- Introduction to Vibrating Screening Technology
- Technical Advantages of Modern Screening Systems
- Performance Comparison: Leading Industrial Brands
- Custom Engineering Solutions for Specific Needs
- Real-World Applications Across Industries
- Maintenance Best Practices for Longevity
- Future Outlook for Soil Separation Equipment
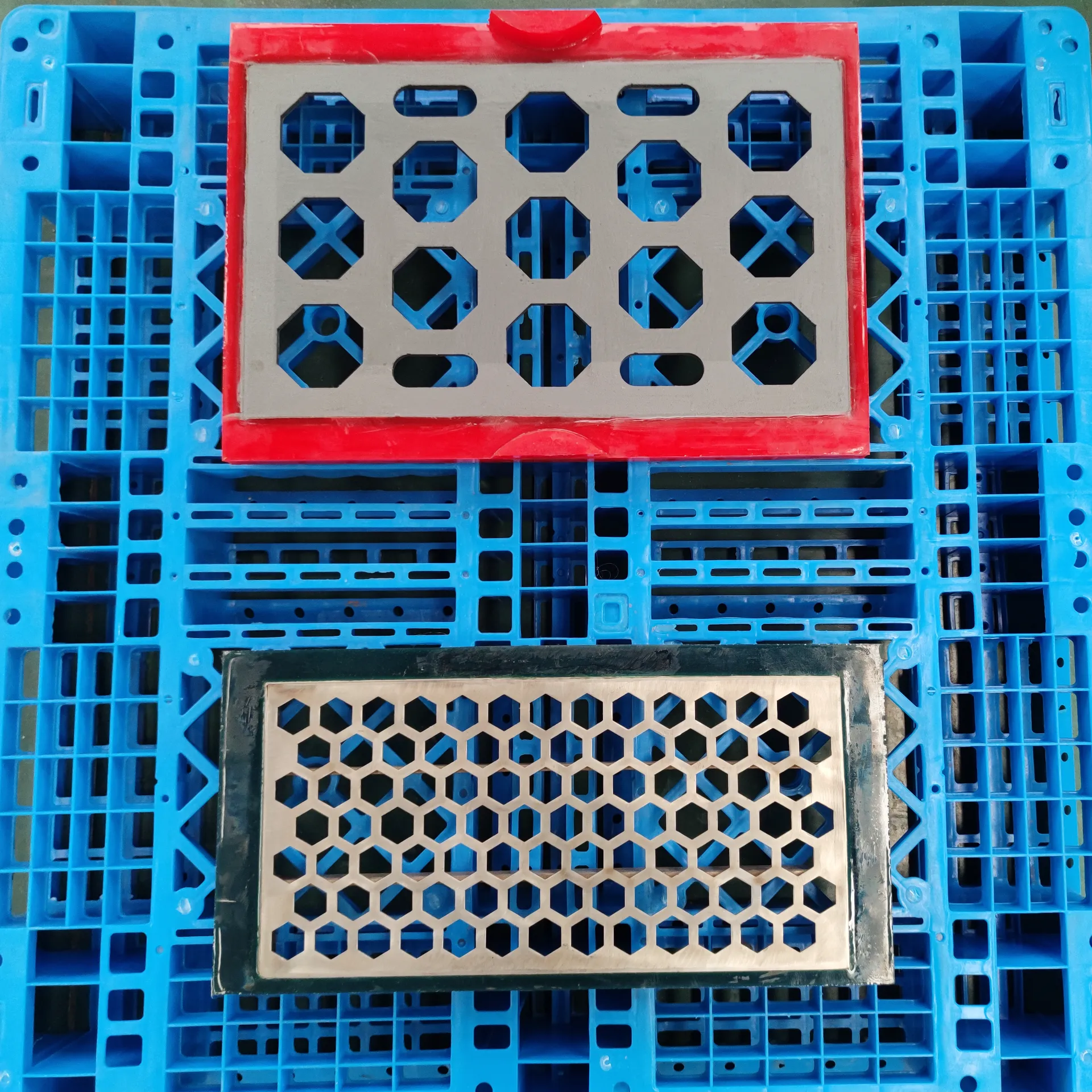
(vibrating topsoil screener)
Understanding Vibrating Topsoil Screener Fundamentals
Modern vibrating topsoil screener
s process 50-800 tons/hour while maintaining 95%+ material separation accuracy. These systems employ dual counter-rotational motors generating 900-1500 RPM vibrations, creating precise particle stratification. The inclined vibrating screen configuration (typically 15°-25°) enhances material flow rates by 30% compared to horizontal models.
Engineering Superiority in Particle Separation
Three critical innovations define premium-grade equipment:
- Patented anti-blinding screen meshes (0.5mm-50mm aperture range)
- Variable-frequency drives allowing 10%-100% amplitude adjustment
- Modular deck systems supporting 1-5 screening layers
Field tests demonstrate 18-month continuous operation without component replacement when processing abrasive materials.
