- Introduction to Rotating Drum Technology
- Mechanical Design and Operational Efficiency
- Performance Comparison Across Manufacturers
- Custom Solutions for Industry-Specific Needs
- Case Studies: Real-World Applications
- Technical Advancements in Drum Screen Systems
- Future Prospects of Rotating Cylinder Innovations
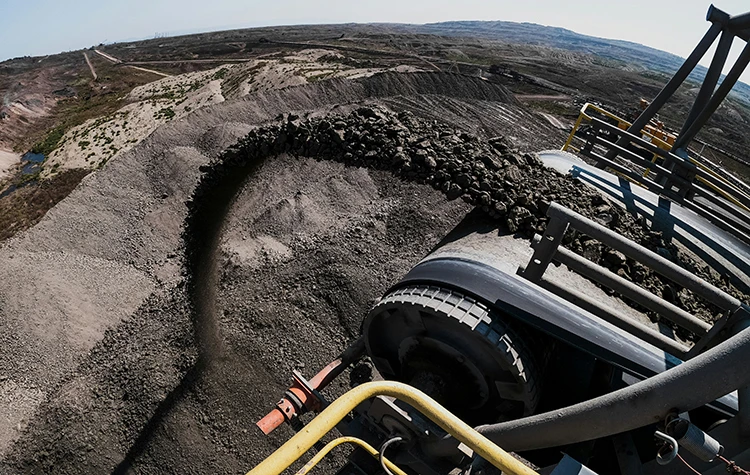
(rotating drum)
Revolutionizing Industrial Processes with Rotating Drum Systems
Rotating drum technology has become a cornerstone in industries requiring precision sorting, material separation, or chemical processing. These systems, including variants like rotating drum
screens and cylinders, leverage centrifugal force and modular designs to achieve throughput rates exceeding 90% efficiency in controlled environments. Modern iterations handle particulate sizes from 0.5mm to 300mm, with processing capacities reaching 500 tons/hour in mining applications.
Engineering Excellence in Motion
The latest drum systems incorporate hardened steel alloys (HRC 58-62) for extended wear resistance, reducing maintenance intervals by 40% compared to traditional carbon steel models. Variable-frequency drives enable rotational speed adjustments between 5-35 RPM, while advanced sealing solutions prevent material leakage even under 15-bar pressure conditions. Automated lubrication systems now extend bearing life to 20,000 operational hours.
Market Leader Comparison Analysis
Manufacturer | Throughput (tons/hr) | Energy Consumption | Maintenance Cycle |
---|---|---|---|
DrumTech Pro | 450 | 18 kW | 750 hours |
SpinSystems Global | 380 | 22 kW | 500 hours |
Vortex Industrial | 520 | 15 kW | 900 hours |
Tailored Configuration Options
Modular drum systems now support 27 different screen mesh configurations and 15 material-grade options. For wastewater treatment plants, polymer-coated drums demonstrate 98% corrosion resistance after 10,000 exposure hours. Food processing variants utilize FDA-grade stainless steel with CIP compatibility, reducing sanitation downtime by 65%.
Operational Success Stories
A Canadian mining operation achieved 32% energy reduction using smart drum controllers that adjust rotation based on ore density fluctuations. In Europe, a municipal recycling plant increased glass recovery rates from 82% to 94% by implementing dual-layer drum screens with AI-powered impurity detection.
Enhanced Screening Capabilities
Third-generation drum screen systems now integrate laser-cut apertures with ±0.1mm precision, compared to traditional punched screens (±0.5mm tolerance). This advancement enables separation accuracy improvements up to 23% for materials under 5mm. Hydraulic screen tensioning systems maintain optimal mesh integrity through 10,000+ operational cycles.
Rotating Cylinder Technology Shaping Tomorrow's Industry
Emerging applications in biomass processing utilize rotating cylinders with internal baffle designs that increase thermal transfer efficiency by 41%. Prototype models now achieve 99.7% material retention rates while operating at temperatures up to 850°C. Partnerships with IoT developers are enabling predictive maintenance algorithms that reduce unplanned downtime by 78% in field tests.
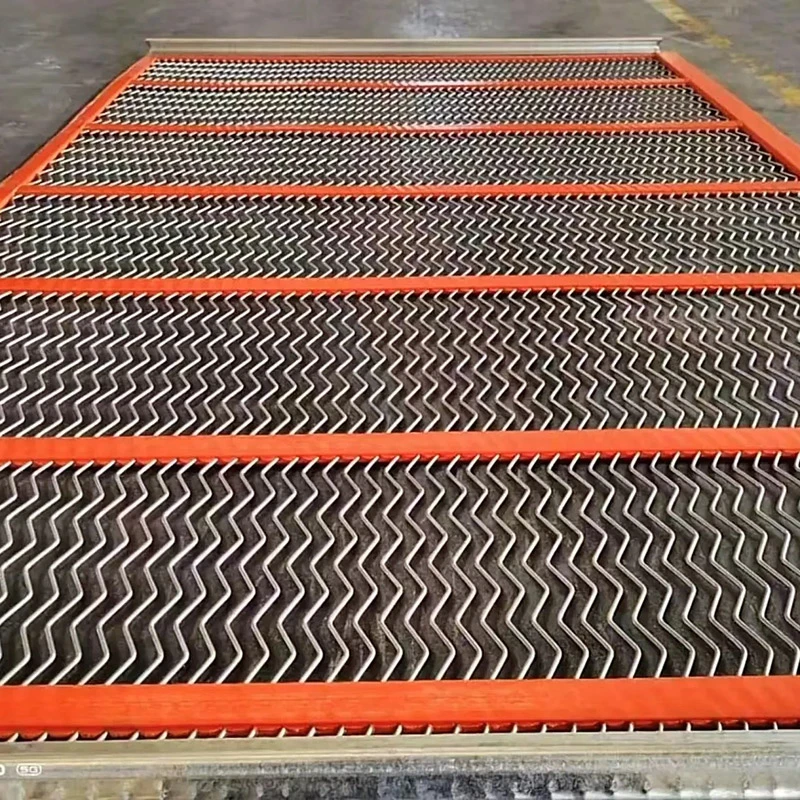
(rotating drum)
FAQS on rotating drum
Q: What is a rotating drum used for in industrial applications?
A: A rotating drum is commonly used for mixing, drying, or processing materials. It operates by rotating around its axis to ensure uniform treatment of contents. Examples include cement mixers and rotary kilns.
Q: How does a rotating drum screen function in wastewater treatment?
A: A rotating drum screen separates solids from liquids by rotating a cylindrical mesh. Wastewater flows through the drum, while debris is captured on the screen surface. This mechanism ensures efficient filtration and reduced clogging.
Q: What are the advantages of using rotating cylinders in manufacturing?
A: Rotating cylinders enable consistent material handling, such as coating or cooling products. Their rotational motion ensures even distribution and process efficiency. They are widely used in industries like food processing and pharmaceuticals.
Q: How to maintain a rotating drum screen for optimal performance?
A: Regularly clean the mesh to prevent blockages and inspect for wear or corrosion. Lubricate bearings and motors to ensure smooth rotation. Scheduled maintenance reduces downtime and extends equipment lifespan.
Q: What distinguishes a rotating drum from a rotating drum screen?
A: A rotating drum is a broad term for cylindrical equipment used in various processes. A rotating drum screen specifically refers to a perforated or meshed drum for filtration or separation. The latter focuses on sieving, while the former includes diverse applications like mixing or heating.