High-Quality Perforated Panel Durable Wedge Wire Screen & PU Screen Panels for Industrial Use
- Introduction to perforated panel
and its industrial relevance - The technology behind wedge wire screen panels: Precision and durability
- Innovative properties of PU screen panels for heavy-duty screening
- Comparative analysis: Technical and economic advantages
- Customization Options: Tailored solutions for diverse industries
- Real-world applications and case studies: Measured impact
- Conclusion: The evolving value of perforated panel solutions
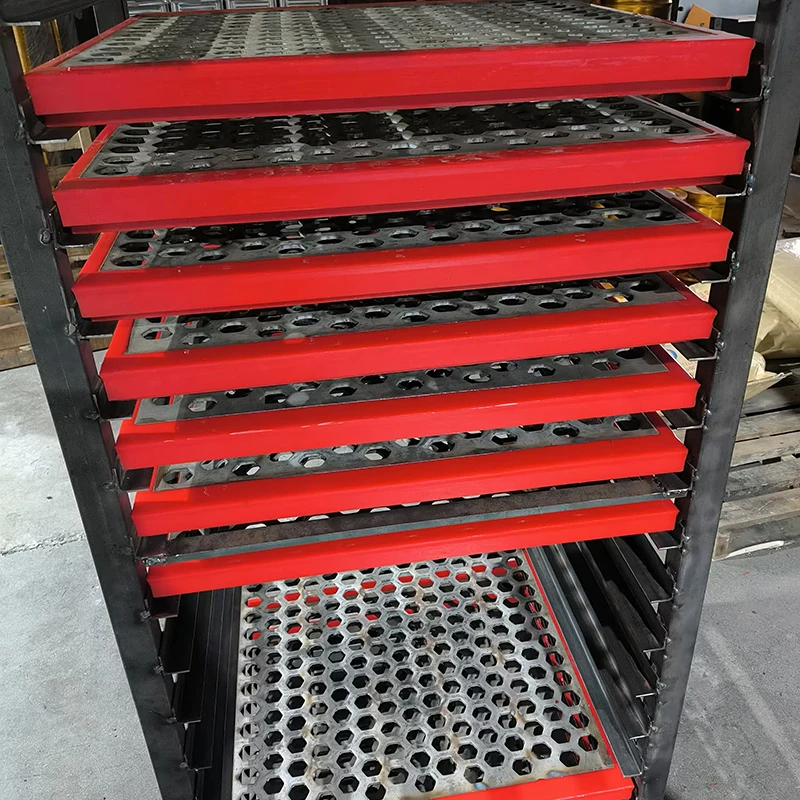
(perforated panel)
Introduction to perforated panel and Its Industrial Relevance
As global demand for efficient material separation grows, the perforated panel has emerged as a key element in many industries. These panels, designed with precision holes or slots, offer exceptional performance in screening, filtering, and even decorative applications. From aggregate sorting in quarries to particle filtration in food processing plants, the adoption of perforated panel technologies reflects a pragmatic response to increasing throughput requirements. Statistically, the global market for perforated metal panels is projected to grow at a CAGR of 4.7% between 2023 and 2030, underlining the sustained necessity for innovative screening solutions across diverse sectors. Their robustness, adaptability, and versatility make perforated panels indispensable, whether in basic mechanical separation or as crucial components in complex systems that demand both strength and precision.
The Technology Behind Wedge Wire Screen Panels: Precision and Durability
Wedge wire screen panels elevate separation technology with their unique profile and construction. Manufactured using stainless or duplex steels, these panels consist of V-shaped wires welded onto support rods, producing a continuous slot with precise tolerances, typically ranging from 0.02mm to 10mm. This design vastly reduces clogging and significantly enhances throughput compared to conventional flat screens. For example, industrial water treatment facilities report up to 25% higher efficiency rates when switching from traditional screens to wedge wire configurations. The inherent open area, often exceeding 60%, maximizes flow rates while maintaining structural integrity, even under intense pressure environments. Technological advancements such as automated welding and laser-calibrated slotting further secure uniformity across large production volumes, ensuring dependable performance where accuracy and longevity are critical.
Innovative Properties of PU Screen Panels for Heavy-Duty Screening
In environments where abrasion, impact, and chemical resistance are vital, Polyurethane (PU) screen panels have redefined industry standards. Their elastomeric matrix withstands corrosive materials and high-velocity particles that frequently degrade conventional metal alternatives. Empirical testing has shown that PU screen panels can outperform stainless steel by delivering 3 to 5 times longer operational lifespan, particularly in mining and aggregate processing sectors. Thanks to customizable slot dimensions (from 0.1mm upwards), these panels enable enhanced selectivity and precise product grades. Key technical achievements include integrated reinforcement frames for high-load tolerances and modular locking systems facilitating rapid, tool-free replacement. Such features not only reduce downtime but also maintain consistent screening performance throughout the product’s lifecycle, contributing to lower total cost of ownership and supporting sustainable industrial workflows.
