High-Efficiency Wastewater Screens for Optimal Treatment Bar & Parabolic Screens Solutions
- Introduction to Wastewater Screens: Functions and Importance
- Types and Technical Advantages of Wastewater Screens
- Comparative Analysis of Leading Manufacturers
- Tailoring Wastewater Screens: Custom Engineering Solutions
- Applications and Case Studies in Municipal and Industrial Sectors
- Operating Data: Performance Metrics and Industry Trends
- Conclusion: The Future of Wastewater Screens
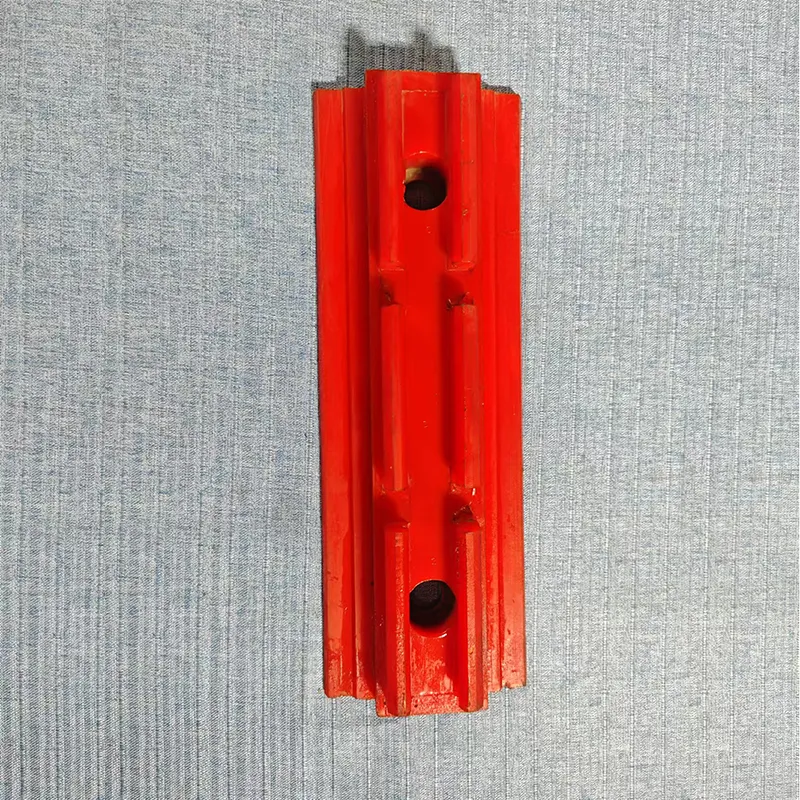
(wastewater screens)
Introduction to Wastewater Screens: Functions and Importance
Wastewater screens are fundamental components in both municipal and industrial water treatment facilities. Their primary role is to remove solids, debris, and particulate matter at initial treatment stages, preventing downstream equipment from becoming clogged or damaged. Globally, rising urbanization and industrialization have highlighted the critical nature of reliable screening systems. According to a 2023 global market analysis, the wastewater treatment equipment sector is projected to grow at a CAGR of 6.8% through 2028, with screens representing over 19% of total primary equipment investment. High-performance screening can reduce suspended solid loads by 30–60% and extend the lifespan of pumps, tanks, and biological systems, placing wastewater screens
at the heart of sustainable water management strategies.
Types and Technical Advantages of Wastewater Screens
Wastewater screens span a wide spectrum—from classic bar screens to advanced parabolic and drum screen technologies. Bar screens in wastewater treatment remain widely used for coarse screening, capturing large objects with robust steel bars set at specific intervals. Their simple, rugged design allows for manual or automated cleaning. Parabolic screen wastewater units are designed for finer filtration; they rely on precise curve geometry and continuous, gravity-fed flows to separate smaller particulates. Drum and rotary drum screens advance the process by providing automated, high-throughput removal of finer material, ideal for industrial plants with variable influent loads. Technical innovations have enabled modern screens to achieve removal rates of up to 90% for particles >2mm, with some parabolic units handling flows exceeding 6,000 m³/day while maintaining low head-loss and energy consumption.
Operational efficiency is now augmented with integrated control systems and self-cleaning mechanisms, which substantially reduce labor requirements and risk of system downtime. Many facilities report maintenance cost reductions of 20–35% following the implementation of advanced screening solutions, underscoring the value of technical innovation in this product segment.
Comparative Analysis of Leading Manufacturers
Selecting the right wastewater screens involves not only technical specifications, but also an understanding of supplier reliability and overall cost-effectiveness. The following table contrasts prominent global manufacturers based on screen type, maximum flow capability, energy consumption, and maintenance intervals:
Manufacturer | Screen Type | Max Flow (m³/day) | Particle Size Removal (mm) | Avg. Energy Cons. (kWh/1000 m³) | Maintenance Interval |
---|---|---|---|---|---|
HydroTech | Rotary Drum | 8,500 | 1.5 | 3.8 | 12 months |
EnviroScreen Corp. | Parabolic | 6,200 | 1.0 | 2.5 | 18 months |
ClearWater Solutions | Bar Screen | 12,000 | 6.0 | 4.5 | 9 months |
ScreenTech Ltd. | Step Screen | 7,100 | 3.0 | 3.0 | 14 months |
While HydroTech’s rotary drum offers the highest flow, EnviroScreen’s parabolic design leads in energy efficiency and extended maintenance cycles. For large municipal plants prioritizing low labor and running costs, drum and parabolic screens often outperform traditional bar screens.
