- Introduction to coanda screen manufacturers
and their market importance - Technical superiority of Coanda screens compared to traditional screening technologies
- Comprehensive comparison: coanda screen, mining screen, and rotary drum screen manufacturers
- Customization options and tailored engineering solutions
- Real-world success: case studies from key industries
- Key considerations when selecting a screening solution and manufacturer
- Conclusion: Why select leading coanda screen manufacturers for optimal results
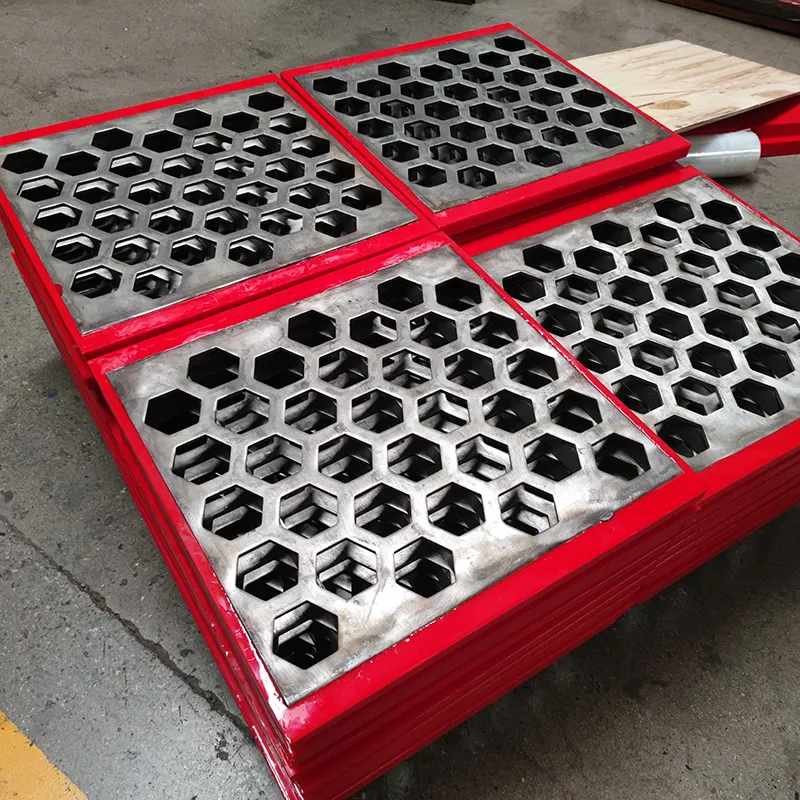
(coanda screen manufacturers)
Introduction: The Pivotal Role of Coanda Screen Manufacturers
In today’s industrial landscape, coanda screen manufacturers serve a crucial function in the global water management, hydropower, and mining sectors. Their expertly engineered screens separate solids and manage water flow with unparalleled precision, directly impacting project efficiency and compliance with ever-stricter environmental standards. As the demand for advanced screening solutions surges—driven by urbanization, stringent regulations, and resource conservation goals—the manufacturers of these products are under increasing pressure to deliver robust, efficient, and long-lasting technologies. The global market for industrial screens was valued at over $3.2 billion in 2023, with Coanda screens accounting for a rapidly expanding segment thanks to their low maintenance requirements and improved debris exclusion rates, reportedly reaching up to 98% efficiency in optimized hydropower applications. This overview sets the stage for a detailed exploration of their technical, comparative, and business advantages.
Technical Edge: Engineering Advantages of Modern Screening Technologies
The engineering landscape of coarse screening has been revolutionized by the implementation of advanced Coanda screen profiles. Unlike conventional flat bar or wire screens, these are built with specialized curved wedge-wire panels set at a precise angle, harnessing the Coanda effect to maximize water capture while rejecting debris. Recent research published in the Journal of Hydraulic Research confirms that Coanda screens can reduce operational downtime by as much as 70% compared to older grate systems.
Key advantages include:
- Self-cleaning action: Gravity-assisted flow helps rinse the surface, reducing clogging and manual intervention.
- Superior hydraulic performance: Optimized open area (typically 60–75%) and smooth wire profiles cut head losses by 20–30%.
- Maximized debris exclusion: Field data shows up to 98% debris exclusion, drastically reducing downstream load.
- Extended service life: High-grade stainless steels (AISI 304/316L) and precise welding extend life expectancy beyond 20 years in most installations.
