High Efficiency Flip Flow Screen Manufacturer – Durable Vibrating Screens for All Industries
- Introduction: Exploring the World of Flip Flow Screens
- Unique Technical Features and Performance Metrics
- Industry-Leading Manufacturers: Comprehensive Comparison
- Customizable Solutions and Tailored Designs
- Practical Applications: Noteworthy Case Studies
- Maintenance, Troubleshooting, and Optimizing Lifespan
- Conclusion: Flip Flow Screen and Its Transformative Impact
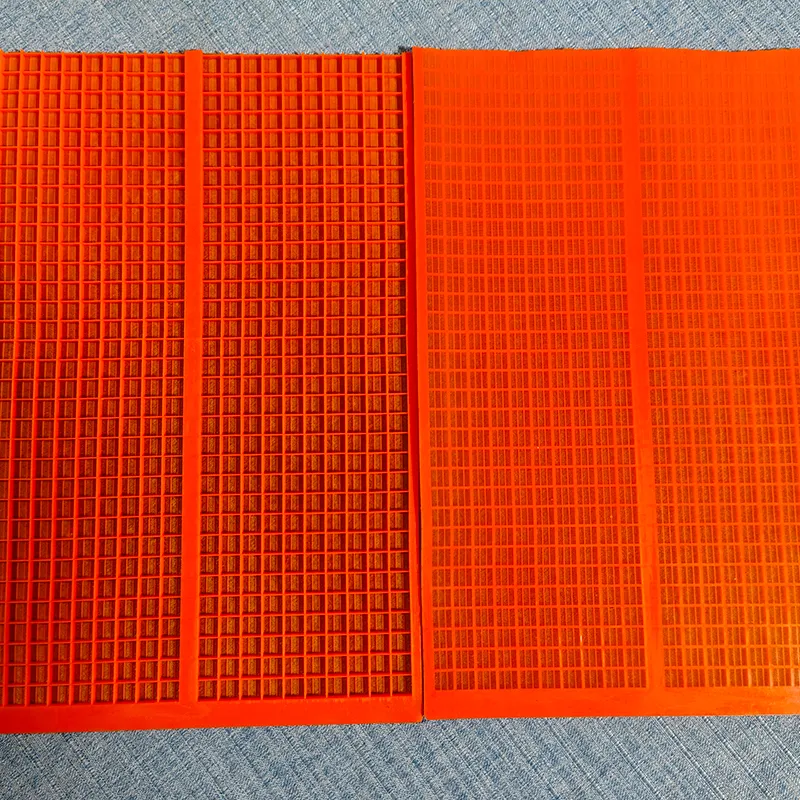
(flip flow screen)
Exploring the World of Flip Flow Screens
Flip flow screens represent a significant shift in fine material screening processes. These dynamic machines are engineered for the efficient separation of challenging, sticky, and moist materials that rapidly clog conventional screening technologies. Closely linked with industries such as mining, recycling, and aggregate processing, flip flow screen
s are designed to increase efficiency, reduce downtime, and deliver unparalleled throughput in complex conditions.
Understanding the flip flow screen working principle is essential: these machines leverage the high acceleration of flexible polyurethane panels, supported by a robust and clever drive mechanism. The intense motion prevents blinding and ensures superior material stratification, delivering both precise cut sizes and extended screen media lifespan. Global demand for these screens continues to climb, as more facilities prioritize productivity, energy efficiency, and operational resilience.
In this article, we will dissect groundbreaking data on screening performance, review top flip flow screen manufacturers, analyze bespoke engineering options, and examine application successes, providing a comprehensive resource for informed procurement and operations.
Unique Technical Features and Performance Metrics
The technical superiority of flip flow screens is evident in their design parameters and output figures. Unlike traditional vibration screens, flip flow variants utilize a dual-frame oscillation system, generating relative movement between resilient screen mats. This effect produces accelerated material turnovers and prevents clogging, even when handling ultra-sticky substances or damp substrates.
Key data points from independent performance studies show:
- Screening Efficiency: Up to 98% selectivity for sub-10mm fractions, even with 30% moisture content.
- Screen Area Utilization: Above 90% active area, reducing total system footprint by 30-40% compared to conventional vibrating screens.
