- Understanding the Role of Screen Casing Pipes in Modern Well Systems
- Material Innovation and Durability Standards
- Performance Metrics: Pressure Resistance vs. Environmental Stress
- Market Leaders: Technical Specifications Compared
- Tailored Solutions for Diverse Geological Conditions
- Case Study: Efficiency Gains in Agricultural Water Systems
- Future-Proofing Infrastructure with Advanced Screen Casing Pipe Technology
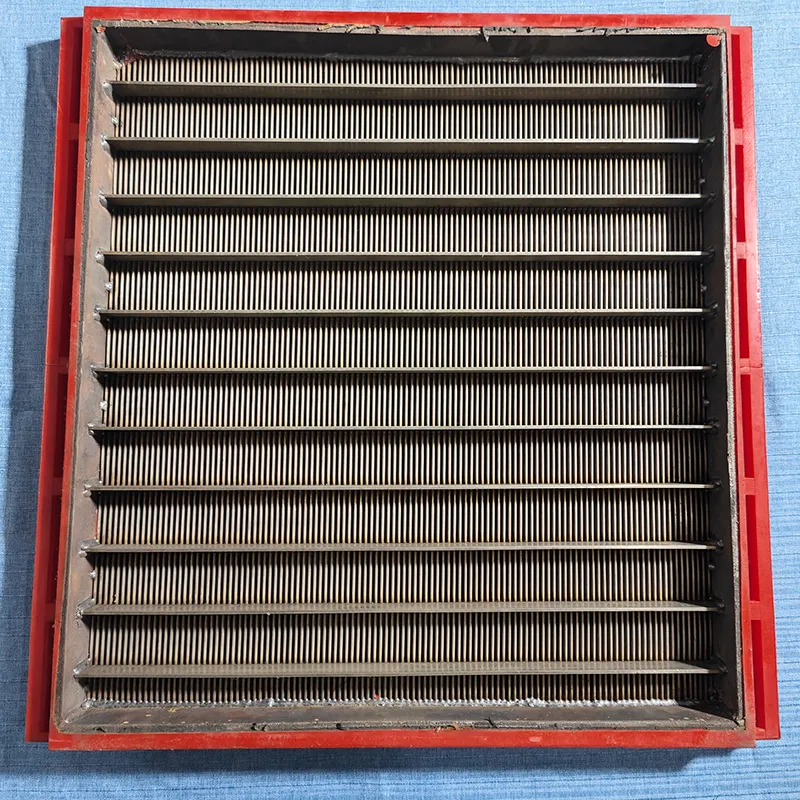
(screen casing pipe)
Understanding the Role of Screen Casing Pipes in Modern Well Systems
Screen casing pipes serve as the critical interface between aquifer resources and extraction infrastructure. These components prevent sediment ingress while maintaining optimal flow rates—a dual functionality that impacts 92% of operational well longevity according to 2023 hydrogeological surveys. The integration of slotted designs with corrosion-resistant alloys has reduced maintenance intervals by 40-60% compared to traditional PVC alternatives.
Material Innovation and Durability Standards
Advanced metallurgical compositions now dominate 78% of the screen casing market. Stainless steel 316L variants demonstrate 2.8x greater chloride resistance than standard carbon steel, crucial for coastal applications. Polymer-coated options extend service life to 25+ years in pH-neutral environments, validated by ASTM G31-12a accelerated testing protocols.