Comparative Analysis: Leading Manufacturers and Screening Technologies
The selection of a screening solution is highly influenced by manufacturer expertise, material selection, output capacity, and aftersales support. To aid investment decision-making, the following table presents a comparison of top-tier options across three principal technologies:
Manufacturer | Technology | Max. Screen Length (m) | Debris Exclusion Efficiency (%) | Typical Application | Material Grade | Maintenance Cycle (months) | Operational Lifespan (years) |
---|---|---|---|---|---|---|---|
HydroScreen Pro | Coanda Screen | 7 | 98 | Hydropower Intake | SS 316L | 36 | 20+ |
MineFlow Solutions | Mining Screen | 9 | 88 | Ore Dewatering | SS 304 | 12 | 12–15 |
ScreenTech Rotary | Rotary Drum Screen | 5 | 80 | Wastewater, Slurry | SS 304/Polymer | 6 | 8–12 |
Evidently, Coanda screen manufacturers consistently lead in terms of debris exclusion and low-maintenance operation, followed by mining and rotary drum screen manufacturers. Rotary drum screens, while efficient for some wastewater applications, generally offer shorter lifespans and more frequent service intervals.
Tailored Solutions: Meeting Unique Industry Challenges Through Customization
No two project sites are alike, nor are their screening demands uniform. Top manufacturers have invested heavily in offering tailored engineering solutions, encompassing custom lengths and widths, module angles, and aperture sizing. Increasingly, computational fluid dynamics (CFD) modeling is standard during the design phase, allowing for precise simulation of complex intake geometries and debris load scenarios.
For example, in alpine hydropower dams, snowmelt debris and rapid flow rates necessitate custom anti-icing features and robust mounting configurations—features major suppliers can now integrate seamlessly. In high-volume mining operations, screens are often built with reinforced frames to withstand heavy suspended solids and can be fitted with detachable panels for swift on-site replacement.
Importantly, customization extends to installation support, operator training, and real-time remote monitoring integrations, ensuring higher uptime and safer operations over the full asset lifespan. This trend is redefining the role of coanda screen manufacturers from simple product vendors to holistic technology partners driving project success.
Profiles in Success: Case Studies Demonstrating Performance
Proven field performance remains the ultimate test of any screening solution. Case studies from leading sectors highlight measurable improvements in efficiency, compliance, and cost-effectiveness.
Case 1: Hydropower Diversion Intake, British Columbia, Canada
After retrofitting a legacy bar screen intake with custom-engineered Coanda screens from a market-leading manufacturer, debris passage rates fell by 93%, and unplanned maintenance dropped from 18 interventions per year to just two. This resulted in annual O&M cost savings upwards of $54,000.
Case 2: Gold Mine Effluent Screening, Western Australia
Deployment of a high-capacity mining screen improved dewatering throughput by 22%, supporting increased mineral recovery rates and reduction in water use.
Case 3: Municipal Wastewater Plant, South America
Rotary drum screens reduced solids loads in clarifiers, but required replacement every 9 years, with substantial manual cleaning compared to alternative wedge-wire options.
These outcomes demonstrate both the dramatic technical advantages and long-term economic value of close collaboration with experienced screen manufacturers. Projects prioritizing advanced engineering consistently report improved reliability and compliance outcomes.
Strategic Factors in Selecting Your Screening Partner
The process of choosing the right manufacturer entails far more than cost or name recognition. Strategic buyers place emphasis on the following criteria:
- Design expertise and track record: Experience in similar flow and loading environments is critical for long-term satisfaction.
- Material certification: Full traceability and compliance with DIN, ASTM, or equivalent standards are non-negotiable in regulated industries.
- Local technical support: Prompt engineering backup, especially during commissioning and challenging conditions, ensures minimal delays.
- Sustainability: Recyclability and energy footprint of materials used reflect broader ESG goals.
- Full lifecycle cost: Consideration of scheduled downtime, spare part availability, and total OPEX alongside upfront CAPEX delivers a truer indication of value.
