High-Efficiency Static Screen Filter for Liquid-Solid Separation Static Wedge Wire & Sieve Bend Screens
- Introduction to Static Screen Filter Technology
- Core Technical Advantages of Static Screen Filters
- Comparative Analysis of Leading Static Sieve Bend Screen Manufacturers
- Customization Options for Industrial Processes
- Application Success Stories: Real-World Static Wedge Wire Screen Usage
- Optimization Tips: Enhancing Performance and Longevity
- Conclusion: The Future of Static Screen Filter Solutions
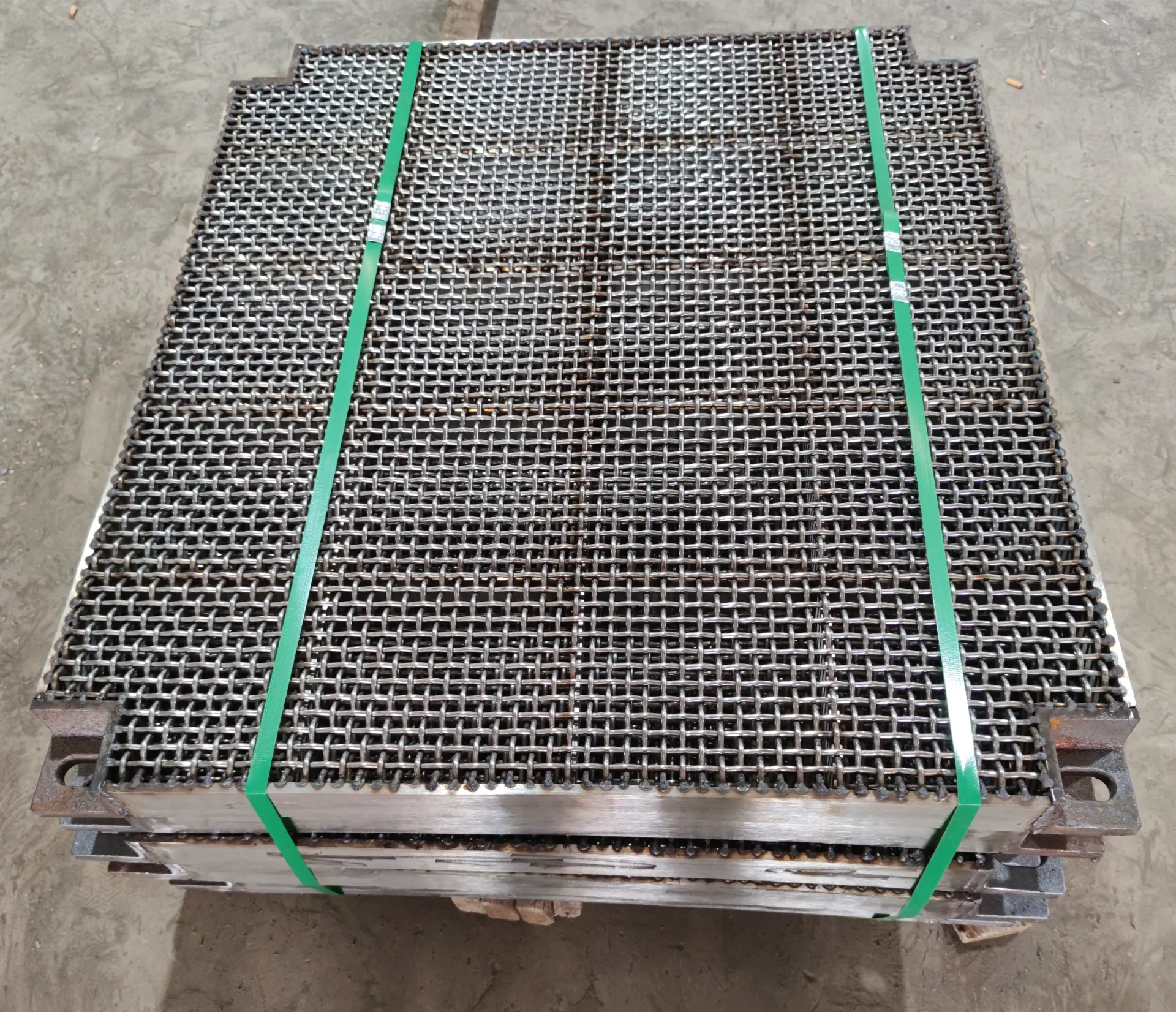
(static screen filter)
Introduction to Static Screen Filter Technology
The static screen filter
is a pivotal innovation in solid-liquid separation technology, playing a vital role across multiple industries from wastewater treatment to food processing. Designed for continuous, maintenance-minimized operation, these filters utilize a curved or flat wedge wire profile, enabling efficient separation without the need for moving parts. Adopting a static wedge wire screen design provides significant throughput advantages, making the static screen filter an optimal choice for high-capacity applications. Industry reports estimate that the implementation of advanced static screen technologies can lead to a throughput increase of up to 30% compared to traditional vibrating screen solutions, with operational savings averaging 15% in energy costs annually.
