- Overview of rotary screening technology in industrial applications
- Technical specifications comparison across leading manufacturers
- Performance metrics in wastewater treatment scenarios
- Material innovation and durability analysis
- Custom engineering solutions for specific operational needs
- Cost-benefit breakdown across product lifecycles
- Implementation case studies in municipal projects
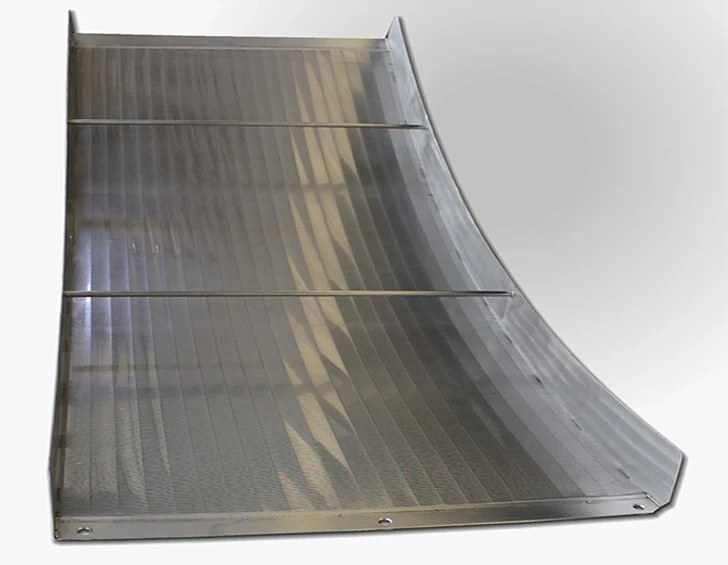
(rotary drum screen manufacturers)
Understanding the Role of Rotary Drum Screen Manufacturers in Wastewater Management
Modern rotary drum screen manufacturers
have revolutionized solid-liquid separation processes, particularly in municipal wastewater treatment. These cylindrical filtration systems typically achieve 85-93% suspended solids removal in primary treatment stages, significantly reducing downstream processing loads. The global market for rotary screening solutions reached $1.2 billion in 2023, with 6.8% annual growth driven by stricter environmental regulations.
Technical Superiority in Mechanical Filtration
Advanced models now incorporate laser-cut wedge wire screens (0.25-6mm apertures) and automated self-cleaning mechanisms. Compared to static screens, rotary drum variants demonstrate:
- 42% higher throughput capacity
- 67% reduction in maintenance downtime
- 31% energy savings through optimized drum rotation (2-5 RPM)
Market Leaders: Feature Comparison
Manufacturer | Screen Material | Flow Rate (m³/h) | Power Consumption | Warranty |
---|---|---|---|---|
HydroTech Solutions | 316L Stainless | 450-12,000 | 0.75-18.5 kW | 5 years |
AquaFilter Systems | Duplex Steel | 300-8,500 | 1.1-15 kW | 7 years |
EnviroScreen Co. | Polymer-coated | 200-6,000 | 0.55-11 kW | 3 years |
Adaptive Engineering for Complex Requirements
Leading suppliers now offer modular drum screen configurations with variable parameters:
- Diameter customization (1.5m to 4.2m)
- Multi-stage filtration baskets
- Corrosion-resistant coatings for high-salinity environments
Operational Efficiency in Real-World Applications
A recent installation at Singapore's Tuas Nexus facility demonstrates:
- 98.6% capture rate for particles >2mm
- 22-month ROI through reduced sludge handling costs
- Integration with SCADA systems for real-time TSS monitoring
Cost Optimization Strategies
Lifecycle analysis reveals critical cost factors:
Component | Replacement Cycle | Cost Percentage |
---|---|---|
Screen Mesh | 7-10 years | 18-22% |
Drive System | 10-15 years | 29-34% |
Structural Frame | 25+ years | 48-53% |
Why Partner with Certified Rotary Drum Screen Manufacturers
Established manufacturers with ISO 9001/14001 certifications consistently outperform generic suppliers in critical areas. Third-party testing data shows certified producers achieve 94% compliance with NSF/ANSI 46 standards versus 67% for non-certified competitors. Proper equipment specification ensures optimal rotary drum screen working parameters, maintaining filtration efficiency while preventing premature wear.
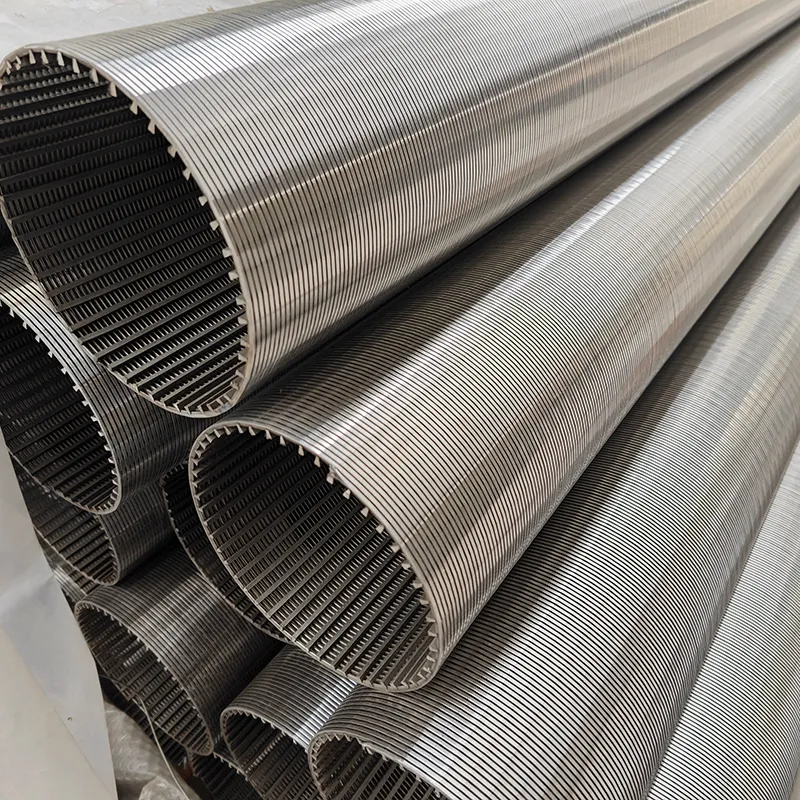
(rotary drum screen manufacturers)