- Fundamentals of Screening in Mineral Processing Operations
- Technical Specifications of Modern Screening Equipment
- Performance Comparison: Leading Industrial Screening Systems
- Custom Engineering Solutions for Complex Ore Profiles
- Operational Case Studies in Base Metal Concentration
- Emerging Technologies in Particle Separation
- Strategic Implementation of Screening in Mineral Processing Circuits
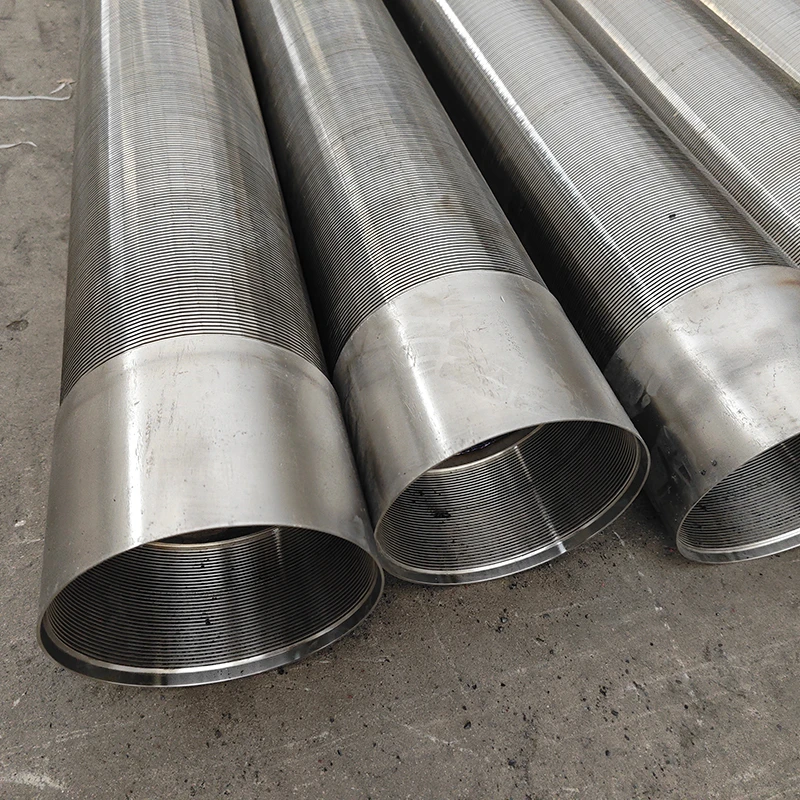
(screening in mineral processing)
Essential Principles of Screening in Mineral Processing
Industrial screening forms the backbone of mineral beneficiation, with vibrating screens processing 12-15 million metric tons annually in medium-sized copper operations. Modern systems achieve 92-97% separation accuracy across particle sizes from 300mm coarse ore to 45μm fines. The operational lifespan of premium screening decks now exceeds 14,000 hours in abrasive iron ore applications.
Advanced Screening Technology Specifications
High-capacity linear vibrators deliver G-forces up to 5.2g, enabling throughput rates of 4,500t/h in diamond processing plants. Multi-deck configurations achieve 4-stage separation within a single footprint, reducing plant space requirements by 18-22%. Smart screening systems incorporate real-time moisture compensation (±3% accuracy) and wear monitoring sensors.
Manufacturer | Capacity (t/h) | Energy Use (kW) | Maintenance Interval | Wear Life (hours) |
---|---|---|---|---|
Metso Outotec | 3,200 | 55 | 480 | 12,000 |
Sandvik | 2,800 | 62 | 420 | 10,500 |
Haver & Boecker | 3,500 | 58 | 500 | 13,200 |
Customized Screening Solutions
Modular screen designs accommodate specific ore characteristics - from 82° inclined units for sticky gold ores to banana screens achieving 35% greater capacity in phosphate operations. Ceramic-coated polyurethane decks demonstrate 63% longer service life in high-silica environments compared to standard rubber surfaces.
