High-Performance Sand Control Screen for Oil & Gas Wells – Durable & Efficient Solutions
- Introduction to sand control screen
technology and its significance - Current challenges of sand control in oil and gas wells
- Analyzing advanced sand control screen technologies and their advantages
- Comparative analysis: Leading manufacturers & product specifications
- The value of customization in sand control screens for specific well conditions
- Real-world application case studies with proven outcomes
- Future trends in sand control screen innovation and industry impact
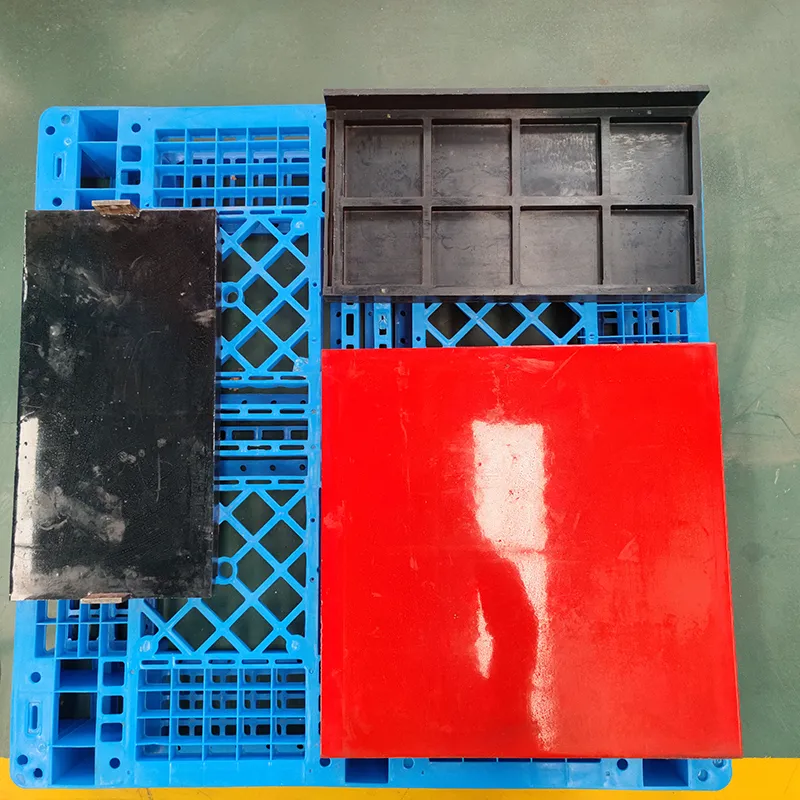
(sand control screen)
Understanding Sand Control Screen Technology
Efficient hydrocarbon production in oil and gas wells critically depends on managing formation sand. Sand control screens have become integral solutions, preventing sand influx that can erode equipment, reduce production rates, and cause costly downtime. The latest market forecasts reveal that sand management failures attribute to more than €2 billion in annual production losses for the global upstream sector. In regions like the Middle East, well studies indicate that over 70% of unconsolidated reservoirs require sand control solutions by default. This prevalence underscores the urgency for reliable sand control in oil and gas wells to safeguard both reservoir integrity and operational efficiency.
Key Challenges in Oil and Gas Well Sand Management
Across varying geological formations, sand influx poses multiple technical hurdles. Deviated wellbores, high-permeability reservoirs, and fluctuating pressure zones increase the risk of sanding. Industry data show that up to 40% of oil wells globally experience unwanted sand production, which can result in more than a 60% decrease in flow rates within the first operational year if left unaddressed. Operators also face issues such as difficulty in predicting sanding intervals, growing regulatory constraints around produced sand disposal, and the escalation of interventions as wells mature. These obstacles amplify the necessity for precisely engineered screening systems that balance high throughput with selective particle retention.
Technological Advancements and Competitive Advantages
Recent breakthroughs in sand control screen design have substantially improved operational outcomes. Wire-wrapped, premium mesh, and multilayer sintered screens now boast filtration ratings as fine as 100 microns, while maintaining open flow areas exceeding 30%. These innovations translate to up to 27% longer operational lifespan and a 15-20% increase in oil recovery rates.
Cutting-edge technologies, such as expandable sand screens, enable conformable deployment in complex well geometries, optimizing contact with the reservoir and minimizing gas or water breakthrough. Improved surface metallurgy and anti-clogging treatments have also rendered screens better equipped to resist erosive forces and biological fouling. The integration of downhole sensors provides real-time feedback, empowering operators to fine-tune production parameters and proactively mitigate sanding events. These technical advances not only boost well reliability but also significantly reduce downtime and maintenance costs, supporting higher overall well productivity.
Manufacturer Comparison: Features and Specifications
Selecting the right sand control screen hinges on understanding manufacturer strengths and the specific performance metrics required for each project. The table below compares leading global vendors and core technology offerings based on publicly available data:
Manufacturer | Screen Type | Filtration Range (microns) | Open Flow Area (%) | Corrosion Resistance Rating | Maximum Operating Pressure (psi) | Fielded Wells (2021-2023) |
---|---|---|---|---|---|---|
Schlumberger | Wire-wrapped/Expandable | 100 - 400 | 30 - 40 | ISO 15156 compliant | 8,500 | 4,700 |
Baker Hughes | Sintered Mesh/Hybrid | 90 - 250 | 25 - 38 | NACE MR0175 | 10,000 | 2,900 |
Halliburton | Premium Mesh/Expandable | 110 - 300 | 28 - 35 | ISO 15156 | 9,000 | 3,800 |
Weatherford | Wire-wrapped/Pre-packed | 120 - 500 | 22 - 33 | API RP14E | 8,000 | 1,950 |
NOV | All-metal Screen | 150 - 400 | 27 - 36 | NACE MR0175 | 9,200 | 1,750 |
Each supplier brings unique value propositions to the table, ranging from ultra-fine mesh counts and corrosion-resistant alloys to rapid delivery and in-situ expandability. Operators should weigh both quantitative specifications and field support capabilities when making procurement and deployment decisions.
