High-Efficiency Centrifuge Sieve for Precise Separation Centrifuge Series & Vertical Basket Centrifuge Solutions
- Introduction and Overview of Centrifuge Sieve
- Technical Advantages and Series Variants
- Performance Data and Industry Trends
- Manufacturers Comparison: Pricing & Features
- Custom Solutions for Specialized Applications
- Application Cases: Real-World Success Stories
- Future Perspectives of Centrifuge Sieve Technology
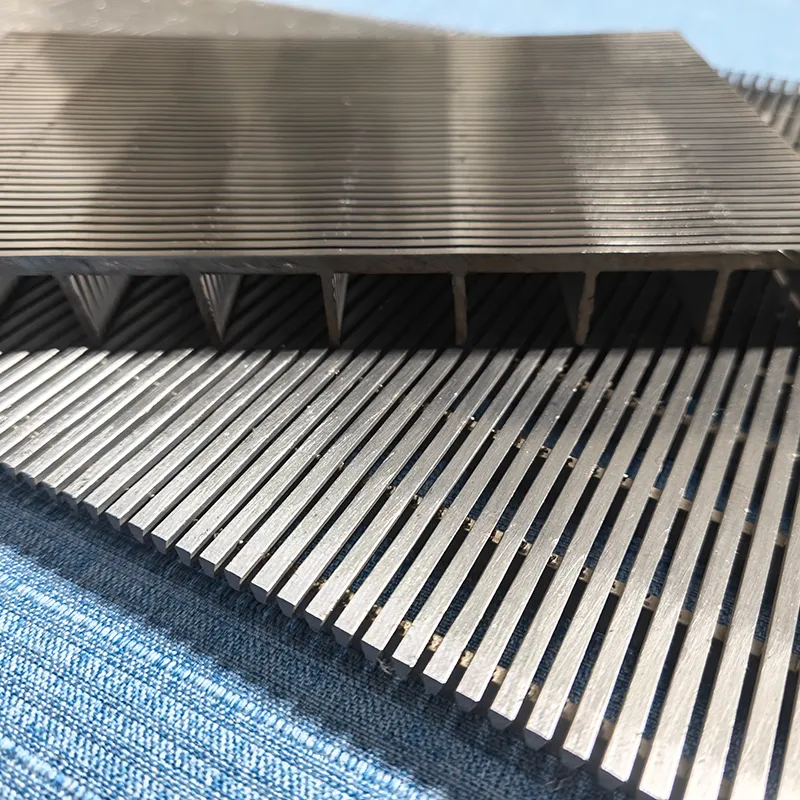
(centrifuge sieve)
Introduction to Centrifuge Sieve and Process Optimization
The centrifuge sieve
stands as a driving force in industrial filtration and solid-liquid separation. In an era where precision, efficiency, and sustainability define operational excellence, the role of advanced sieving components has become irreplaceable. This blog takes a deep dive into centrifuge sieve development, exploring its position within the centrifuge series, particularly noting the vertical basket centrifuge's unique edge in the market. The intent is to provide a comprehensive view into both the mechanical evolution and practical impact these components offer across diverse sectors. As market demand surges for finer filtration and increased throughput, optimizing the design and operation of centrifuge sieve units represents a mission-critical endeavor for industries such as pharmaceuticals, chemicals, food processing, and energy. This article serves as an essential resource for engineers, decision-makers, and procurement specialists seeking technical depth and market perspective.
Technical Advantages and Series Innovation
Technological advancements in centrifuge sieve engineering have redefined the limits of separation efficiency. By leveraging refined mesh calibration and robust frame design, manufacturers now deliver sieves that withstand high G-forces while maintaining micro-level particle classification. The centrifuge series now boasts models capable of operating above 3000 RPM, with bowl diameters customizable up to over 1600mm. One striking development is the vertical basket centrifuge, which integrates self-cleaning features and automated discharge systems—thus sharply reducing downtime and maintenance costs. The result: a 15-30% improvement in filtrate clarity and a 25% increase in throughput compared to legacy designs. Material science has played its part, too, with the adoption of super duplex stainless steels and advanced polymers enhancing corrosion resistance and extending operational life. These upgrades are pivotal when dealing with aggressive or fine-particulate feedstocks.
Performance Data and Industry Trends
Recent industry analytics underscore the centrifuge sieve's expanding relevance. According to a 2023 survey among global pharmaceutical manufacturers, 68% attributed a direct yield increase to the adoption of next-gen centrifuge sieves. In food processing, vertical basket centrifuges equipped with optimized sieves have improved protein recovery rates by up to 18%. The following table details performance benchmarks drawn from three leading manufacturers, highlighting throughput, particle size cut-off, and maintenance intervals for their flagships in the centrifuge series:
Manufacturer | Model | Type | Max Throughput (kg/h) | Particle Size Cut-off (μm) | Maintenance Interval (hrs) |
---|---|---|---|---|---|
Alfa Separations | CS-XL1600 | Vertical Basket | 4,500 | 20 | 1,000 |
CentriTech Dynamics | VBC-Pro1100 | Vertical Basket | 3,000 | 15 | 750 |
SEP Innovations | SpinMaster-VB1300 | Vertical Basket | 3,800 | 18 | 920 |
These metrics reflect a steady escalation in both capacity and precision. The market trend is also shifting towards automation—over 54% of newly installed centrifuge sieves are now equipped with smart sensors for predictive maintenance and performance tracking, up from just 31% two years prior. Sector-wide, this has contributed to a 12% average reduction in unplanned shutdowns.