Field Performance Analysis
A Chilean copper mine achieved 23% energy reduction through optimized screen media combinations, processing 18Mtpa at 94% efficiency. In Australian iron ore operations, hybrid screening circuits increased yield by 7.4% while reducing screen panel replacement frequency from 6 to 9 months.
Innovations in Separation Technology
High-frequency screens now achieve 500μm separations at 92% efficiency, while AI-powered predictive maintenance systems reduce downtime by 31%. Electromagnetic drive systems cut energy consumption by 18-25% compared to conventional eccentric vibrators.
Optimizing Screening in Mineral Processing Systems
Proper screening configuration improves overall plant efficiency by 12-15%, with advanced control systems maintaining optimal performance across varying feed conditions. Recent installations demonstrate ROI periods under 14 months through increased throughput and reduced media costs.
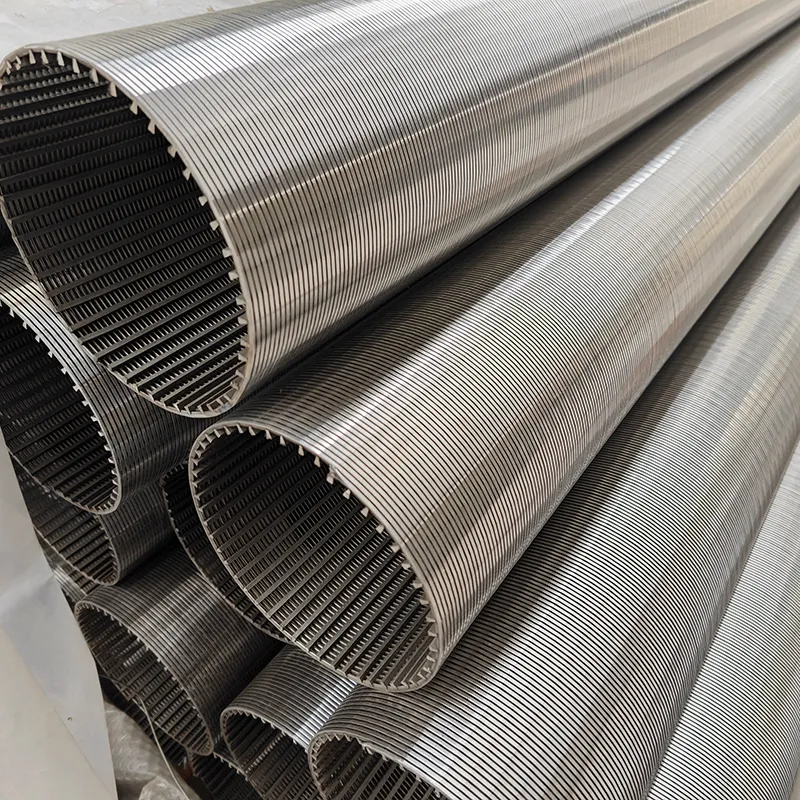
(screening in mineral processing)
FAQS on screening in mineral processing
Q: What is the purpose of screening in mineral processing?
A: Screening separates raw minerals by particle size to ensure optimal downstream processing. It improves efficiency in crushing and grinding stages while minimizing energy waste. Proper screening enhances product quality and resource utilization.
Q: How does industrial screening in mineral processing differ from basic screening?
A: Industrial screening handles large-scale operations with high-capacity equipment like vibrating screens. It integrates automation for consistent particle separation in complex mineral mixes. This method prioritizes durability and adaptability to harsh mining environments.
Q: Why are vibrating screens widely used in mineral processing?
A: Vibrating screens efficiently separate fine and coarse particles through high-frequency vibrations. Their design reduces material clogging and increases throughput. They are versatile for diverse ore types and moisture conditions.
Q: What factors affect screening efficiency in mineral processing?
A: Key factors include screen mesh size, vibration intensity, material moisture content, and feed rate. Proper maintenance and equipment selection also impact performance. Particle shape and screen inclination further influence separation accuracy.
Q: How is screening integrated into a mineral processing workflow?
A: Screening occurs at multiple stages: pre-crushing to remove oversize material, between grinding phases for size control, and pre-concentration. It ensures only properly sized ore progresses to separation processes like flotation or leaching.