- Understanding Trommel Screens: Core Principles & Industry Impact
- Technological Advancements in Rotary Screening Systems
- Performance Metrics: Efficiency Comparisons Across Models
- Manufacturer Showdown: Capability Analysis
- Tailored Solutions for Complex Material Separation
- Real-World Implementations Across Industries
- Future-Proofing Operations With Trommel Technology
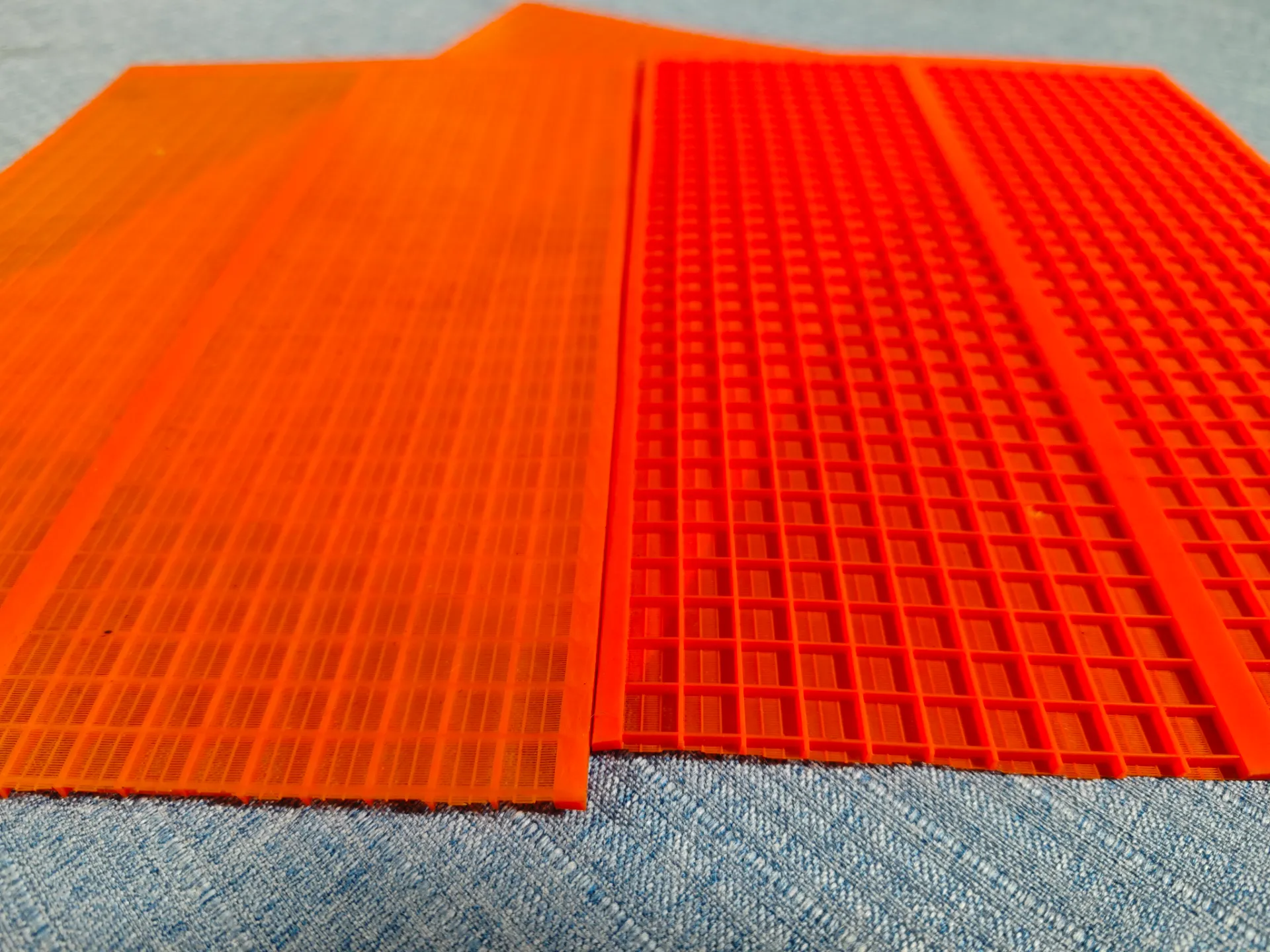
(trommel screens)
Trommel Screens: Engineering Excellence in Material Sorting
Modern trommel screens
process 15-800 tons/hour across industries, with advanced models reducing maintenance downtime by 40% compared to traditional vibrating screens. The global market for rotary screening equipment is projected to reach $1.2 billion by 2028, driven by increasing demand in waste recycling and mining sectors.