Conclusion: Choosing Coanda Screen Manufacturers for Future-Proof Solutions
As global regulatory and operational demands escalate, organizations cannot afford to compromise on inlet screening. Coanda screen manufacturers are redefining the standard for efficiency, durability, and tailor-fit solutions. Their technology not only achieves market-leading debris exclusion but also minimizes environmental impact and long-term operational cost. When compared with traditional mining screen manufacturers and rotary drum screen manufacturers, the competitive advantage of sophisticated engineering and proactive support is indisputable. By aligning with established manufacturers at the forefront of innovation, project stakeholders position themselves for sustainable success and resilient infrastructure far into the future.
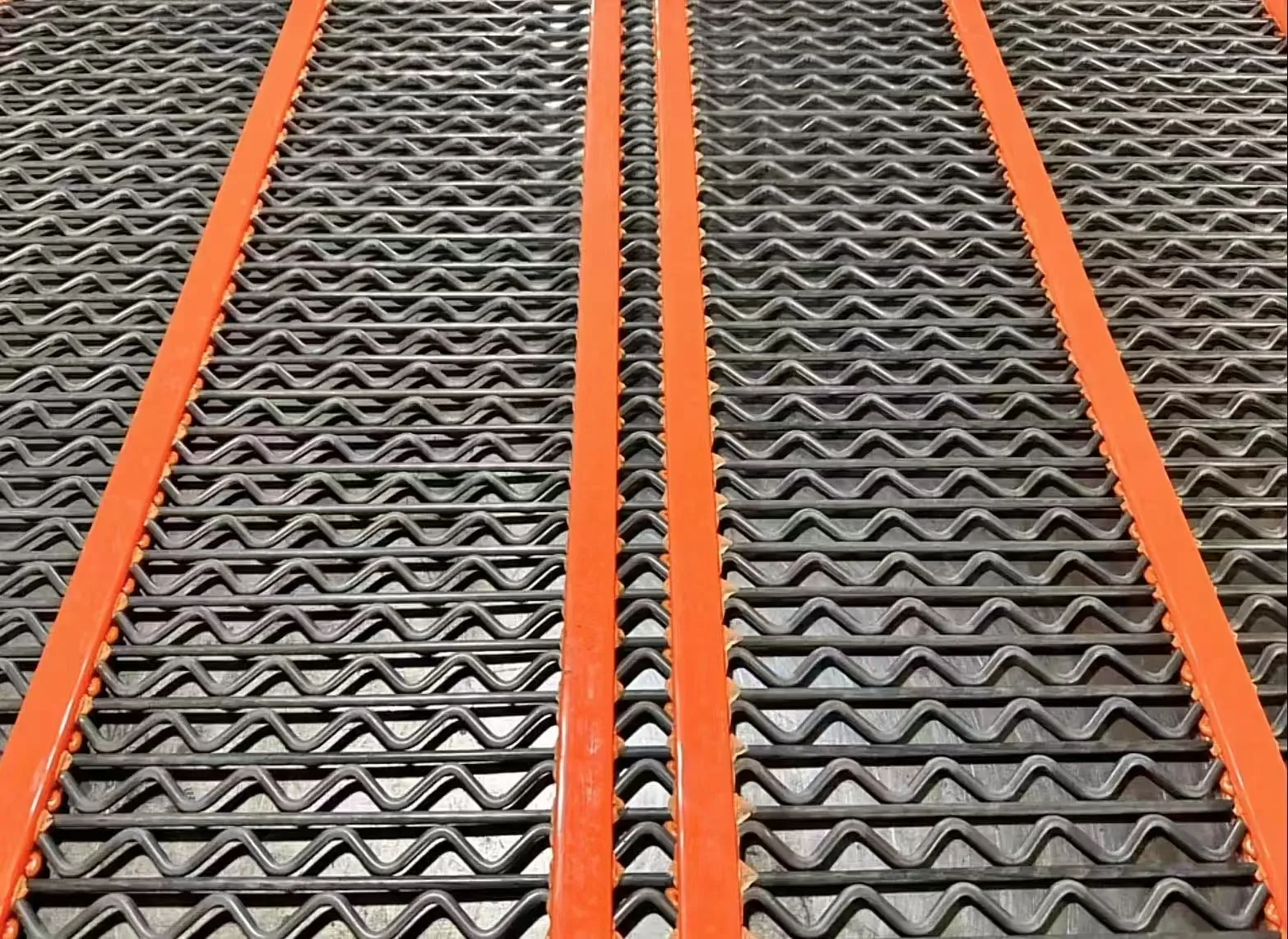
(coanda screen manufacturers)