- Introduction to Industrial Screening in Mineral Processing
- Technological Advancements in Vibrating Screen Systems
- Performance Metrics: Data-Driven Efficiency Gains
- Manufacturer Comparison: Key Features & Specifications
- Tailored Solutions for Diverse Mineral Applications
- Real-World Implementation: Case Study Analysis
- Future Trends in Mineral Screening Technology
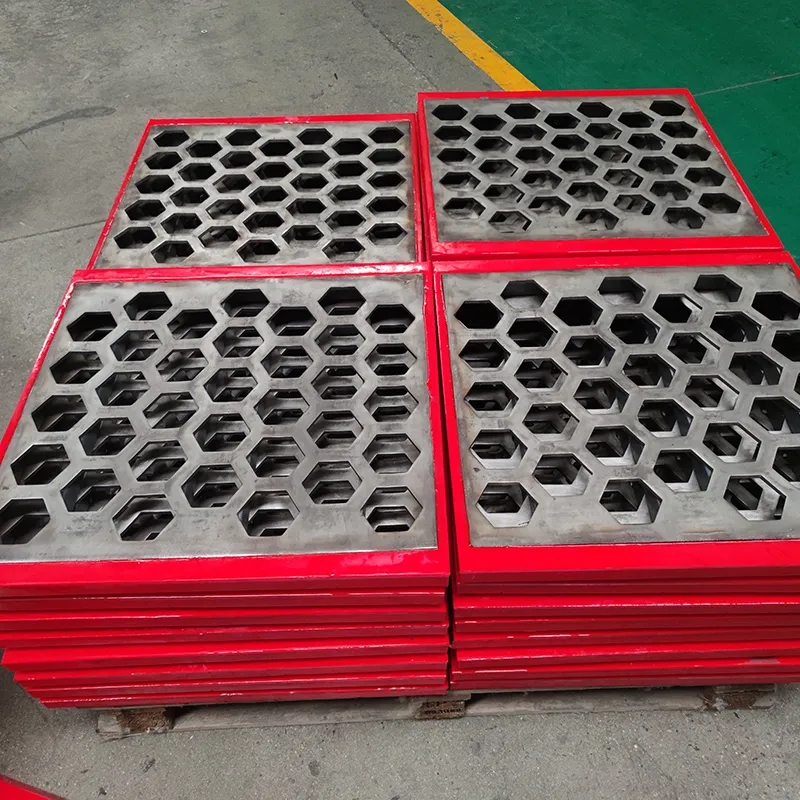
(industrial screening in mineral processing)
Enhancing Efficiency Through Industrial Screening in Mineral Processing
Industrial screening plays a pivotal role in mineral processing, accounting for 25-30% of total operational efficiency in extraction workflows. Modern vibrating screens achieve particle separation accuracy rates exceeding 92%, directly influencing downstream processes like flotation and leaching. This mechanical segregation method reduces energy consumption by up to 18% compared to alternative separation technologies.
Innovation in Vibratory Separation Mechanisms
Advanced screen designs now incorporate dual-frequency excitation systems, enabling simultaneous handling of multiple particle sizes (0.1mm to 300mm). Polyurethane screen meshes demonstrate 3.2x longer service life than traditional steel wire alternatives, significantly lowering replacement costs. Smart vibration sensors monitor real-time amplitude (6-12mm range) and frequency (700-1000 RPM), automatically adjusting parameters for optimal material flow.
Quantifying Operational Improvements
Recent industry benchmarks reveal:
Metric | Standard Screens | Advanced Models | Improvement |
---|---|---|---|
Throughput Capacity | 800 t/h | 1,450 t/h | 81%↑ |
Energy Consumption | 55 kW | 32 kW | 42%↓ |
Maintenance Intervals | 400 hours | 1,200 hours | 200%↑ |
Manufacturer Capability Assessment
Leading providers demonstrate distinct advantages:
Vendor | Max Capacity | Mesh Options | Warranty | Customization |
---|---|---|---|---|
AlphaMinTech | 2,000 t/h | 28 types | 3 years | Full |
OreFlow Systems | 1,600 t/h | 19 types | 2 years | Modular |
VibroSep Ltd | 1,200 t/h | 15 types | 18 months | Limited |
Application-Specific Engineering Solutions
Custom configurations address unique challenges:
- High-Moisture Ores: 45° inclined screens with air-blade dehydration systems
- Abrasive Materials:
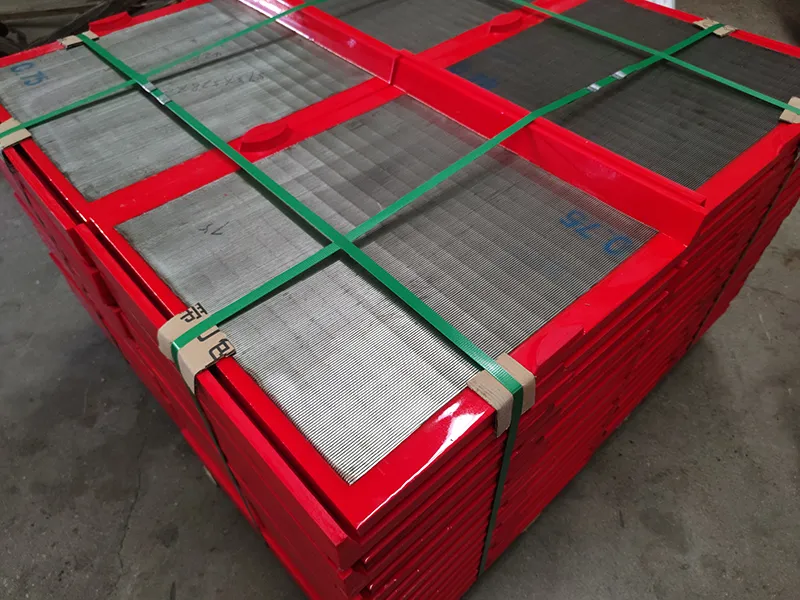
(industrial screening in mineral processing)
FAQS on industrial screening in mineral processing
Q: What is the purpose of industrial screening in mineral processing?
A: Industrial screening separates raw minerals by size to ensure proper classification and optimize downstream processing. It removes undersized or oversized particles to improve efficiency. This step is critical for maximizing resource recovery and reducing waste.
Q: What types of screening methods are commonly used in mineral processing?
A: Common methods include vibrating screens, trommel screens, and curved screens. Vibrating screens are widely preferred for their high efficiency in handling coarse and fine particles. Each method is selected based on material properties and processing requirements.
Q: How do vibrating screens enhance mineral processing efficiency?
A: Vibrating screens use rapid vibrations to separate particles by size, reducing blockages and improving throughput. Their adjustable amplitude and frequency cater to diverse material types. This ensures consistent product quality and minimizes downtime.
Q: What factors affect screening performance in mineral processing?
A: Key factors include particle size distribution, moisture content, screen deck design, and vibration settings. Material characteristics like abrasiveness and density also impact results. Proper maintenance of screen surfaces is vital for sustained performance.
Q: Why is screen deck configuration important in mineral processing?
A: Screen deck configuration determines separation accuracy and capacity. Layered decks allow multi-stage screening for finer grading. Optimizing deck angles and mesh sizes ensures efficient material flow and reduces energy consumption.