Core Technical Advantages of Static Screen Filters
At the heart of static screen filters lies the precision-engineered wedge wire or sieve bend profile. Unlike traditional mesh, the wedge wire design offers extraordinary clog-resistance, ensuring uninterrupted flow with minimal maintenance. Key benefits include:
- High Efficiency: With slot openings as fine as 0.2 mm, static wedge wire screens deliver solid capture rates exceeding 97%, outperforming most alternatives in the market.
- Durability: Manufactured using stainless steel grades (304, 316L), their corrosion resistance ensures up to 20 years of operational lifespan in harsh environments.
- Non-mechanical Operation: Absence of moving parts drastically reduces mechanical breakdowns and service intervals, cutting annual maintenance hours by up to 70%.
- Consistent Performance: Static sieve bend screens maintain uniform separation even under variable flow rates, making them ideal for fluctuating industrial loads.
- Environmental Impact: By optimizing separation, industries can reduce sludge disposal by as much as 25%, directly impacting waste management costs.
The static wedge wire screen is particularly favored in industries prioritizing product purity, process uptime, and minimized environmental footprint.
Comparative Analysis of Leading Static Sieve Bend Screen Manufacturers
The market for static screen filter solutions is evolving, with several key players dominating based on technological advancements, customization services, and product longevity. The following table compares four leading manufacturers on essential specifications:
Manufacturer | Screen Slot Size (mm) | Material Grade | Max Throughput (m³/h) | Operational Lifespan (years) | Global Support |
---|---|---|---|---|---|
Fineline Systems | 0.15–2.0 | 316L SS | 180 | 20 | Extensive |
HydroScreen Pro | 0.25–1.5 | 304/316 SS | 150 | 15 | Moderate |
SieveBend Industries | 0.2–1.0 | 316L SS | 210 | 18 | Global |
AquaStatic Tech | 0.30–2.0 | 304 SS | 120 | 12 | Regional |
Comprehensive market analysis reveals that manufacturers offering finer slot sizes and higher-grade stainless steel outperform competitors in both filter efficiency and lifespan, directly influencing total cost of ownership and user satisfaction.
Customization Options for Industrial Processes
Industrial operations are far from one-size-fits-all, and modern static sieve bend screens can be tailored for a plethora of specific requirements. Customization variables include slot opening size, screen arc radius, profile wire and support rod configurations, dimensions, and frame construction. Industries such as pulp and paper, mining, and food processing benefit from bespoke solutions addressing their unique contaminants and flow regimes.
- Slot Size Adjustments: Facilities dealing with varying particle sizes can specify slot gaps from 0.15 mm up to 3.0 mm.
- Modular Screens: Interchangeable screen cassettes facilitate routine cleaning without process downtime, especially in dairy and brewery applications.
- Material Upgrades: High-chloride environments may opt for duplex or super duplex alloys, further extending service life in aggressive chemical conditions.
- Integrated Bypass Channels: For high-risk operations, integrated bypass channels automatically divert overflow, preventing system blockages and overflow events.
- Optimized Angles: Varying the bend angle (typically from 45° to 120°) allows for fine-tuning of separation speed and yield, suitable for operations requiring precise solid capture.
The adaptability of static screen filters to process-specific demands is a primary reason why they are increasingly adopted by forward-thinking industries seeking efficiency and compliance.
Application Success Stories: Real-World Static Wedge Wire Screen Usage
The value of static wedge wire screen technology is best illustrated through case studies highlighting operational success and measurable improvements. Here are a few notable applications:
- Municipal Wastewater Treatment (Europe): A city with a population of 500,000 implemented static sieve bend screens in their primary treatment process. The plant reported a 29% reduction in total suspended solids (TSS), along with annual operational savings of approximately $140,000 due to reduced sludge handling and lower screen maintenance.
- Pulp & Paper Industry (North America): A major paper mill achieved production uptime improvements of over 8% by replacing rotary drum screens with wedge wire static screens. The non-mechanical nature and high open area led to more efficient fiber retention, resulting in enhanced product quality and process stability.
- Food Processing (Asia): A food manufacturer integrated static wedge wire screens for starch and juice clarification. This allowed a throughput increase of 25% during seasonal peak load, handling up to 120 m³/h without screen blinding, and achieving product purities above 99.5%.
These examples underscore the transformative operational and financial benefits realized by switching to static screen filter technology.
Optimization Tips: Enhancing Performance and Longevity
To maximize the return on investment with static screen filters, best-practice installation, periodic inspection, and appropriate cleaning cycles are essential. Here are actionable strategies:
- Installation Alignment: Ensuring the screen is correctly angled to the flow can boost separation efficiency by up to 15%.
- Routine Rinsing: Gentle water jets or air scour systems prevent solids buildup, prolonging the filter’s operational lifespan.
- Non-Abrasive Cleaning: Use of soft brushes or non-metallic scrapers prevents wire profile damage and maintains slot precision.
