High-Efficiency Parabolic Screen Filter for Wastewater Treatment Durable Parabolic Screen Solutions
- Introduction to Parabolic Screen Filter Technologies
- Data Highlights and Performance Metrics
- Advanced Technical Advantages
- Manufacturer Comparison Table: Features and Specifications
- Customized Solutions for Diverse Wastewater Challenges
- Real-World Application Case Studies
- Conclusion: Parabolic Screen Filter Impact on Wastewater Management
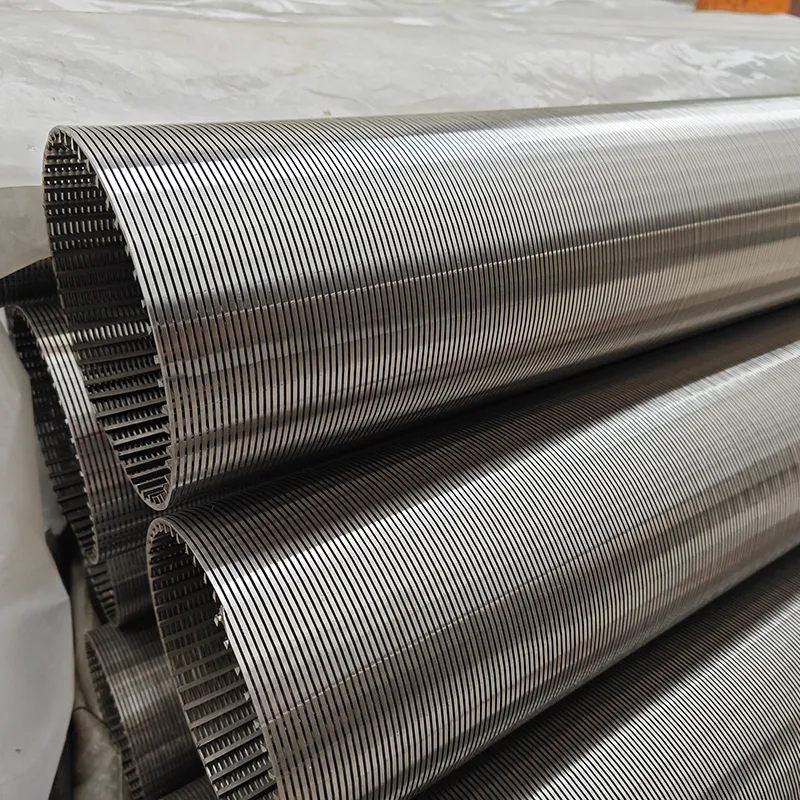
(parabolic screen filter)
Introduction to Parabolic Screen Filter Technologies
The demand for enhanced solids-liquid separation has brought parabolic screen filter
s to the forefront of wastewater treatment innovation. These devices, known for their high efficiency and reliability, employ a curved or “parabolic” static screen that utilizes gravity to separate solids from liquid streams. With industries increasingly required to meet stringent discharge limits and recycle process water wherever possible, parabolic screen filter systems are reshaping process economics. Statistics reveal that by the end of 2023, the global industrial wastewater treatment market exceeded $145 billion, a number projected to rise swiftly as filtration technologies continue to evolve. Specifically, industries such as food processing, municipal treatment, and pulp & paper have adopted parabolic screen filters to achieve TSS (Total Suspended Solids) removal efficiencies consistently above 80%, significantly reducing the downstream load on biological treatment phases.
Data Highlights and Performance Metrics
Recent industry benchmarking studies highlight that parabolic screen equipment outperforms many traditional rotary drum screens and wedge wire solutions. Typical flow rates handled are between 5 m3/h and 150 m3/h, depending on the model size and screen aperture (ranging from 50 microns to 2 mm). Laboratory tests on municipal influent with 600 mg/L TSS input have shown that optimized parabolic screen configurations achieve an average 78-92% solids reduction, correlating to effluent concentrations as low as 45 mg/L. Standard models consume almost negligible energy as screens operate passively, with only intermittent rinsing required, resulting in maintenance costs up to 60% lower than comparable drum screens.
Advanced Technical Advantages
Technological refinement over recent years has established parabolic screen filters as the preferred choice for preliminary and secondary solid-liquid separation in large-scale facilities. The unique parabolic curvature maximizes hydraulic throughput while minimizing blinding, allowing continuous operation with minimal interruptions. Self-cleaning enhancements—including vibrating screens, automated spray bars, and anti-fouling surface coatings—extend lifespan and preserve performance. In fact, filter lifespans now routinely exceed 8 years with proper servicing. Additionally, the open construction of these filters significantly reduces the hazard of microbial accumulation and odor generation, improving workplace conditions. Versatility is also a key advantage; screens can be customized with variable slot openings and angles to target specific solids size fractions. Unlike rotating mechanisms, the static design boasts only one or two moving parts, reducing breakdown risk and ensuring reliability even during extended operations.