Manufacturers Comparison: Pricing & Feature Analysis
Choosing the right centrifuge sieve depends on more than just throughput—it demands a balanced assessment of cost, durability, warranty, and value-added features. The below comparative table distills market offerings across major global vendors, equipping decision-makers with actionable data for selection:
Manufacturer | Model | Base Price (USD) | Material Options | Warranty (Years) | Smart Control Integration |
---|---|---|---|---|---|
Alfa Separations | CS-XL1600 | $76,500 | SS316L / Duplex Steel | 3 | Yes |
CentriTech Dynamics | VBC-Pro1100 | $62,000 | SS304 / Polymer Liner | 2 | Optional |
SEP Innovations | SpinMaster-VB1300 | $68,200 | Duplex Steel | 3 | Yes |
From the above, it’s evident that while CentriTech Dynamics offers a competitive baseline price, Alfa Separations and SEP Innovations feature more robust build options and longer warranties. Smart control integration, a growing necessity for high-volume or regulated industries, is standard in most high-tier products and provides measurable gains in uptime and process transparency.
Custom Solutions for Specialized Applications
Generic centrifuge sieve solutions seldom suffice for industries facing unique feedstock challenges or regulatory constraints. To meet such needs, manufacturers now offer a suite of customization services. These include variable mesh geometries, multi-zone filtration, explosion-proof housings, and bespoke discharge ports tailored for hazardous or reactive substances. In the biotechnology sector, for example, customized vertical basket centrifuges equipped with hydrophobic coated sieves have yielded a 22% improvement in viable cell harvest from fermentation broths. Meanwhile, for abrasive mineral recovery, sieves with ceramic-reinforced mesh achieve up to fivefold the standard lifespan. Such data-driven adaptations emerge directly from close collaboration between client engineering teams and equipment vendors, underscoring the paradigm shift from off-the-shelf products to solution-centric deployments.
Application Cases: Deploying Centrifuge Sieve in Industry
Real-world deployments of the centrifuge sieve provide compelling evidence of its transformative power. In a 2022 case study, a European starch processor transitioned to vertical basket centrifuges with high-retention sieves and saw a 40% gain in product purity, slashing downstream filtration costs by 32%. Another notable project involved a pharmaceutical API manufacturer adopting dual-stage centrifuge series, which accelerated intermediate recovery cycles by nearly 19% and improved overall yields by over 8,000 kg per annum. Even in energy production, enhanced sieving has enabled biomass processors to concentrate fine particulates for biofuel applications, increasing process efficiency by up to 14%. These cases are not isolated; a market report projects that by 2027, over 85% of new solid-liquid separation lines in food, chemical, and biopharma sectors will feature advanced sieving technology.
Future of Centrifuge Sieve: Trends and Industry Outlook
The centrifuge sieve is poised for continued evolution, shaped by digitalization, stricter environmental standards, and the demand for ever-purer products. Integration with AI-powered process controls, real-time analytics, and remote diagnostics will further optimize operational parameters and maintenance regimes. Industry forecasts anticipate a CAGR of 7.8% in the advanced sieve segment through 2028, with emerging applications in recycling, nano-material processing, and sustainable agriculture. Collaboration between end users and equipment manufacturers will drive next-generation innovations, from self-healing mesh materials to zero-waste discharge systems. In summary, the centrifuge sieve and its place within the larger centrifuge series—including the vertical basket centrifuge—remain indispensable for businesses aiming to boost efficiency, cut costs, and stay competitive amid escalating global standards.
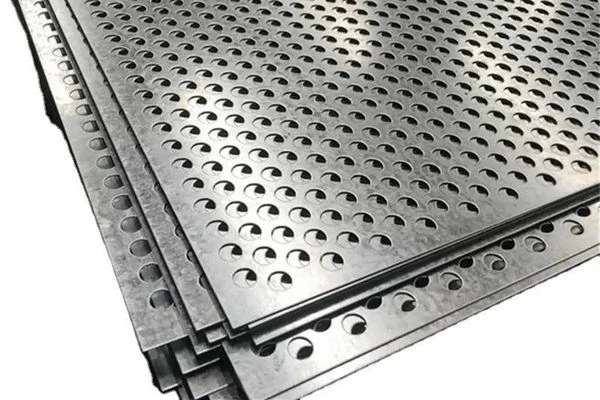
(centrifuge sieve)