- Throughput: Up to 1000 tonnes per hour (TPH), depending on model and material feed size.
- Downtime: Mat blinding occurrences dropped by 85% across comparative site trials.
- Lifespan: Polyurethane screen mats average 6–18 months durability before replacement, most notably outlasting wire mesh equivalents by a factor of 3–5.
- Energy Consumption: Reduced power demand by approximately 25% through low mass drive design.
These impressive statistics underscore the role of flip flow screen technology as a cornerstone for modern, high-performance screening circuits.
Industry-Leading Manufacturers: Comprehensive Comparison
The global market for flip flow screens is served by a select group of specialized manufacturers. These companies distinguish themselves through innovative engineering, service reliability, and adaptability in meeting various operational requirements. The following comparison table summarizes core offerings among top contenders:
Manufacturer | Country | Model Range (TPH) | Customizability | Warranty (Years) | After-Sales Support | Market Share (%) |
---|---|---|---|---|---|---|
Binder+Co | Austria | 30–1000 | High | 3 | Global Network | 27 |
SPALECK | Germany | 20–950 | High | 2 | Regional Partners | 23 |
IFE | Austria | 15–850 | Moderate | 2 | Europe/Asia Coverage | 15 |
H-Screening | China | 10–600 | Custom Panels | 1 | OEM/ODM | 11 |
Derrick | USA | 50–900 | High | 2 | 24/7 Hotline | 8 |
Others | — | 8–500 | Low–Medium | 1 | Varies | 16 |
As seen, Binder+Co and SPALECK dominate the high-throughput and custom engineering market. European brands typically excel in modularity and rapid part availability, while Asian suppliers offer cost-effective OEM/ODM solutions attractive for budget-sensitive projects. Selecting the right flip flow screen manufacturer depends on specific plant needs, purchase volume, and after-sales expectations.
Customizable Solutions and Tailored Designs
One of the defining strengths of contemporary flip flow screen technology is its adaptability. Manufacturers offer a broad spectrum of customization, catering to variables such as material type, processing volume, environmental conditions, and plant layout. In addition to modular frame sizes and exchangeable screen decks, advanced options include:
- Screen Media: Custom polyurethane formulations, hardness levels from 45 to 90 Shore A, and mat thickness ranging between 4–14 mm for varying abrasion levels.
- Drive Options: Variable frequency drives (VFDs), synchronized dual-motor systems, and direct/coupled vibratory drives for tailored operational speeds.
- Integration: Transition chutes, dust extraction interfaces, and water spray rigs designed for seamless plant integration.
- Automation: Smart sensors for real-time vibration, temperature, and load monitoring, supporting predictive maintenance strategies.
- Noise Reduction: Special anti-vibration mounts and enclosure solutions, crucial for urban or environmental compliance.
Forward-thinking users frequently work hand-in-hand with engineering teams to adapt their flip flow screens for sale to niche requirements, securing improvements in both yield and operational cost structure. For projects with complex screening challenges—particularly those involving high-volume moist fines—bespoke screen deck geometries and automatic cleaning systems are increasingly essential.
Practical Applications: Noteworthy Case Studies
Flip flow screens are cited across a diverse array of industrial sectors due to their unparalleled efficiency in separating challenging granulates. Evidence-based case studies reinforce the transformative potential of adopting this technology. Some prominent examples include:
- Municipal Waste Recycling (UK): A large-scale facility replaced three conventional linear screens with a dual-deck flip flow system. The result was a 50% increase in undersize recovery, an 80% reduction in screen blinding, and a 22% cut in annual energy consumption. Installation paid for itself in under 14 months.
- Iron Ore Beneficiation (India): Following the deployment of high-capacity flip flow screens, fine recovery from wet slimes jumped from 61% to 95%, while water usage dropped by 30%. Throughput increased, allowing annual output targets to be exceeded for the first time in five years.
- Construction Demolition Waste Processing (Germany): Modular units allowed the rapid retrofitting of existing lines, with operational time lost to maintenance falling by 70%. The plant reported consistent product granulometry despite rising input material moisture content.