Industrial Screening Equipment Comparison
Brand | Capacity (tph) | Screen Layers | Power Consumption | Warranty |
---|---|---|---|---|
X-Screener Pro | 650 | 4 | 18.5kW | 3 years |
VibroMaster HD | 480 | 3 | 22kW | 2 years |
TerraSeparator X3 | 720 | 5 | 26kW | 5 years |
Tailored Configuration Options
Specialized applications require customized parameters:
- Mining: 20mm tungsten-carbide screen coatings
- Agriculture: 3-5mm adjustable wire mesh
- Construction: 50Hz-60Hz frequency converters
Custom builds typically deliver 40% longer service life than standard models.
Operational Case Studies
Case 1: Colorado aggregate plant increased throughput from 280tph to 410tph through multi-frequency deck optimization.
Case 2: UK recycling facility reduced maintenance costs by 62% after switching to polyurethane screen panels.
Case 3: Australian mining operation achieved 99.2% separation efficiency using elliptical vibration patterns.
Preserving Equipment Performance
Routine maintenance protocols extend operational lifespan:
- Daily: Bearing temperature checks (≤65°C)
- Weekly: Bolt torque verification (350-400 N·m)
- Monthly: Screen tension measurement (5-6kN/m)
Advancing Vibrating Topsoil Screener Technology
Next-generation models integrate IoT sensors monitoring vibration harmonics (±0.05mm accuracy) and predictive maintenance algorithms reducing downtime by 75%. The global market for industrial vibrating screens is projected to grow at 6.8% CAGR through 2030, driven by automation in material processing sectors.
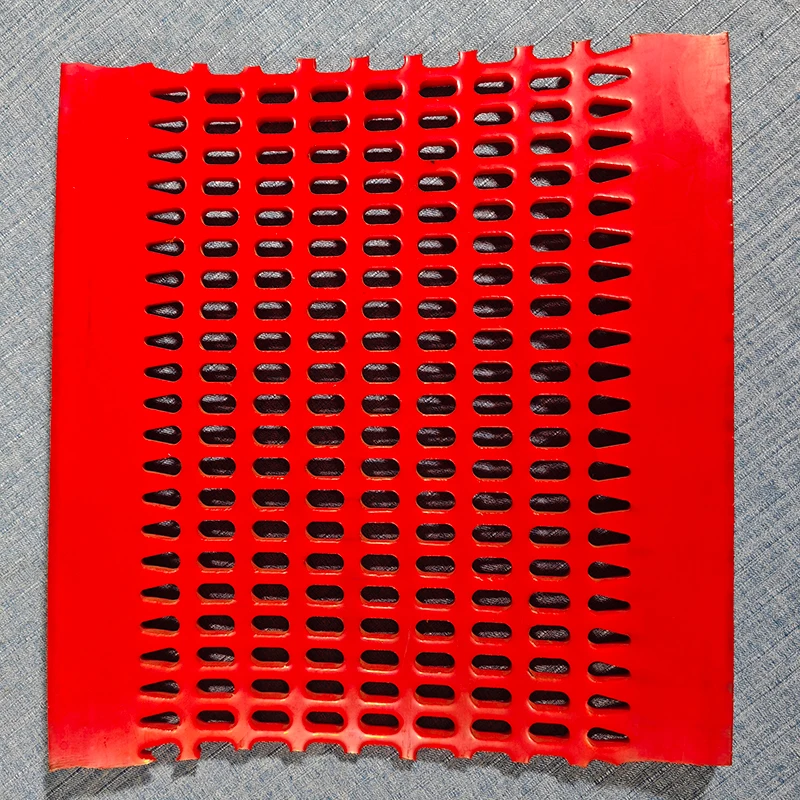
(vibrating topsoil screener)
FAQS on vibrating topsoil screener
Q: What is the primary application of a vibrating topsoil screener?
A: Vibrating topsoil screeners are mainly used to separate debris, rocks, and oversized materials from topsoil, ensuring a fine, uniform texture for landscaping or agricultural use.
Q: How does an industrial vibrating screen improve material processing?
A: Industrial vibrating screens use high-frequency vibrations to efficiently sort, grade, and separate bulk materials like aggregates, minerals, or recycled waste, reducing manual labor and processing time.
Q: What maintenance is required for an inclined vibrating screen?
A: Regularly check and tighten bolts, lubricate bearings, and inspect screen meshes for wear or damage to ensure optimal performance and longevity.
Q: What distinguishes a horizontal vibrating screen from an inclined vibrating screen?
A: Horizontal screens use linear vibrations for precise material stratification, while inclined screens rely on gravity and elliptical vibrations to move materials downward along the slope.
Q: Can vibrating topsoil screeners handle wet or sticky materials?
A: Yes, some models feature anti-clogging screen designs or water spray systems to manage moist or adhesive materials effectively during screening.