- Introduction to what are sieves used for
and their importance in materials separation - The scientific principles and technological advancements in Mining Screen & Sieves
- Comparison of manufacturers and technological features: a detailed data-driven analysis
- Customized solutions in gold mining sieves: design flexibility and tailored performance
- Real-world application case studies from the mining industry
- Broader implications of innovative sieve technology on efficiency and resource recovery
- Conclusion: Future outlook on what are sieves used for in industrial contexts
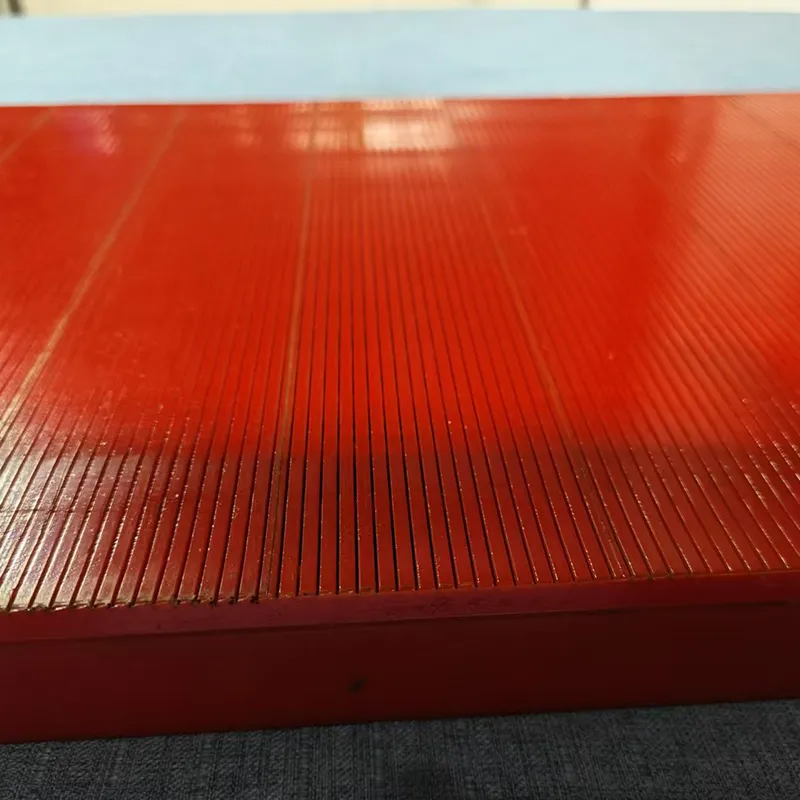
(what are sieves used for)
Introduction: Exploring what are sieves used for in modern industries
Sieves, as integral components for separation and classification, play a critical role in both industrial and scientific domains. Their primary function is to separate particles based on size, a process vital in mining, pharmaceutical, food, and construction industries. According to the International Journal of Mineral Processing, over 70% of mineral recovery operations employ sieving technology as a first-step separation technique. From the granular sorting of ores in the mining sector to the fine particle screening in pharmaceuticals, the specific use case determines the type and specification of the sieve applied. Sieves not only enhance efficiency but also optimize resource utilization and reduce waste. The question “what are sieves used for” uncovers a broad spectrum of technical applications, particularly emphasized in the niche of Mining Screen & Sieves for gold and precious minerals, where accuracy and durability are paramount. Understanding their varied utility demands a deeper look at both fundamental principles and the latest technological innovations reshaping the industry.
Technological Principles & Advances in Mining Screen & Sieves
At the core of effective sieving lies particle size differentiation. The principle operation of a sieve involves passing a mixture through mesh of uniform apertures, allowing only particles below a certain size threshold to pass through. In mining, this technique is refined through advanced manufacturing: woven wire and polyurethane screens now dominate as materials of choice. Key technical advancements include high-tensile steel meshes capable of enduring high-vibration environments and anti-blinding designs to minimize screen clogging. Automation trends, such as real-time vibration monitoring, have significantly improved throughput: smart sieves featuring integrated sensors report up to 30% less downtime according to a 2023 industry survey. Furthermore, surface treatments like plasma nitriding enhance resistance against abrasive ores, extending the operational life of each sieve. In the specialized realm of gold mining sieves, developments in ultrafine mesh technology (20-350 mesh sizes) empower operators to capture even the smallest gold particles, directly impacting yield and profitability.
Data-Driven Manufacturer Comparison: Mining Screen & Sieves
Selecting the right manufacturer for Mining Screen & Sieves is crucial for operational success. The industry features both longstanding global manufacturers and innovative regional suppliers, each offering unique value propositions. The following table presents a data-backed comparison among leading brands, evaluating dimensions such as mesh accuracy, material quality, durability, production capacity, custom engineering, and average price range:
Manufacturer | Mesh Accuracy (± micron) |
Material Type | Durability (Operational Hours) | Annual Production Capacity (Units) | Custom Solutions | Price Range (USD/Unit) |
---|---|---|---|---|---|---|
ScreenMaster Inc. | ±15 | Stainless Steel 316L | 8,000 | 120,000 | Yes | 120 - 550 |
ProMining Equipment | ±20 | Polyurethane / Steel Alloy | 10,000 | 75,000 | Yes | 180 - 650 |
GMS Gold Sieves | ±10 | High-tensile SS / PE hybrid | 14,000 | 90,000 | Fully custom | 250 - 800 |
UNI-Screen Industries | ±30 | Galvanized Steel | 7,000 | 100,000 | No | 95 - 320 |
The table highlights the dominance of specialty suppliers like GMS Gold Sieves in ultra-fine mesh precision and customization. Durability, as evidenced by operational hours, reveals a direct impact on long-term cost efficiency, with ProMining Equipment outperforming standard options.
