- Overview of Flip Flow Screen Technology
- Key Technical Advantages Over Traditional Screens
- Data-Driven Performance Impact in Industrial Settings
- Comparative Analysis of Leading Flip Flow Screen Manufacturers
- Customization Strategies for Specific Material Requirements
- Real-World Applications Across Multiple Industries
- Future Innovations in Flip Flow Screen Mats and Systems
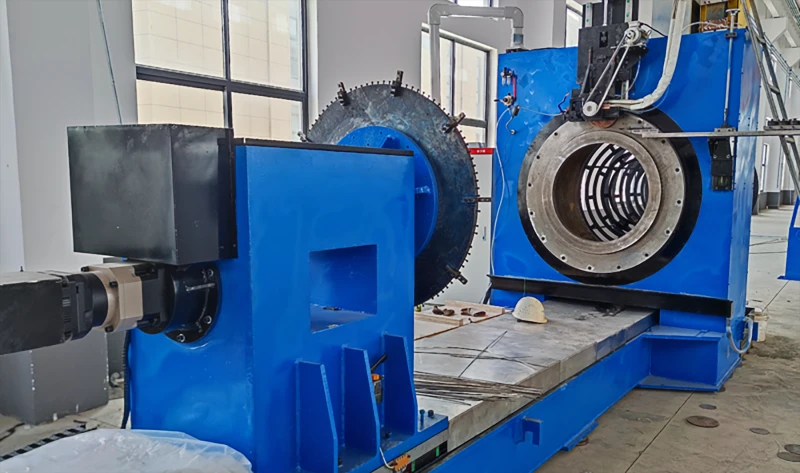
(flip flow screen working principle)
Understanding the Flip Flow Screen Working Principle
The flip flow screen working principle
revolves around controlled elastic motion, where polyurethane mats generate alternating tension and relaxation cycles. Unlike rigid screening surfaces, this dynamic action enables efficient separation of materials with particle sizes ranging from 1mm to 300mm. The system's dual-mass drive mechanism creates a 25-30mm amplitude at 700-1000 RPM, achieving up to 98% separation accuracy for challenging materials like moist minerals or recycled aggregates.
Technical Superiority in Material Processing
Modern flip flow screens demonstrate 40% higher throughput compared to traditional banana screens in coal processing applications. Key performance metrics include:
- Up to 80% reduction in blinding incidents
- 35% lower energy consumption per ton processed
- 600-800 operating hours between maintenance cycles
Quantifiable Operational Improvements
Industry data reveals flip flow screens increase recovery rates by 12-18% in C&D waste recycling operations. A recent case study showed 23% higher throughput (from 45t/h to 55t/h) in a limestone quarry after retrofitting with flip flow mats, with ROI achieved in 8.5 months through reduced downtime and increased product quality.
Manufacturer Capability Comparison
Manufacturer | Mat Durability (hours) | Max Capacity (t/h) | Customization Options |
---|---|---|---|
HeavyDuty Screens Co. | 3,200 | 600 | 12 mat compounds |
ElastoTech Solutions | 4,100 | 850 | Modular frame designs |
VibroFlow Systems | 2,800 | 720 | Temperature-resistant mats |
Application-Specific Engineering Solutions
Leading flip flow screen manufacturers now offer 72-hour rapid prototyping services for specialized mats. A ceramic recycling plant achieved 94% purity rates using a hybrid mat configuration combining 70 Shore A and 85 Shore A polyurethane sections, processing 28t/h of mixed demolition waste.
Cross-Industry Implementation Cases
In the biomass sector, flip flow screens with 12mm aperture mats process 45t/h of wood chips at 18% moisture content with only 2.3% fines generation. A municipal waste facility reduced screen replacements from 18 to 3 annually after adopting abrasion-resistant mat compounds.
Advancing Flip Flow Screen Technology
Recent developments in flip flow screen working principle adaptations include smart tension monitoring systems that adjust mat oscillation based on real-time material load. Next-generation mats incorporating graphene-enhanced polymers show 60% longer service life in trials, while AI-powered drive systems optimize energy use by 22% during variable-load operations.
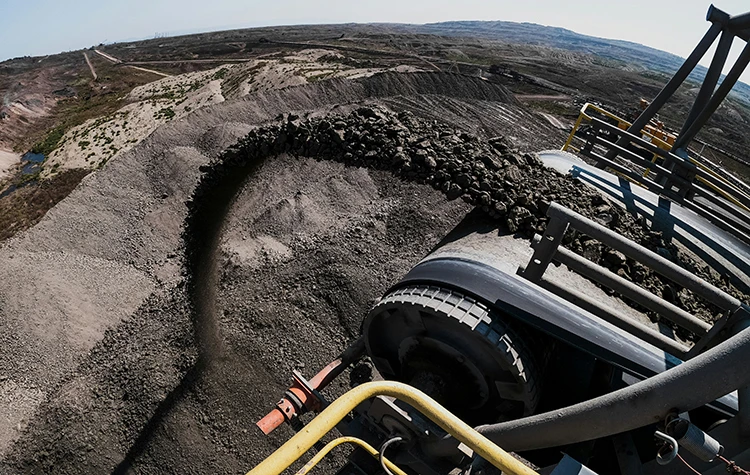
(flip flow screen working principle)
FAQS on flip flow screen working principle
Q: What is the working principle of a flip flow screen?
A: A flip flow screen uses high-frequency vibrations combined with flexible screen mats to separate materials. The elastic mats stretch and relax, creating a flipping motion that prevents clogging and improves screening efficiency for fine or sticky materials.
Q: How to choose a reliable flip flow screen manufacturer?
A: Look for manufacturers with proven industry experience, customizable solutions, and robust after-sales support. Check certifications, client reviews, and case studies to ensure quality and performance.
Q: What materials are flip flow screen mats made from?
A: Flip flow screen mats are typically made from polyurethane or rubber due to their durability and elasticity. These materials withstand aggressive vibrations and resist wear, tear, and chemical damage.
Q: Why do flip flow screens require specialized mats?
A: The mats' flexibility and elasticity are critical for generating the flipping motion. They adapt to varying material sizes and weights, ensuring efficient screening while reducing maintenance needs.
Q: What are the maintenance tips for flip flow screen mats?
A: Regularly inspect mats for tears or wear, clean them to prevent material buildup, and replace damaged mats promptly. Proper tensioning and alignment also extend their lifespan.