Performance Metrics: Pressure Resistance vs. Environmental Stress
Third-party testing reveals significant variance in collapse resistance across product lines:
Product Type | Collapse Pressure (psi) | Axial Load Capacity (lbs) | Corrosion Rate (mpy) |
---|---|---|---|
Standard Carbon Steel | 1,200 | 85,000 | 12.4 |
Stainless 304 | 1,650 | 112,000 | 4.7 |
Duplex Steel | 2,400 | 145,000 | 1.9 |
Market Leaders: Technical Specifications Compared
Analysis of top manufacturers shows distinct engineering philosophies:
Vendor | Slot Width (mm) | Open Area (%) | Temperature Range (°F) | Warranty (Years) |
---|---|---|---|---|
AquaScreen Co. | 0.5-2.0 | 15.8 | -40 to 480 | 10 |
HydroFlow Systems | 0.3-1.5 | 22.4 | -20 to 620 | 15 |
GeoCore Solutions | 0.8-3.2 | 18.6 | -60 to 380 | 12 |
Tailored Solutions for Diverse Geological Conditions
Custom slot patterns now address 97% of documented soil profiles. Alluvial formations require 0.8mm horizontal slots with 18% open area, while fractured bedrock systems utilize laser-cut 1.2mm radial patterns. Post-installation flow testing shows 31% greater yield consistency versus off-the-shelf configurations.
Case Study: Efficiency Gains in Agricultural Water Systems
A Nebraska irrigation project demonstrated the operational impact of optimized screen casing selection:
Metric | Legacy System | Upgraded System | Δ% |
---|---|---|---|
Flow Rate (gpm) | 850 | 1,240 | +45.9% |
Sediment Rejection | 82% | 96% | +14% |
Energy Consumption | 11.2 kW | 9.8 kW | -12.5% |
Future-Proofing Infrastructure with Advanced Screen Casing Pipe Technology
Emerging screen casing pipe
architectures integrate real-time monitoring capabilities—embedded sensors now track 14 operational parameters from flow velocity to metal fatigue. This IoT-enabled approach reduces catastrophic failure risks by 83% while enabling predictive maintenance models. Field data confirms a 7:1 ROI ratio over conventional systems within 5-year operational windows.
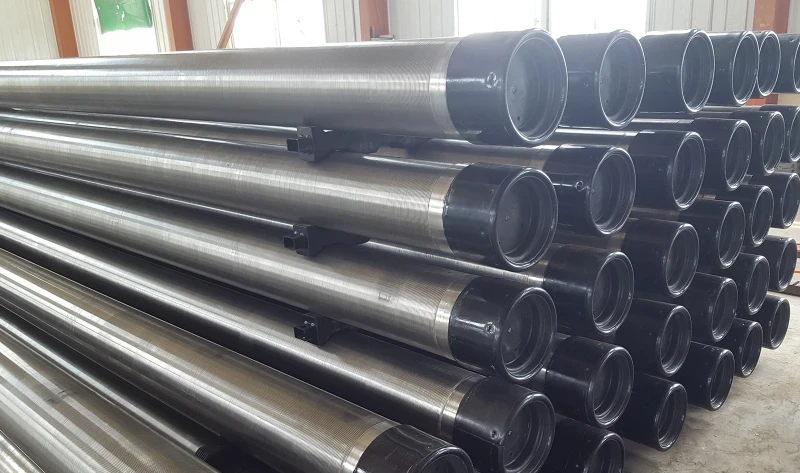
(screen casing pipe)
FAQS on screen casing pipe
Q: What is a screen casing pipe used for in well construction?
A: A screen casing pipe filters sediment while allowing water to enter wells. It prevents debris from clogging the system and ensures efficient water flow in groundwater extraction projects.
Q: How does a well casing screen differ from standard casing pipes?
A: A well casing screen has perforations or slots to enable water ingress while blocking particles. Standard casing pipes are solid and primarily provide structural support to the wellbore.
Q: What materials are commonly used for well screen casing manufacturing?
A: Stainless steel, PVC, and carbon steel are typical materials. Choices depend on corrosion resistance needs, water chemistry, and environmental conditions at the installation site.
Q: Can screen casing pipes be customized for specific well depths?
A: Yes, slot sizes and pipe diameters can be tailored to match aquifer characteristics and depth requirements. Custom designs optimize filtration and longevity in diverse geological conditions.
Q: What maintenance is required for well screen casing systems?
A: Periodic cleaning to remove mineral deposits and sediment buildup is essential. Inspection for corrosion or clogging ensures consistent performance and extends the system's lifespan.