforated screen plate)
Understanding the Role of Perforated Screen Plates in Modern Industry
Perforated screen plates, including variants like perforated plate screens and PU plates, are critical components across filtration, separation, and material processing systems. Engineered with precision-drilled apertures, these plates enable efficient particle sorting, airflow regulation, and liquid drainage. Industries such as agriculture, mining, and wastewater management rely on their ability to balance durability (withstand 50-400 MPa pressure) and precision (tolerance levels as low as ±0.05mm).
Technical Advantages and Performance Metrics
Modern perforated screen plate
s demonstrate:
- 98.6% filtration efficiency in particle sizes ranging 0.1-25mm
- Corrosion resistance exceeding ASTM G48 standards
- Operational lifespan of 8-15 years under continuous use
Advanced laser-cutting techniques enable complex hole patterns while maintaining structural integrity, reducing material waste by 22% compared to traditional stamping methods.
Manufacturer Comparison and Product Specifications
Brand | Hole Size Range | Material Grade | Pressure Resistance | Price/㎡ (USD) |
---|---|---|---|---|
ScreenTech Pro | 0.5-20mm | 316L Stainless | 380 MPa | $245 |
PerfPlate Masters | 1-30mm | Carbon Steel | 250 MPa | $180 |
UltraPU Solutions | 2-15mm | Polyurethane | 120 MPa | $310 |
Customization for Specialized Operational Needs
Adaptable configurations include:
- Variable hole geometries (round, square, hexagonal)
- Multi-layer composite designs
- Anti-clogging surface treatments
Custom-engineered solutions account for 34% of industrial orders, particularly in pharmaceutical manufacturing requiring FDA-compliant materials.
Real-World Applications and Operational Results
Case Study 1: Cement Plant Screening System
Installation of wedge wire screens reduced maintenance intervals from weekly to quarterly, increasing throughput by 18%.
Case Study 2: Food Processing Facility
PU plate implementation decreased product loss by 6.2% through improved drainage efficiency.
Preserving Functional Integrity Over Time
Routine maintenance protocols:
- Ultrasonic cleaning every 500 operational hours
- Eddy current testing for micro-crack detection
- Surface recoating at 5-year intervals
Why Perforated Screen Plates Remain an Industry Staple
The evolution of perforated screen plate technology continues to address industrial challenges, with recent innovations offering 41% greater energy efficiency in separation processes compared to 2018 benchmarks. When specifying these components, engineers must balance initial costs against total lifecycle value – premium-grade materials typically demonstrate 27% lower cost-per-ton over decade-long service periods.
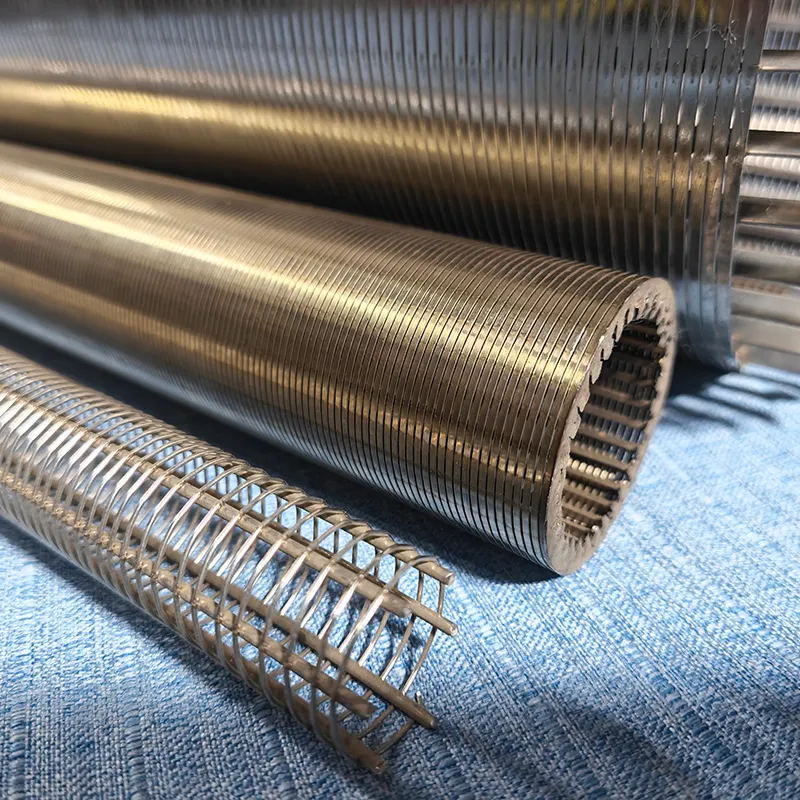
(perforated screen plate)
FAQS on perforated screen plate
Q: What is a perforated screen plate used for?
A: A perforated screen plate is designed for material separation, filtration, or sizing in industries like mining, agriculture, and construction. Its holes allow desired particles to pass while blocking larger debris. It’s also used for ventilation and noise reduction.
Q: How does a perforated plate screen differ from a standard sieve?
A: A perforated plate screen has precisely sized and shaped holes for consistent material sorting, while standard sieves often use woven mesh. The plate’s durability and rigid structure make it ideal for heavy-duty applications compared to flexible mesh screens.
Q: What materials are used to make PU plates for screening?
A: PU (polyurethane) plates are made from flexible, wear-resistant polyurethane, ideal for damp or abrasive environments. They resist clogging and provide longer service life than metal screens in certain conditions, such as wet mineral processing.
Q: Can perforated screen plates be customized for specific applications?
A: Yes, perforated screen plates can be tailored in hole size, pattern, and material (e.g., stainless steel, PU). Customization ensures optimal flow rates, durability, and efficiency for unique industrial needs like food processing or wastewater treatment.
Q: Why choose a PU plate over a metal perforated screen plate?
A: PU plates offer superior resistance to corrosion, noise, and impact, making them suitable for wet or chemically harsh environments. They also reduce material adhesion, minimizing downtime for cleaning compared to metal alternatives.