The Power of Customization in Sand Control Solutions
No two wells are identical; thus, a tailored sand control strategy is paramount. Custom sand control screens are engineered by optimizing screen type, micron rating, length, and alloy composition based on formation grain size analysis, expected drawdown, and fluid properties. For example, operators in high CO2 content fields often specify duplex or super duplex stainless steel to combat rapid corrosion, while ultra-fine formations benefit from multilayer sintered screens offering tighter particle retention profiles. Proactive collaboration between operators and screen manufacturers accelerates the engineering assessment, testing, and commissioning cycle, ensuring a tight fit to overall field development objectives.
According to a 2023 survey of offshore projects in the Norwegian North Sea, wells utilizing bespoke sand control screens cut sand-related remediation events by 45% compared to those employing generic solutions. This underscores that precise customization directly translates to tangible economic and operational benefits, as well as enhanced environmental compliance.
Field-Driven Case Studies Proving Sand Control Screen Effectiveness
Practical deployment experiences shed light on the transformational impact of modern sand control screens. In the offshore Campos Basin, a major operator retrofitted wells with premium mesh, achieving a 38% improvement in well uptime and extending average run times between interventions by 28 months. In the Oman South Cluster, adoption of expandable sand screens enabled effective completion in severely deviated wells, leading to a 400 barrels per day incremental oil recovery per well.
Similarly, case data from shale plays in the Permian indicate that integrating intelligent sand screens with downhole monitoring slashed sand cut in produced fluids from 2.7% to below 0.3% over a 12-month production cycle. This reduction substantially minimized surface equipment wear, cutting replacement costs by roughly $1.1 million over five wells. These real-world cases validate that thoughtful selection and deployment of technology-aligned sand control screens can reset expectations for well longevity and profitability.
Prospects and Industry Evolution for Sand Control Screen Technologies
As reservoir complexity grows and the focus on carbon-neutral petroleum extraction intensifies, sand control screens will remain at the forefront of well integrity engineering. Visionary suppliers are actively pursuing innovations such as 3D-printed lattices for ultra-precision slotting, nano-coatings for anti-fouling, and autonomous real-time flow control modules embedded directly into the screen. By 2027, the global sand control market is expected to surpass $5.5 billion, with compound annual growth rates above 8%, propelled by both brownfield optimization and greenfield megaprojects in emerging energy provinces.
Adoption of data-driven diagnostics and closed-loop performance monitoring will further empower proactive preventive action, driving ever-greater return on investment for every deployed sand control system. Ultimately, sectors that prioritize advanced, fit-for-purpose sand control solutions—in both harsh and benign environments—will set new benchmarks for safe, economical, and sustainable hydrocarbon production around the world.
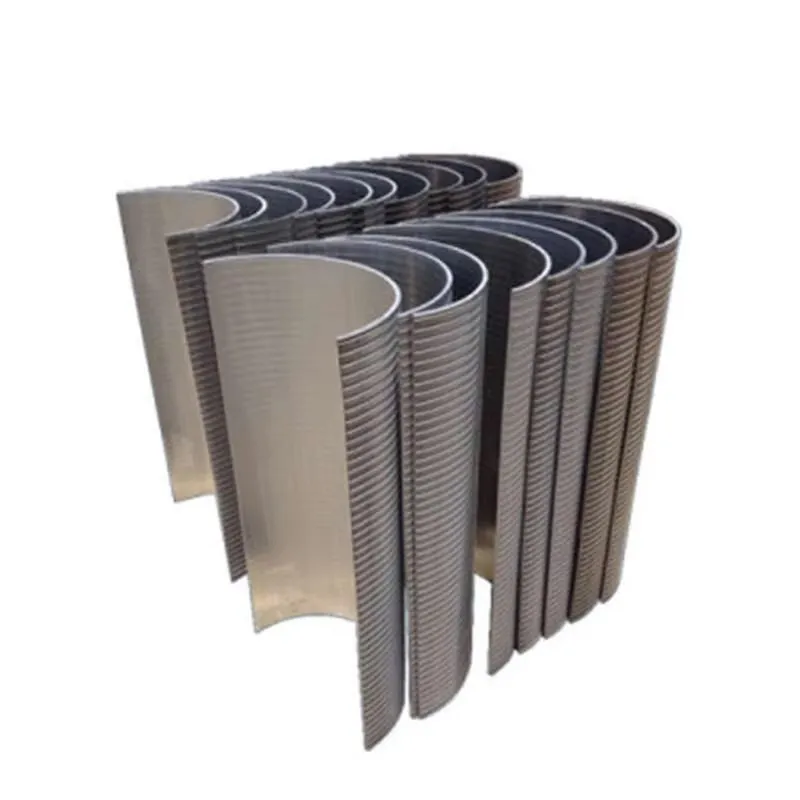
(sand control screen)