- Introduction to industrial vibrating screen
s and their importance - Impactful data on efficiency and technological advancements
- Comparative analysis of key manufacturers
- Custom solutions for diverse industrial needs
- Application case studies across mineral processing and other sectors
- Operational optimization and maintenance strategies
- Conclusion highlighting the future of industrial vibrating screen technologies
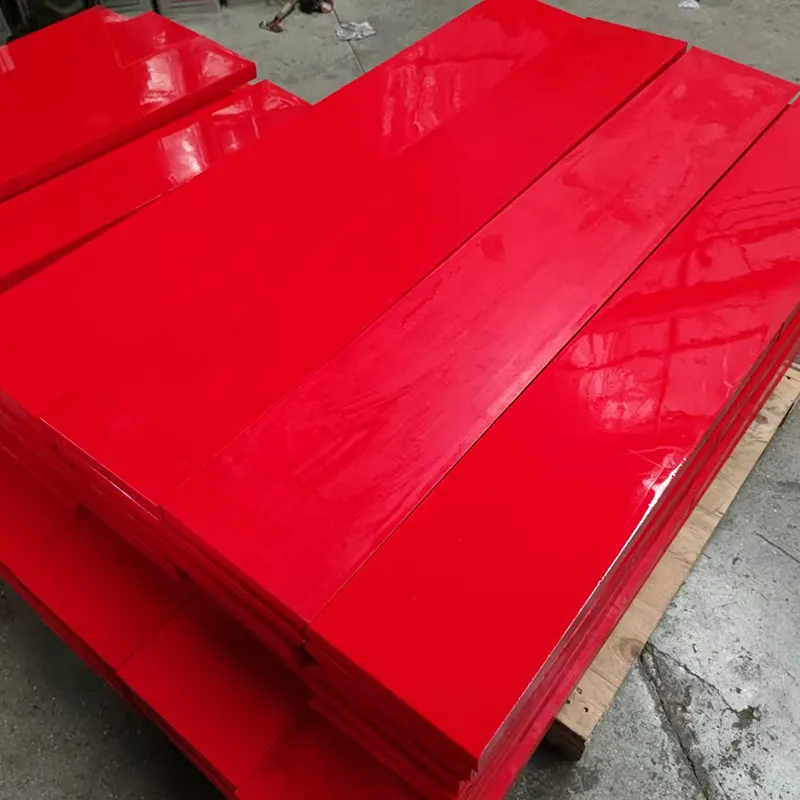
(industrial vibrating screen)
Industrial Vibrating Screen: Essential Equipment in Modern Processing
In modern industries, the need for precise and efficient material separation drives the continuous evolution of equipment. Industrial vibrating screens have become integral for numerous sectors—especially mineral processing—where the requirement for high throughput, accuracy, and minimal downtime is paramount. Efficient screening lies at the heart of ensuring product quality, reducing waste, and optimizing downstream operations. The strategic application of vibrating screens enables organizations to tackle materials ranging from fine particles to large aggregates, maximizing process yield and minimizing operational costs.
Efficiency Data and Technological Advancements
Recent industry analyses demonstrate substantial improvements in both throughput and accuracy due to advancements in industrial screening technologies. Modern vibrating screens boast processing capacities that have increased by over 23% in the last decade, with fines recovery rates now exceeding 98% in optimized installations. These figures are bolstered by new drive technologies, precision-engineered screening media, and digital monitoring systems. Enhanced vibration mechanisms—such as adjustable stroke and frequency—enable tailored solutions, addressing specific ore and feed characteristics.
For example, in mineral processing facilities, implementing state-of-the-art screens can reduce downtime by up to 37%, contributing to an annual cost savings of approximately $380,000 for a mid-sized plant. The following table contrasts previous generation models with next-generation vibrating screens, summarizing recent technological breakthroughs:
Feature | Previous Generation | Next-Gen Industrial Vibrating Screens |
---|---|---|
Throughput (TPH) | 200–400 | 350–650 |
Screening Efficiency (%) | 88–92 | 97–99 |
Fine Particle Recovery (%) | 80–85 | 95–98 |
Downtime (hrs/year) | 110 | 69 |
Maintenance Frequency | Monthly | Quarterly |
Integrated Digital Monitoring | No | Yes |
Benchmarking Major Manufacturers: A Comparative Overview
The global landscape for industrial sieves and screens is populated by several leading manufacturers, each offering unique approaches to durability, customization, and operational support. Consider the comparative table below:
Manufacturer | Main Technology | Certifications | Global Support | Warranty | Innovation Rating |
---|---|---|---|---|---|
Kason Corporation | Circular Vibratory Screeners | ISO 9001 | North America, EU, APAC | 2 years | 4.5/5 |
Schenck Process | Linear Motion Screens | ATEX, ISO 14001 | Global | 3 years | 4.8/5 |
Rotex Global | Gyratory Reciprocating Screens | CE, ISO 9001 | Americas, EMEA, APAC | 2 years | 4.2/5 |
Metso Outotec | Banana Screens | ISO 9001, OHSAS 18001 | Global | 3 years | 4.9/5 |
While all major brands invest in robust engineering, aspects such as localized service, modularity, and digital integration set them apart. End-users frequently rank after-sales service and upgrade paths as determining factors when choosing a supplier.
