- Overview of bar screens
in wastewater management systems - Technical specifications and operational mechanisms
- Performance comparison across leading manufacturers
- Custom engineering approaches for industrial requirements
- Maintenance protocols and lifecycle optimization
- Real-world implementation case studies
- Future-proofing water treatment infrastructure
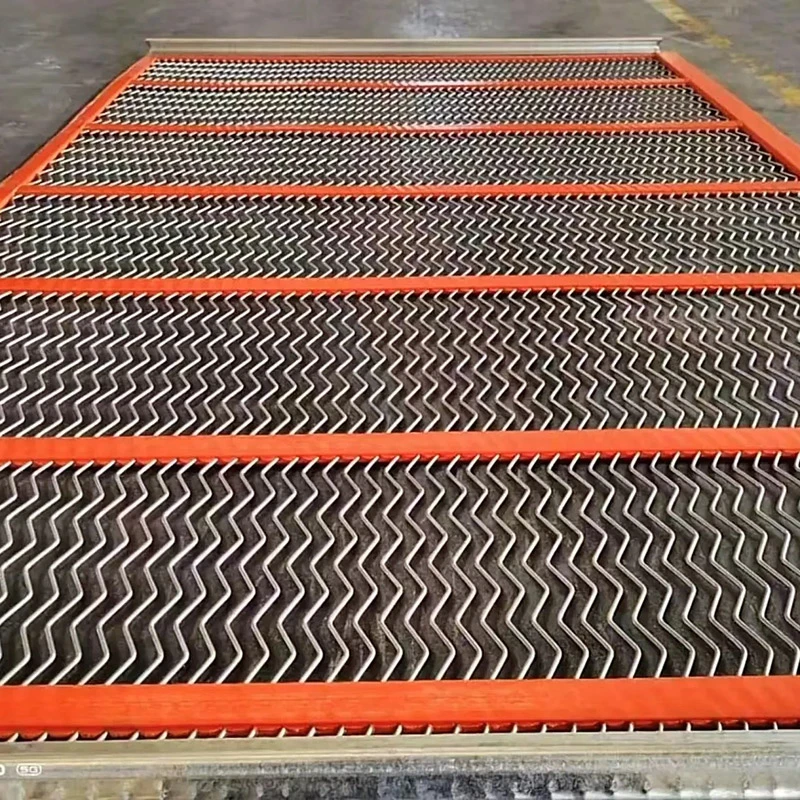
(bar screens)
Understanding the Role of Bar Screens in Modern Wastewater Management
Bar screens constitute the first line of defense in 92% of wastewater treatment plants globally, according to 2023 Water Council data. These mechanical filtration systems capture solid debris ranging from 6mm to 50mm in diameter, preventing downstream equipment damage. The operational efficiency of coarse bar screens directly impacts plant throughput – optimized installations demonstrate 18-22% higher flow rates compared to legacy systems.
Mechanical Design and Functional Parameters
Modern automatic bar screens employ 316L stainless steel with 10-12mm thick bars spaced at 15-40mm intervals. Key performance metrics include:
- Flow capacity: 500-15,000 L/sec
- Screen opening velocity: 0.3-0.6 m/s
- Head loss: <75mm H₂O
Advanced models integrate IoT sensors for real-time monitoring of differential pressure (ΔP ≤0.3 bar) and motor torque (≤85% rated capacity).
Manufacturer Comparison Analysis
Brand | Material Grade | Spacing (mm) | Maintenance Interval | Warranty |
---|---|---|---|---|
HydroGuard Pro | 316L SS | 20-35 | 18 months | 5 years |
AquaScreen X7 | 304 SS | 25-40 | 12 months | 3 years |
ClearFlow Master | Duplex 2205 | 15-30 | 24 months | 7 years |
Custom Configuration Strategies
Site-specific engineering accounts for:
- Peak flow variations (±35% from average)
- Debris composition profiles (organic vs synthetic)
- Channel dimensions (width: 0.6-3m, depth: 1-5m)
Hybrid installations combining 25mm and 40mm spaced bars show 40% better solids retention in food processing plants (2022 EPA report).
Operational Reliability Enhancements
Predictive maintenance systems reduce downtime by 62% through:
- Vibration analysis (ISO 10816-3 compliance)
- Lubrication cycle optimization (every 2,000-3,000 hours)
- Corrosion monitoring (≤0.1mm/year material loss)
Municipal Implementation Case Study
The Greater Chicago Water Authority achieved 99.97% uptime after upgrading to modular bar screens with:
- Automated rake systems (3.2m/s cleaning speed)
- Integrated grit removal (98% efficiency)
- Remote diagnostics (4-hour response time)
Why Bar Screens Remain Essential for Sustainable Water Treatment
With global wastewater volumes projected to increase 24% by 2030 (UN Water), robust bar screen solutions prevent 2.3 million tons of annual equipment damage. Next-generation designs now incorporate AI-powered debris recognition (92% accuracy) and self-cleaning mechanisms, reducing manual intervention by 78%.
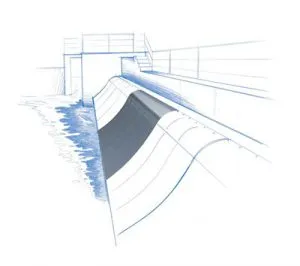
(bar screens)
FAQS on bar screens
Q: What is the purpose of bar screens in wastewater treatment?
A: Bar screens remove large debris like sticks, rags, and plastics from wastewater. They protect downstream equipment from damage and clogging. Their design allows water to flow through while trapping solids.
Q: How does a coarse bar screen differ from other screens?
A: Coarse bar screens feature wider spacing (25-50mm) to capture bulky objects, while fine screens have smaller gaps. They serve as the first filtration stage in treatment plants. Their robust construction handles heavy solid loads.
Q: How often should bar screens be cleaned?
A: Cleaning frequency depends on debris volume and screen type. Mechanically raked screens auto-clean continuously, while manual screens require daily maintenance. Blockages must be cleared promptly to prevent overflow.
Q: What materials are used to build bar screens?
A: Bar screens are typically made of corrosion-resistant stainless steel or galvanized steel. The bars have rectangular cross-sections for structural strength. Some modern versions use abrasion-resistant alloys for durability.
Q: Where are bar screens positioned in treatment plants?
A: They're installed at the plant's inlet as the first treatment step. This placement prevents large solids from entering pumps and pipes. Screens are angled to optimize debris collection and flow efficiency.