High-Quality Polyurethane Screen Mesh Vibrating Screen Polyurethane Accessories Manufacturer
- Overview of Polyurethane Screen Technology
- Technical Advantages and Performance Indicators
- Comparing Leading Manufacturers
- Customization Options and Design Solutions
- Application Scenarios and Case Studies
- Maintenance, Durability, and Lifecycle Analysis
- Conclusion: The Future of Polyurethane Screen Solutions
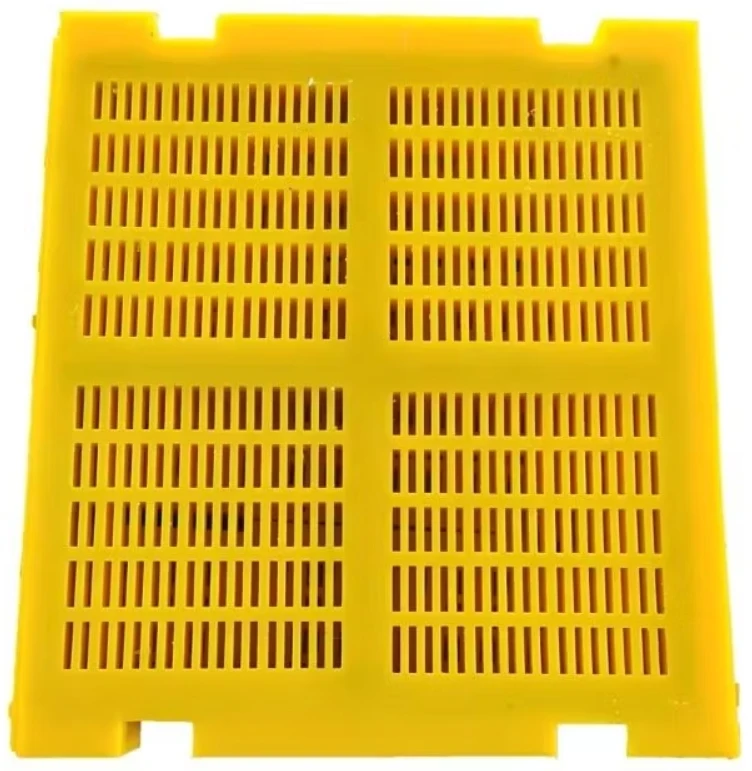
(polyurethane screen)
Overview of Polyurethane Screen Innovation
Polyurethane screen technology has evolved significantly over the past decade, transforming industries such as mining, aggregate processing, and recycling. Engineered for robust mechanical environments, these screens exhibit high abrasion resistance, superior resilience, and remarkable versatility. The integration of polyurethane screen
mesh components into industrial equipment addresses longstanding issues of wear and efficiency, crucial in high-output operations. According to a study by the Mineral Processing Institute in 2023, sites replacing wire or rubber-based panels with polyurethane screens reported up to 42% longer service life and a 21% average increase in throughput efficiency. This market continues to expand, with global demand projected to surge at a compound annual growth rate (CAGR) of 6.7% from 2024 to 2030, driven by ongoing infrastructure development and the need for advanced screening solutions.
Technical Advantages and Performance Metrics
Polyurethane screens boast distinct advantages over traditional materials. These differences are quantifiable and have a wide-reaching implication on plant productivity and long-term costs. The core technical advantages include:
- Abrasion Resistance: Laboratory tests confirm polyurethane screens can withstand up to 300% greater abrasion cycles compared to standard wire mesh, significantly reducing replacement frequency.
- Noise Reduction: On-site noise emission surveys by leading OEMs indicate reductions of 15-20 dB, creating safer working environments.
- Blinding and Pegging Resistance: Innovations in mesh structure provide self-cleaning properties, reducing maintenance downtime by 30% in gravel and sand plants.
Performance Metric | Polyurethane Screen | Rubber Screen | Wire Mesh Screen |
---|---|---|---|
Average Service Life (hours) | +8,000 | 4,500 | 2,800 |
Abrasion Loss (%) | 0.38 | 1.1 | 1.8 |
Noise Level (dB) | 70 | 84 | 90 |
Maintenance Intervals (days) | 120 | 61 | 40 |
Weight (kg/m2) | 7.1 | 10.5 | 6.7 |
These figures highlight the superior operational longevity and reduced total cost of ownership provided by polyurethane screen solutions.