Custom-Engineered Solutions for Complex Requirements
Industrial screening in mineral processing often presents unique challenges: high moisture content, abrasiveness, irregular particle shapes, or variable feed rates. Leading suppliers now offer fully custom solutions that optimize screen size, vibration patterns, deck configurations, and materials of construction. For instance, polyurethane screen panels have replaced metal mesh in high-wear situations, significantly extending service life. Some installations integrate real-time condition monitoring, automatically flagging torque or amplitude changes that precede costly failures.
Customization is not limited to the physical build. Process-specific enhancements—such as anti-blinding devices, heated decks for damp fines, or quick-release fasteners—ensure screens meet precise workflows. Collaboration between engineers and clients during early design stages allows for simulation-driven selection, reducing commissioning time and minimizing operational risk.
Sector Application Cases: Mineral Processing and Beyond
The utility of industrial sieves and screens extends well beyond mineral processing, finding roles in food production, pharmaceuticals, chemicals, and recycling. Within mining, one South African platinum concentrator reports that upgraded multi-slope banana screens increased annual recovery by 2.6%, translating to additional revenue of $4.2 million. In the food industry, high-frequency fine screens ensure contaminant-free finished goods and comply with strict hygiene audits.
A prominent recycling facility processing electronic waste reduced labor costs by 18% after installing triple-deck vibratory separators—automating the sorting of valuable metallic fractions. As ever more sectors prioritize quality control and throughput, custom-engineered screening systems are fast becoming industry standards, driving up both profitability and regulatory compliance.
Case studies consistently highlight the ROI achievable through higher screening efficiency, lower maintenance, and minimized product contamination—demonstrating a direct link between cutting-edge screen technology and overall business resilience.
Optimizing Performance: System Integration and Maintenance
Achieving sustainable operation from industrial vibrating screens demands more than initial specification. Key performance levers include feed consistency, correct screen tensioning, balanced vibration amplitude, and regular maintenance scheduling. Proactive use of built-in diagnostic sensors has led to a 34% reduction in unplanned downtime, according to a recent survey covering 120 facilities worldwide.
Integration with plant-wide automation frameworks facilitates closed-loop control, adjusting screening parameters in real-time based on material flow or product specifications. Modular components and tool-free maintenance designs reduce mean time to repair (MTTR) from several hours to under 40 minutes, maximizing asset utilization. Training programs focused on predictive maintenance and digital monitoring further ensure staff efficiency and equipment longevity.
The Future of Industrial Vibrating Screen Technology
With accelerating advances in industrial screening, future developments will likely emphasize AI-driven process optimization, wear-resistant sustainable materials, and fully autonomous monitoring systems. The convergence of data analytics, remote troubleshooting, and modular engineering promises to elevate the role of the industrial vibrating screen from a simple separator to an intelligent process enabler. As industries face mounting pressures for higher output, energy efficiency, and regulatory compliance, investment in next-generation vibrating screens will remain a cornerstone of robust, future-proof operations.
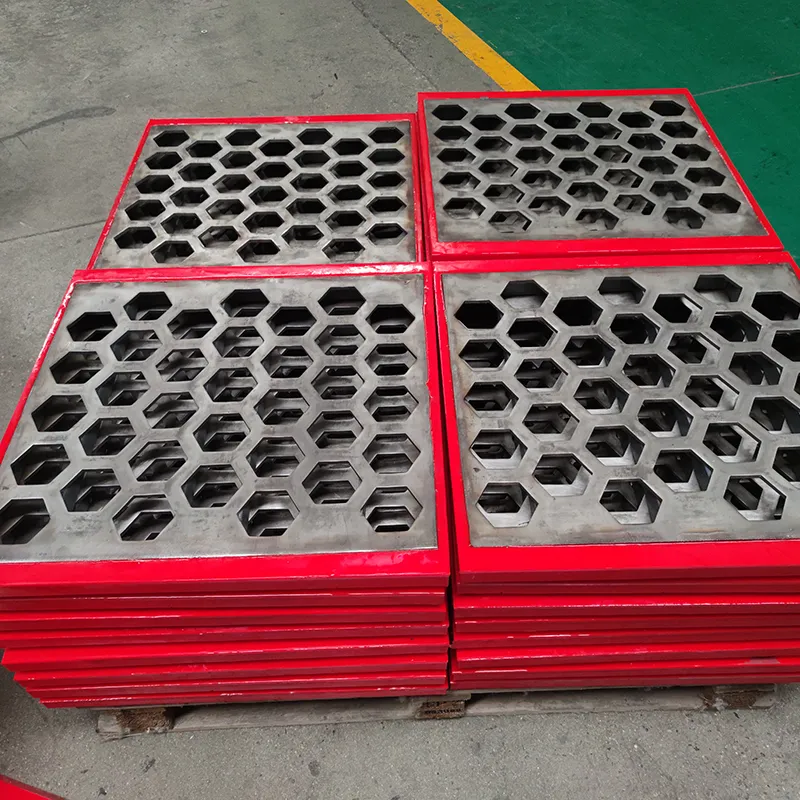
(industrial vibrating screen)