Tailoring Wastewater Screens: Custom Engineering Solutions
The diversity of influent waste streams demands customized screening approaches. Modern manufacturers provide engineering consultations to tailor screens for exact facility requirements—flow characteristics, expected debris size, chemical compatibility, and spatial constraints all inform the final solution.
A custom-designed system may feature variable bar spacings, hybrid screen geometries (combining rotary/drum and parabolic stages), and fully automated debris handling. Sensors can now integrate with plant-wide automation, performing predictive maintenance scheduling and maximizing uptime. According to industry data, facilities that implemented tailored screen solutions observed a 17% average increase in solid collection efficiency and a 22% reduction in unplanned service events within the first operational year.
Choosing a partner with in-house engineering and prototyping capability ensures not only compliance with stringent regulatory standards, but also long-term adaptability as process requirements evolve.
Applications and Case Studies in Municipal and Industrial Sectors
Wastewater screens serve a dual purpose: protecting sensitive downstream processes and enabling water reuse. Case histories from municipal, food processing, and petrochemical industries illustrate diverse application needs. The City of Leeds introduced parabolic screens at three main pumping stations; within 18 months, pump blockage events dropped by over 83%. In another instance, a dairy processing facility in Wisconsin replaced aging bar screens with a step screen and parabolic system, improving BOD removal by 25% and slash manual cleaning hours by 40% per month.
In oil and gas operations, parabolic screen wastewater equipment is prized for separating oil-laden solids while minimizing chemical usage. These units combine small footprints with high capacity, which is crucial in retrofits where space is at a premium. Globally, over 70% of new large-scale effluent plants adopted some form of fine screening between 2019 and 2022, signaling a decisive shift towards higher process reliability and effluent quality.
Operating Data: Performance Metrics and Industry Trends
Performance measurement of wastewater screens has become increasingly sophisticated, with integrated instrumentation providing real-time data on throughput, solids load, and cleaning cycles. Industry benchmarking indicates average solids removal rates of 55–85% depending on screen type and influent composition. Drum and parabolic screen units typically demonstrate superior consistency in variable flow regimes, with flow deviation coefficients under 0.12 compared to 0.27 for manual bar screens.
Efficiency improvements extend beyond process metrics: a 2021 meta-analysis showed that facilities upgrading to automated screening solutions reduced chemical preconditioning needs by up to 18%, leading to significant operational savings. The demand for low-carbon, energy-optimized equipment is pushing manufacturers to develop ultra-low head-loss screens and variable frequency drive motors, offering energy savings of 16–24% annually.
Conclusion: The Future of Wastewater Screens
As regulatory standards tighten and climate resilience becomes a core priority, wastewater screens will solidify their strategic role in modern treatment infrastructure. Ongoing advances in sensor integration, energy consumption, and materials science are set to further boost operational efficiency. With parabolic screen wastewater technologies poised for wider adoption, and bar screens in wastewater treatment evolving through automation and hybridization, future facilities can expect unparalleled system reliability and lifecycle cost savings. The integration of smart diagnostics, custom engineering, and robust manufacturer partnerships will determine the next generation of wastewater screens, safeguarding both environmental and business objectives.
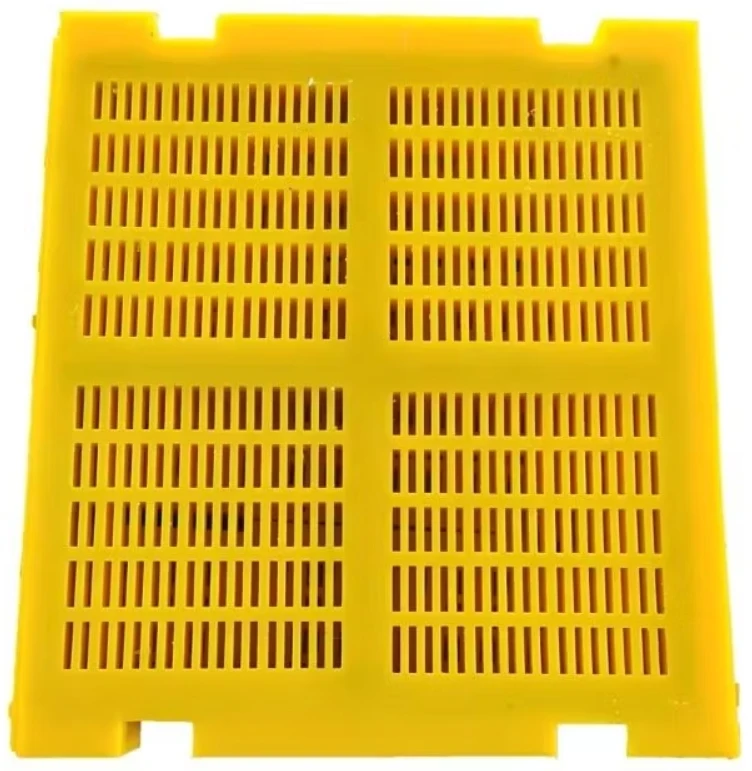
(wastewater screens)