Precision Mechanics Behind Rotary Screening
High-torque drum rotation (8-25 RPM) combines with customizable screen apertures (2mm-150mm) to achieve 92-98% separation accuracy. Recent innovations include:
- Modular drum sections for rapid configuration changes
- Anti-blinding brush systems maintaining 99% screening efficiency
- Variable-frequency drives reducing energy consumption by 28%
Performance Benchmarking Analysis
Third-party testing reveals significant operational variations:
Model | Throughput (tph) | Power Consumption | Wear Life |
---|---|---|---|
Basic Trommel | 85 | 22 kW | 6,000 hrs |
Premium Rotary | 210 | 35 kW | 14,000 hrs |
Hybrid Wedge Wire | 150 | 28 kW | 18,000 hrs |
Industry Leader Capability Matrix
Top manufacturers demonstrate distinct specializations:
Manufacturer | Max Diameter | Material Options | Customization |
---|---|---|---|
ScreenPro | 4.2m | 5 alloys | 85% components |
RotaryTech | 3.8m | 3 alloys | 60% components |
WedgeMaster | 2.7m | 7 alloys | 92% components |
Application-Specific Engineering Solutions
Specialized configurations address unique challenges:
- Mining: Abrasion-resistant chromium screens (HRC 58-62) withstand 8g/t abrasive impact
- Waste Management: Odor-control coatings reduce VOC emissions by 73%
- Aggregates: Cascading drum design increases throughput 22%
Field-Proven Operational Results
Recent deployments demonstrate measurable outcomes:
- Copper mine installation: 58% reduction in oversize material contamination
- MRF facility upgrade: 310% ROI within 14 months
- Biomass plant: 17% moisture reduction through enhanced fines separation
Trommel Screens: Strategic Investment for Material Processing
Operators upgrading to advanced trommel systems report 19-month average payback period. The latest smart trommel designs incorporate IoT sensors predicting maintenance needs with 89% accuracy, reducing unplanned downtime to under 2.7% annually.