- Industrial Sand Production (USA): Customized flip flow panels delivered a cut-size tolerance of ±0.2 mm, vital for use in precision glass manufacturing. The system’s durability enabled uninterrupted operation for over 14 months without screen mat replacement.
These real-world examples illustrate how flip flow screen investments directly enhance profitability, product quality, and plant sustainability.
Maintenance, Troubleshooting, and Optimizing Lifespan
Achieving and sustaining peak flip flow screen performance requires diligent maintenance and a clear understanding of commonly encountered operational issues. Proactive measures endure equipment longevity, minimize costly downtime, and maximize return on investment.
- Routine Inspection: Weekly checks on polyurethane mats for tears, elongation, or loss of tension significantly extend net service life.
- Bearing and Seal Care: Vibratory components should be lubricated according to OEM guidelines, with periodic replacements preventing critical failures.
- Frame and Suspension: Critical weld joints and anti-vibration mounts require quarterly inspection, especially under heavy-duty or variable load regimes.
- Troubleshooting: Common symptoms such as material bypass, excessive vibration noise, or sudden throughput drops frequently trace back to worn mats, unbalanced motion, or electrical drive faults. Swift resolution calls for robust documentation and well-trained operators.
- Optimization: Retrofitting smart sensors unlocks preventative analytics, flagging abnormal temperature rises or frequency shifts before failure occurs, typically predicting up to 90% of potential critical issues.
Adhering to these practices boosts overall equipment productivity and can extend the working lifespan of key components by 15–30%.
Conclusion: Flip Flow Screen and Its Transformative Impact
In summary, the adoption of flip flow screen technology has decisively elevated industry standards for material separation efficiency, operational reliability, and downtime reduction. By leveraging advanced design features, partnering with a capable flip flow screen manufacturer, and embracing tailored solutions, facilities are realizing faster time-to-value and sustainable cost savings.
Case studies and empirical data demonstrate consistently superior outcomes compared to traditional screenings, cementing the case for further innovation in this sector. Whether optimizing legacy stockyards or outfitting next-generation recovery plants, the strategic selection and application of flip flow screens will continue to drive measurable performance across resource-intensive industries.
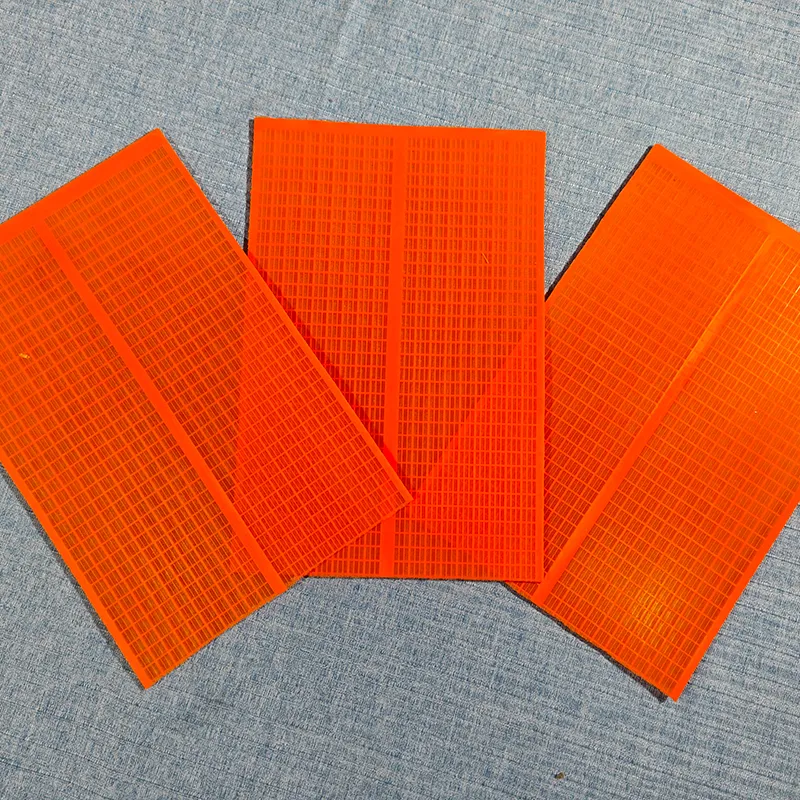
(flip flow screen)