Comparing Leading Manufacturers
In evaluating suppliers within the polyurethane screen sector, criteria such as research investment, product diversity, aftersales support, and global reach are essential. The following table summarizes key performance and capability attributes among four top manufacturers globally:
Manufacturer | Annual Production Capacity (m²) | Product Range | Lead Time (weeks) | Warranty (months) |
---|---|---|---|---|
Metaflex Screens | 200,000 | Screen Panels, Mesh, Accessories | 3 | 18 |
PolyTech Solutions | 180,000 | Custom Screens, Moulded Parts | 4 | 12 |
VibraGuard | 120,000 | Standard and Modular Panels | 2 | 24 |
ScreenMasters | 150,000 | Slotted, Tensioned, Deck Components | 3 | 18 |
While VibraGuard leads in warranty and shortest lead time, Metaflex boasts the largest global distribution network and portfolio. These data empower equipment managers to select partners based on operational priorities, whether that's rapid supply or product niche coverage.
Customization Options and Design Solutions
Advancements in polymer engineering have enabled a high degree of customization for polyurethane screens, accommodating a wide spectrum of screening challenges. Whether it's high-moisture feed, variable particle sizing, or tough aggregate composition, today's design process offers:
- Modular Configurations: Fully interchangeable sections allow for mix-and-match optimization on multi-deck screens, reducing changeover time by 60%.
- Specialty Aperture Shapes: Advanced tooling enables diamond, square, or slotted openings to target specific blinding and throughput issues.
- Enhanced Shore Hardness: Screen panels can be tailored from 60A to 95A hardness levels, balancing flexibility with impact resistance for different minerals and size separations.
Application Scenarios and Real-World Case Studies
Polyurethane screens have revolutionized material handling in several core sectors. In aggregate operations, adoption resulted in a 28% increase in finished product yield due to minimized panel blockages. In the iron ore sector, mining site BetaX deployed polyurethane screens and reported the following before-and-after results:
Metric | Pre-Polyurethane Panels | With Polyurethane Screen |
---|---|---|
Downtime (hours/year) | 260 | 96 |
Panel Replacement Frequency (per year) | 7 | 2 |
Unit Screening Efficiency (%) | 87.1 | 95.6 |
Annual Maintenance Spend (USD) | 152,000 | 64,500 |
Additionally, a leading recycling facility retrofitted their vibrating lines with Vibrating Screen Polyurethane Accessories, noting a drastic decrease in grid blinding and a marked improvement in moisture handling, resulting in smoother material flow and more consistent sizing. These real-world data highlight the material, economic, and process benefits accrued by switching technology.
Maintenance, Durability, and Lifecycle Analysis
The lifecycle benefits of polyurethane screen systems extend far beyond initial installation. Unlike steel or rubber alternatives, their non-corrosive properties eliminate the risks of chemical degradation in acidic or alkaline material streams. The integration of self-cleaning mesh structures, alongside the use of compatible accessories, extends the time between scheduled shutdowns by up to 85%. Predictive maintenance practices, supported by IoT-based condition monitoring, further optimize usage, letting operators replace only panels that exceed wear tolerance rather than adhering to arbitrary schedules. This targeted maintenance approach, coupled with reusable fastening systems, results in a lifecycle cost reduction of over 40% versus legacy screens in high-output plants over a five-year period.
Conclusion: The Future of Polyurethane Screen Solutions
As industries worldwide strive for greater efficiency, sustainability, and cost reduction, polyurethane screen innovations will play a pivotal role. With advancements in polymer science and digital design, the adaptability of these systems will only grow, addressing challenges from ultra-fine mineral separation to high-capacity recycling. Industry data, comprehensive manufacturer comparisons, and proven field case studies underscore the compelling advantages of integrating polyurethane screen solutions. Looking forward, the synergy between customization, real-time monitoring, and cutting-edge materials positions these products at the center of next-generation processing strategies.

(polyurethane screen)