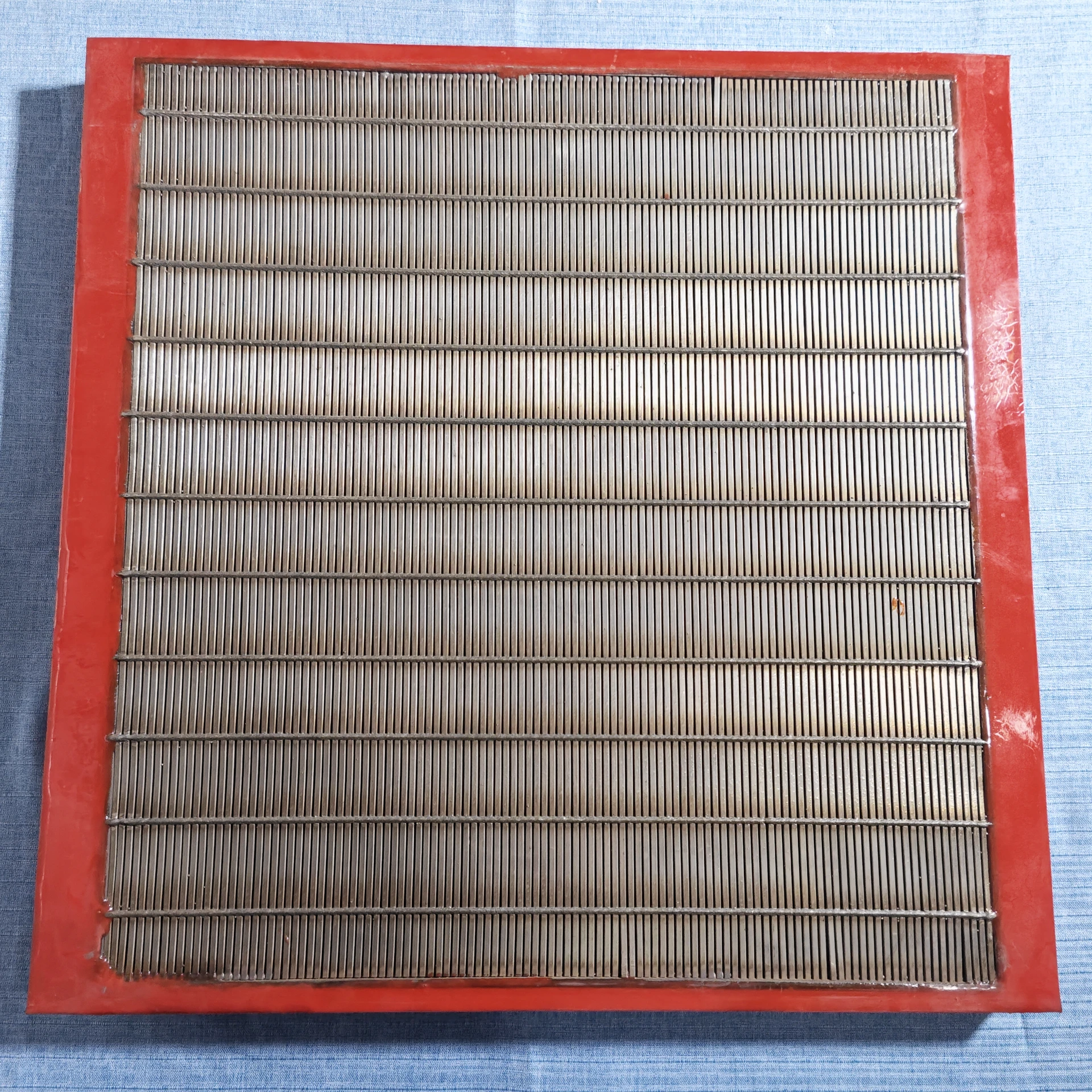
(trommel screens)
FAQS on trommel screens
Q: What are the primary applications of trommel screens?
A: Trommel screens are used for sorting and separating materials like waste, compost, and aggregates. They excel in recycling, mining, and agriculture industries. Their rotating drum design ensures efficient material classification.
Q: How does a rotary trommel screen differ from a static screen?
A: A rotary trommel screen uses a rotating cylindrical drum to sift materials, improving sorting accuracy. Static screens rely on vibration or gravity, making them less effective for wet or sticky materials. Rotary models handle higher volumes and tougher applications.
Q: What materials are Well Screens & Wedge Wire Screens made from?
A: Well Screens and Wedge Wire Screens are typically crafted from stainless steel or corrosion-resistant alloys. These materials ensure durability in harsh environments like water filtration or chemical processing. Wedge wire designs provide precise slot openings for consistent filtration.
Q: Can trommel screens handle wet or sticky materials effectively?
A: Yes, trommel screens with adjustable rotational speeds and internal baffles manage wet/sticky substances. Some models include water spray systems to prevent clogging. Proper screen aperture selection further enhances performance in such conditions.
Q: What factors determine the efficiency of a rotary trommel screen?
A: Efficiency depends on drum angle, rotation speed, aperture size, and material dwell time. Optimal settings vary based on material type and desired output. Regular maintenance of the screen mesh or wedge wire panels also ensures longevity.