Manufacturer Comparison Table: Features and Specifications
Manufacturer | Flow Rate (m3/h) | Screen Aperture (micron) | TSS Removal Efficiency (%) | Energy Consumption | Average Lifespan (years) | Customization Options |
---|---|---|---|---|---|---|
HydroTech | 5 – 60 | 100 – 2000 | 80 – 90 | Passive | 7 | Screen angle, aperture size, spray bar |
AquaFine Solutions | 10 – 120 | 50 – 1500 | 82 – 92 | Passive | 8 | Surface coating, frame materials |
FlowGuard | 8 – 100 | 75 – 1200 | 75 – 88 | Passive | 6 | Replaceable modules, anti-fouling |
EcoScreen Technologies | 12 – 150 | 60 – 1800 | 79 – 91 | Passive | 9 | Hybrid slot types, automation |
Reviewing the data above, it's evident that modern parabolic screen filters deliver industry-leading efficiency and operational savings, enabling users to select units matched precisely to their process needs.
Customized Solutions for Diverse Wastewater Challenges
A distinguishing factor for parabolic screen designs is their capacity for customization across industrial, municipal, and food-grade wastewater streams. For high-fiber effluents, for example, screens with wider slot openings prevent frequent clogging and promote free drainage, while finer slots (down to 50 microns) target paint, textile, or dairy process water requiring stringent particulate control. Facilities can further tailor their solutions with stainless steel or corrosion-resistant composite frames based on aggressive chemical exposure profiles. Integrating pre-filtration, modular stacking, or hybridization with subsequent filtration technologies (such as dissolved air flotation) has led to up to 30% higher system throughput. Automated monitoring and remote adjustment of spray bar cycles enable further optimization, especially where influent loads fluctuate significantly during production peaks. This adaptability ensures parabolic screen wastewater treatment remains robust, cost-effective, and compliant with evolving regulatory requirements.
Real-World Application Case Studies
Numerous installations worldwide underscore the dependable performance and scalability of parabolic screen wastewater systems. In a large dairy processing plant in Wisconsin handling 75 m3/h, installation of parabolic screens reduced daily solids loading by roughly 88%, slashing sludge hauling expenses by $45,000 annually. In a municipal treatment works in Northern Europe, retrofitting aging rotary drums with next-generation parabolic screens resulted in a 15% net increase in hydraulic capacity, enabling the plant to reliably treat up to 40% more peak stormwater flows without compromise in effluent quality. Another compelling example comes from Southeast Asia where a paper mill achieved a 10x increase in screen life after upgrading to automated, self-rinsed parabolic filters—downtime dropped to less than 1 shift per quarter. These real-world examples demonstrate not only the robust efficiency but also the clear economic and operational benefits driving widespread adoption.
Conclusion: Parabolic Screen Filter Impact on Wastewater Management
The parabolic screen filter represents a paradigm shift in the field of wastewater treatment, providing users with a high-efficiency, low-maintenance solution suitable for a broad spectrum of industrial and municipal challenges. Performance data and field experience confirm the ability of these systems to reduce solids loads, optimize water reuse, and decrease operational costs with outstanding reliability. As legislative pressure on discharge quality intensifies and water conservation becomes ever more critical, the parabolic screen filter remains indispensable to future-ready treatment infrastructures. Businesses and municipalities are encouraged to evaluate these advanced systems to strengthen environmental compliance, sustainability, and profitability.
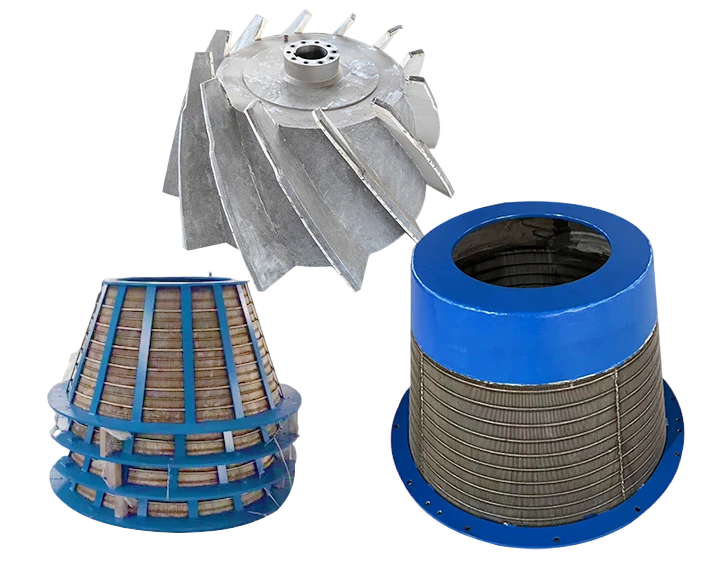
(parabolic screen filter)