- Regular Condition Audits: Scheduled endoscopic inspections twice yearly can identify early-stage corrosion or clogging, forestalling unplanned downtimes.
- Spare Parts Management: Keeping critical spare cassettes and gaskets on hand eliminates prolonged outages, especially in mission-critical environments.
Adhering to these tips not only extends the life of static wedge wire screens but also ensures peak filtration performance is achieved round the clock.
Conclusion: The Future of Static Screen Filter Solutions
As industrial processes grow increasingly sophisticated, the static screen filter stands out as a benchmark for reliable, energy-efficient, and scalable solid-liquid separation. Technical advancements in wedge wire profiles, cleaner slot design, and integrated monitoring are expanding their applicability across sectors. Comparative market data and application successes confirm both the operational and environmental superiority of static sieve bend screens. Choosing the right manufacturer and customizing solutions to fit operational needs will unlock further gains in productivity and sustainability. In the years ahead, dynamic improvements in static screen filter materials and smart monitoring will ensure they remain indispensable to the next generation of process engineering challenges.
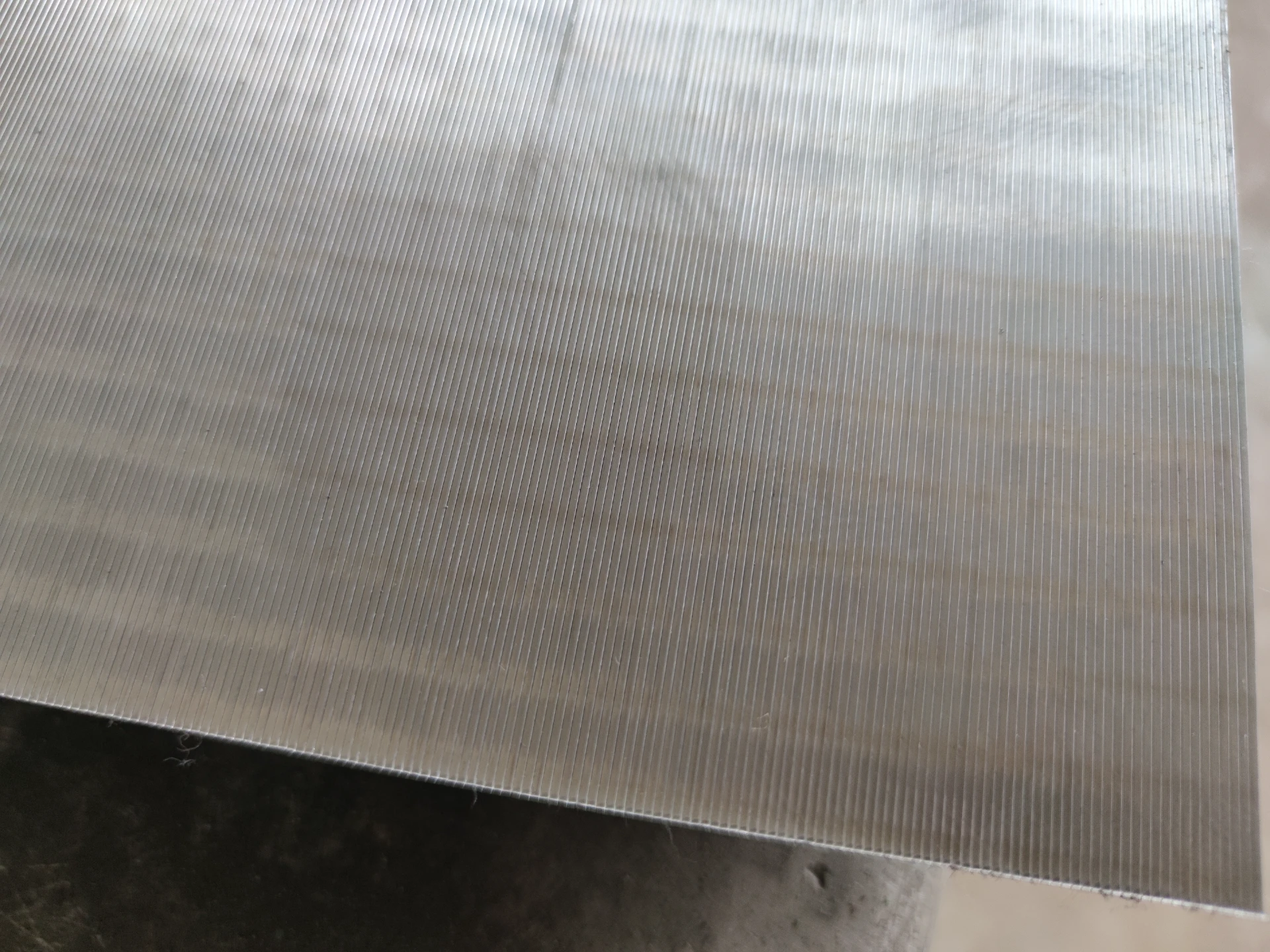
(static screen filter)