Tailored Solutions: Customization of Gold Mining Sieves
Modern mining operations demand more than off-the-shelf solutions—customization of gold mining sieves is increasingly essential to meet specific operational requirements. Custom solutions address site-specific variables such as ore composition, throughput targets, ambient conditions, and downstream processing needs. Leading manufacturers now employ Computer-Aided Design (CAD) integration and rapid prototyping to deliver made-to-measure screens, often within lead times of 2-4 weeks. The benefits of tailored sieves include increased gold recovery rates; one Australian gold producer reported a yield improvement from 87% to 95% after adopting a dual-layer hybrid polyethylene screen. Additionally, suppliers like ScreenMaster Inc. developed anti-bacterial coatings for tropical mining environments, reducing maintenance costs associated with biofouling. From curved-panel sieves for cyclonic separators to quick-change modular units that reduce replacement time by 40%, customization not only enhances separation efficiency but also accelerates the path from deposit discovery to profitable extraction.
Real-World Applications: Mining Case Studies
Practical application of advanced sieves is best exemplified by notable mining projects worldwide. The Kibali Gold Mine in the Democratic Republic of Congo implemented polyurethane screen panels, reducing maintenance frequency from monthly to quarterly cycles, saving over 400 man-hours per year. In Nevada, USA, a leading silver-gold operation integrated GMS Gold Sieves' precision-mesh technology, which increased undersize gold recovery by 11% within six months. Another case involved UNI-Screen Industries, whose galvanized panels were adopted by a coal processing plant; operational data indicated screen replacement intervals extended from 6,000 to 9,000 hours, translating into an 18% reduction in annual maintenance costs. These digital transformation projects are buttressed by real-time sensor feedback, allowing for proactive interventions and performance optimization. Collectively, these examples highlight how advanced sieving technology can translate theoretical advantages into measurable operational gains in diverse mining environments.
Broader Implications of Innovative Sieve Technology
The ripple effects of advanced Mining Screen & Sieves extend beyond immediate productivity metrics. Modern sieve innovation impacts environmental sustainability by minimizing process water use—up to 22% less in certain gravity separation circuits—and maximizing resource recovery from lower-grade ores. Furthermore, process automation and digitalization contribute to workforce safety, as predictive maintenance reduces both scheduled and unscheduled manual interventions. New mesh alloys and surface treatments decrease the environmental footprint through increased lifecycle and recyclability, supporting circular economy goals. As regulations tighten and ore grades decline globally, leading mining firms are investing in sensor-integrated sieves and process analytics, with the global mining screen market projected to grow at a CAGR of 6.4% through 2028 (Allied Market Research, 2023). This trajectory underscores a dual mandate: advancing operational excellence while supporting responsible resource management.
Conclusion: Future Outlook on what are sieves used for in industrial contexts
As industrial challenges and resource constraints intensify, the answer to "what are sieves used for" will continue to evolve. Sieve technology, especially in the form of Mining Screen & Sieves for gold mining, represents a linchpin for material efficiency, environmental stewardship, and profitability. Ongoing innovation in mesh engineering, digital monitoring, and bespoke solutions sets new standards for performance and recovery. For manufacturers, adaptability and a focus on precision remain vital competitive differentiators. For mine operators, strategic investment in advanced sieving translates directly into lower costs and improved yields. The future promises even more integrated, sensor-driven systems that will redefine sieving’s role—not just as a separator, but as a pivotal enabler of next-generation mining operations. Ultimately, thorough understanding and thoughtful application of sieve technology will continue to drive success in industries where size, purity, and process reliability are the keys to value.
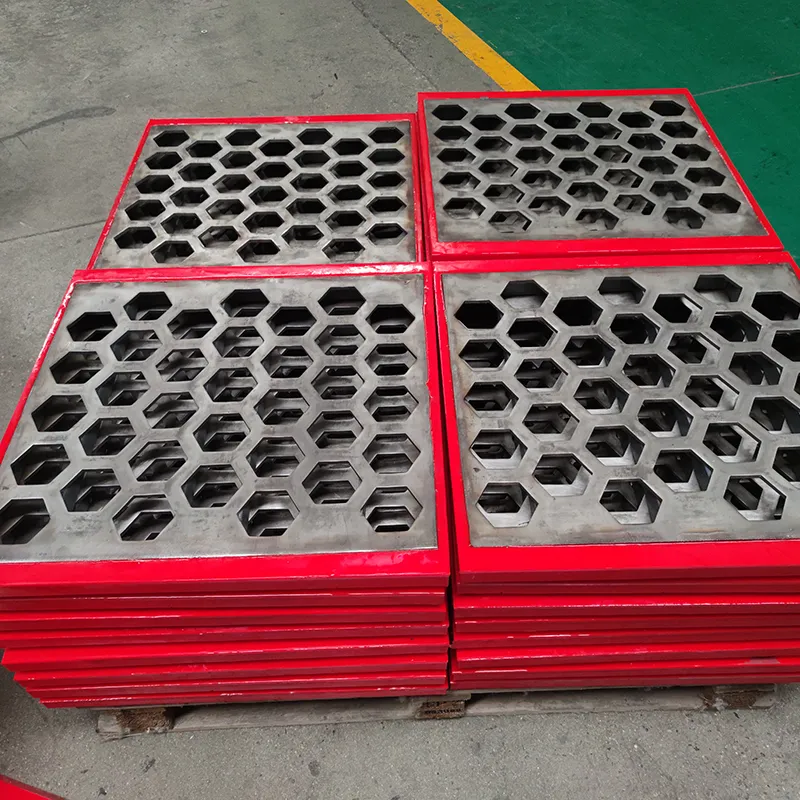
(what are sieves used for)