Comparative Analysis: Technical and Economic Advantages
The choice between perforated panel, wedge wire screen panel, and PU screen panel involves balancing technical requirements, operational context, and economic factors. The following table details core parameters and performance metrics to support decision-making:
Panel Type | Main Material | Slot/Opening Range (mm) | Open Area (%) | Expected Lifespan | Maintenance Interval | Initial Cost |
---|---|---|---|---|---|---|
Perforated Panel | Mild/Stainless Steel, Aluminum | 0.5 – 20 | 20 – 60 | 2 – 5 years | Bi-annual | $$ |
Wedge Wire Screen Panel | High-Grade Stainless, Duplex Steel | 0.02 – 10 | 40 – 70 | 5 – 12 years | Annual | $$$ |
PU Screen Panel | Polyurethane, Optional Steel Frame | 0.1 – 50 | 35 – 50 | 6 – 15 years | Annual | $$$ |
While the perforated panel is both affordable and versatile, wedge wire panels deliver tight tolerance and minimal blinding where critical filtration is necessary. PU screen panels, with their resilience and longevity, often provide the best ROI in abrasive conditions despite a higher upfront investment.
Customization Options: Tailored Solutions for Diverse Industries
Each industrial application presents unique operational demands, making customization indispensable for optimal screening performance. Perforated panels can be tailored by adjusting hole shapes (round, square, elongated), substrate thickness (1mm to 25mm), and sheet size to precisely meet architectural, sorting, or ventilation needs. Wedge wire panels offer adaptable profiles, slot sizing as fine as 20 microns, and materials engineered for corrosive or high-temperature environments, including duplex or super duplex alloys for offshore and petrochemical use. For PU screen panels, users may specify frame reinforcements, fastening types, and advanced surface treatments to enhance anti-fouling or anti-abrasion properties. These customizations not only extend the solution’s operational lifespan but also optimize energy consumption, process yield, and maintenance intervals, ensuring that each installation is both cost-effective and environmentally responsible.
Real-World Applications and Case Studies: Measured Impact
Success in real-world settings showcases the tangible value of advanced screening panels. In South Africa, a leading mining operation upgraded to PU screen panels, resulting in a 40% drop in downtime and a 50% reduction in annual replacement costs over two years. Similarly, a municipal water filtration plant in Germany transitioned to wedge wire screen panels, achieving more consistent filtrate quality and a reported 95% operational uptime over three years. In architectural projects, custom-designed perforated panels have been implemented in commercial facades, improving building ventilation by up to 30% and contributing to LEED certification for energy efficiency. These examples underscore not only the adaptability of such panels but also their measurable impact in productivity, resource conservation, and compliance with rigorous industry regulations.
Conclusion: The Evolving Value of perforated panel Solutions
The relentless evolution of industrial processes demands components that deliver on performance, reliability, and adaptability. Modern perforated panel solutions, alongside wedge wire and PU panels, exemplify this convergence of quality and innovation. By integrating advanced manufacturing techniques with user-centric customization, manufacturers now offer screening products that minimize operational costs and maximize output. The trend towards smart, sustainable solutions in filtration, separation, and decorative applications highlights the ongoing significance of these panels, ensuring industries remain competitive as demands change. By carefully evaluating application needs and leveraging data-backed decision-making, companies can unlock new efficiencies and sustain long-term growth.
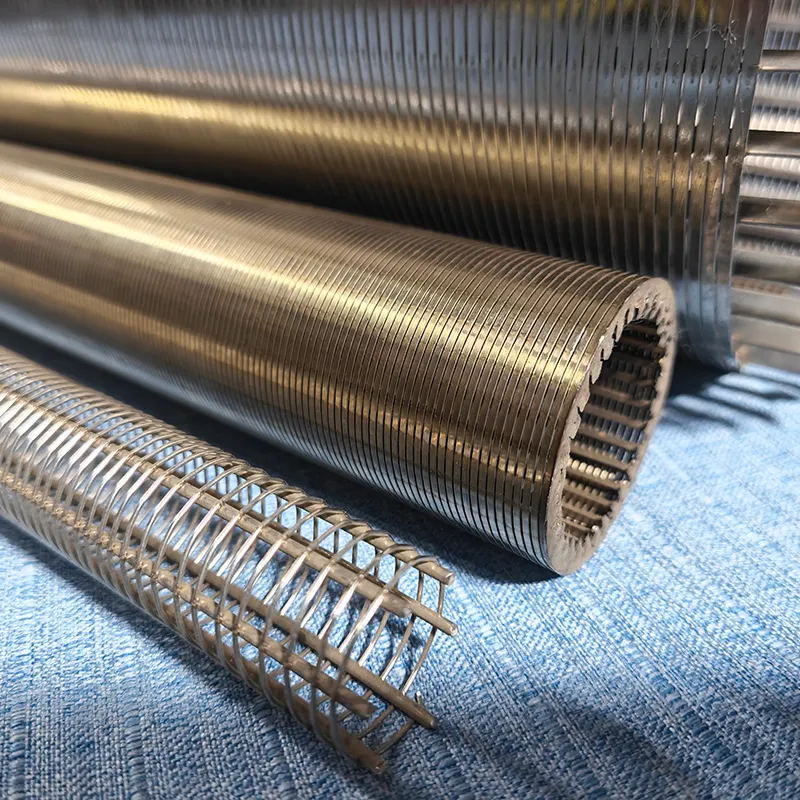
(perforated panel)